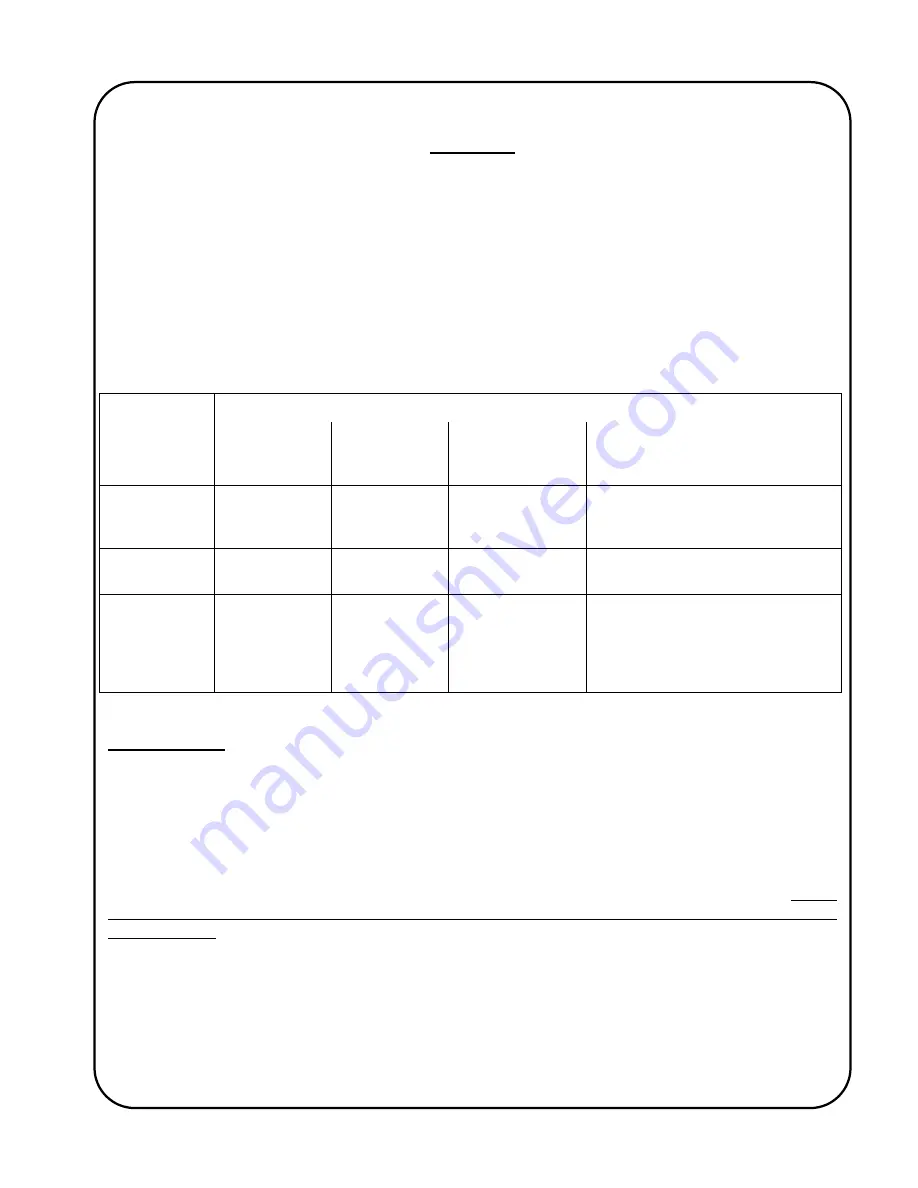
27
CUTTER
The circular cutter on the Gullco KBM
®
-18 bevelling machine is made from special, high strength
and abrasion resistant tool steel and is designed to withstand the heavy stresses applied during
normal bevelling operations. All cutters are heat treated to provide maximum cutter life. The
specifically designed serrated cutting edge provides a firm grip on the material for both feeding and
cutting purposes.
Three (3) types of cutters are available for use with the KBM
®
-18. The table below shows the basic
features of each cutter. It is important to note that the properties of different materials will respond
differently to each other with respect to rotary shearing. Therefore the following is only intended as
a guideline. It is Gullco's recommendation that the best cutter for the project be found by trial and
experimentation.
AVAILABLE
CUTTERS
CUTTER PROPERTIES
FEEDABILITY
BEVEL
FINISH
IMPACT/HARD
SPOT
RESISTANCE
FEATURES
KBM
®
-18-X1C GOOD EXCELLENT
GOOD
TOUGHER, MORE DURABLE,
MORE FORGIVING OF MINOR
IMPROPER SETUP/OPERATION
KBM
®
-18-X1H GOOD
GOOD
FAIR
HARDER, BETTER WEAR
RESISTANCE
KBM
®
-18-X1A EXCELLENT
FAIR
LOW
HARD, AGGRESSIVE CUTTER
PERFORMS WELL UNDER
PERFECT CONDITIONS, BUT
WILL FAIL IF NOT PROPERLY
SETUP/OPERATED
CUTTER LIFE
KBM
®
-18 cutters are subject to wear under normal working conditions and should be re-ground at
regular intervals, as per the procedure described later in this manual. The service life of the cutter,
before resurfacing or replacement is necessary, depends on a number of factors. The tougher the
plate material, the shorter the expected service life. It is also shortened by heavier cuts and greater
bevelling angles. However, the most important factor contributing to premature failure of the cutter
is misapplication of heavy stress to the cutter. How and why this occurs is described later in this
manual. Generally, it involves errors relative to the proper setup and use of the machine. A well
experienced operator will obtain a much longer service life from the cutter than indicated in the
“guide” below. An inexperienced operator may experience cutter failure after only a few feet
[meters] of cut. The following re-grinding schedule is provided as a guide:
-
Mild Steel
-
Re-grind after bevelling 600 feet (182 meters)
-
Stainless Steel
-
Re-grind after bevelling 300 feet (91 meters)
The most effective way to obtain maximum cutter life is:
Содержание KBM-18
Страница 2: ......
Страница 8: ...4 KBM 18 080 UNDERCARRIAGE ...
Страница 23: ...19 22 5º 30º 22 5º BEVEL ARRANGEMENT 30º BEVEL ARRANGEMENT ...
Страница 24: ...20 37 5º 45º 37 5º BEVEL ARRANGEMENT 45º BEVEL ARRANGEMENT ...
Страница 25: ...21 55º 55º BEVEL ARRANGEMENT ROOT FACE SCALE EXAMPLES ...
Страница 42: ...38 KBM 18 100 GENERAL ASSEMBLY BREAKDOWN Drawing Number KBM 18 100 ...
Страница 43: ...39 KBM 18 100 GENERAL ASSEMBLY BREAKDOWN Drawing Number KBM 18 100 ...
Страница 45: ...41 PIVOT ARM ASSEMBLY BREAKDOWN Part Number KBM 18 213 ...
Страница 46: ...42 SLIDE BASE ASSEMBLY BREAKDOWN Part Number KBM 18 212 ...
Страница 49: ...45 STARTER ASSEMBLY BREAKDOWN Drawing Number KBM 18 214 ...
Страница 50: ...46 MANUAL STARTER ASSEMBLY BREAKDOWN Drawing Number KBM 18 215 1 2 3 ...
Страница 54: ...50 OPTIONAL HYDRAULIC UNDERCARRIAGE ASSEMBLY BREAKDOWN Part Number KBM 18 080 ...
Страница 55: ...51 OPTIONAL HYDRAULIC UNDERCARRIAGE ASSEMBLY BREAKDOWN Part Number KBM 18 080 ...
Страница 56: ...52 OPTIONAL UNDERCARRIAGE ASSEMBLY BREAKDOWN Part Number KBM 18 069 ...
Страница 57: ...53 KBM 18 WIRING SCHEMATIC Drawing Number KBM 18 215 SCH ...
Страница 60: ...www GULLCO com ...