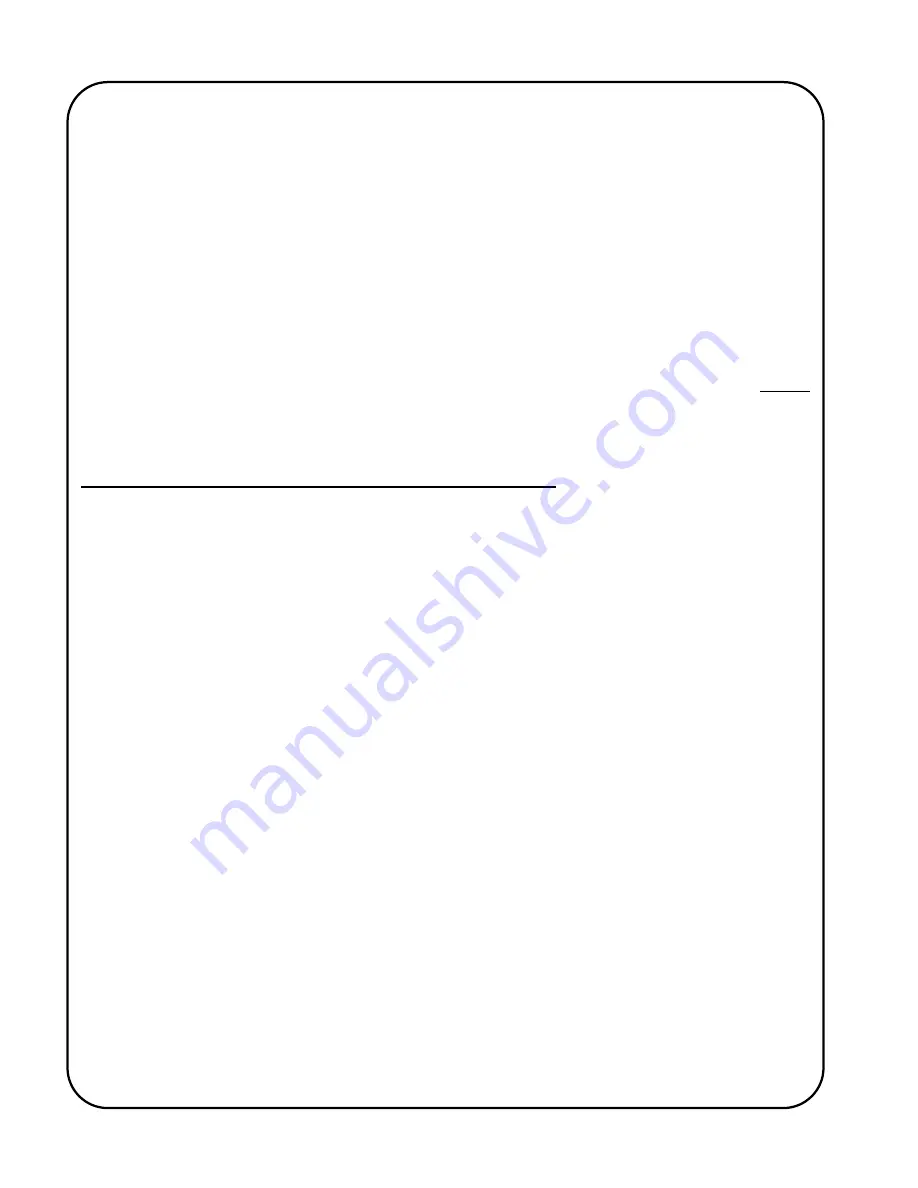
28
1. All operators of the KBM
®
-18 machine must have a thorough understanding of how the
machine and material are set up for proper operation and that proper operational procedures
are followed.
2.
Perform trial runs before the actual application. This is particularly important.
Most cutter
troubles are encountered at the start or finish of the operation.
3.
Remember that the misapplication of stress to the cutter will damage or break it. Plates
should be fed square to the cutter. Twisting forces should not be applied to the cutter. Large
and unbalanced pieces should be properly supported so that the material is always positioned
square to the cutter. This is particularly true when bevelling circular discs or curved plates.
Worn and dull cutters may produce a coarse bevelled surface, create feeding problems and tend to
be broken more easily. It is recommended that the cutters be re-sharpened or replaced
before
these conditions occur. If a few extra cutters were kept on-hand, it would allow a frequent rotation
or replacement of the cutters without delays and significant down time, which would ultimately
reduce the total bevelling costs.
SHARPENING INSTRUCTIONS FOR KBM
®
-18 CUTTERS
Normally up to 10 re-grinds can be performed before the cutters 0.110" [2.8 mm] recess is ground
flat. When resurfacing GBM-18 & KBM
®
-18 cutters, the following instructions will help to provide
the maximum cutter life:
1.
The cutter should be surface ground until all of the burred and dulled edges of the flutes are
removed.
2.
The recommended grinding wheel is a "Carborundum, S.G. Medalist, 461 Grit" or equivalent.
3.
The manufacturers recommended cutting oil, if any, for the grinding medium to be used,
should be applied when grinding (the above recommended grinding wheel performs best with
no cutting oil).
4.
Never allow the cutter to overheat when grinding.
5.
The last pass/passes of the resurfacing process should be light enough to ensure that all the
burrs that have been produced due to the grinding process, are removed. This is important, as
large burrs around the cutting edges may dull or possibly deform the cutter immediately on
reuse.
6.
Ensure that the back face of the cutter is smooth and clean before grinding and that the front
face of the cutter is parallel to within 0.001" [0.03mm] of the back face after grinding.
7.
Demagnetize the
cutter before reuse.
IMPORTANT: If the Gullco KBM
®
-18 cutter is resurfaced below the original recess, or if
cutters other than those approved by Gullco International are used on the
Gullco KBM
®
-18 Portable Plate Edge Bevelling Machine, the warranty will be
void.
Содержание KBM-18
Страница 2: ......
Страница 8: ...4 KBM 18 080 UNDERCARRIAGE ...
Страница 23: ...19 22 5º 30º 22 5º BEVEL ARRANGEMENT 30º BEVEL ARRANGEMENT ...
Страница 24: ...20 37 5º 45º 37 5º BEVEL ARRANGEMENT 45º BEVEL ARRANGEMENT ...
Страница 25: ...21 55º 55º BEVEL ARRANGEMENT ROOT FACE SCALE EXAMPLES ...
Страница 42: ...38 KBM 18 100 GENERAL ASSEMBLY BREAKDOWN Drawing Number KBM 18 100 ...
Страница 43: ...39 KBM 18 100 GENERAL ASSEMBLY BREAKDOWN Drawing Number KBM 18 100 ...
Страница 45: ...41 PIVOT ARM ASSEMBLY BREAKDOWN Part Number KBM 18 213 ...
Страница 46: ...42 SLIDE BASE ASSEMBLY BREAKDOWN Part Number KBM 18 212 ...
Страница 49: ...45 STARTER ASSEMBLY BREAKDOWN Drawing Number KBM 18 214 ...
Страница 50: ...46 MANUAL STARTER ASSEMBLY BREAKDOWN Drawing Number KBM 18 215 1 2 3 ...
Страница 54: ...50 OPTIONAL HYDRAULIC UNDERCARRIAGE ASSEMBLY BREAKDOWN Part Number KBM 18 080 ...
Страница 55: ...51 OPTIONAL HYDRAULIC UNDERCARRIAGE ASSEMBLY BREAKDOWN Part Number KBM 18 080 ...
Страница 56: ...52 OPTIONAL UNDERCARRIAGE ASSEMBLY BREAKDOWN Part Number KBM 18 069 ...
Страница 57: ...53 KBM 18 WIRING SCHEMATIC Drawing Number KBM 18 215 SCH ...
Страница 60: ...www GULLCO com ...