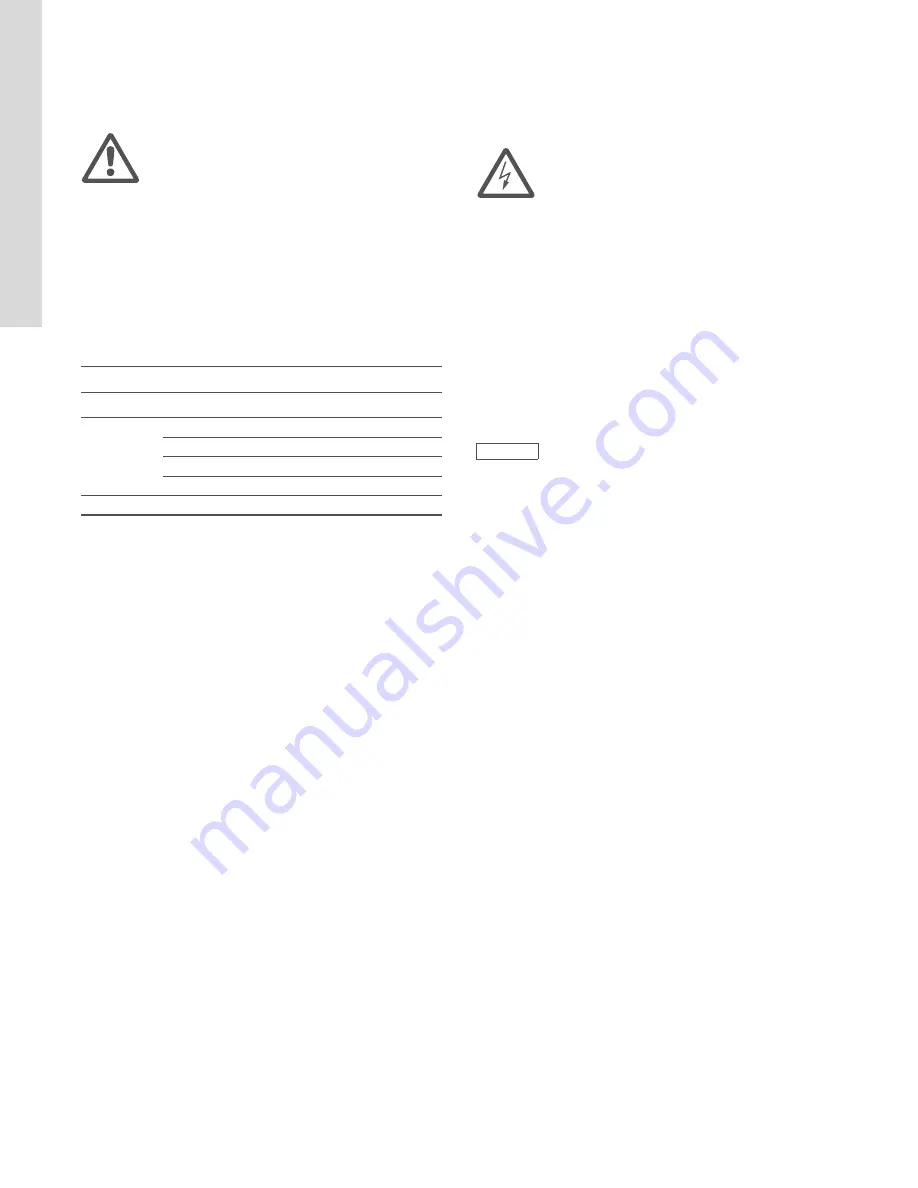
Eng
lish (US)
8
7. Maintenance
7.1 Motor lubrication
Always follow motor manufacturer's lubrication instructions if
available, and periodically check grease fittings and drain plugs
for leaks. Use the standard lubrication interval, see installation
and operating instructions or the lubrication plate on the E-motor.
If lubricating instructions do not accompany motor, refer to for
recommended lubrication periods.
Standard conditions:
8 hours per day operation, normal or light loading, clean air,
100 °F, maximum ambient temperature.
Severe conditions:
Continuous 24-hour operation, shock loading or vibration, poor
ventilation, 100-150 °F, ambient temperature.
Extreme conditions:
Continuous operation, heavy shock or vibration, dirt or dust in air,
extreme ambient temperature.
8. Disassembly
8.1 Preparation for disassembly
Complete disassembly instructions are outlined below.
Proceed only as far as required to perform the maintenance work
needed. Close valves on suction and discharge side of pumps
and drain pump, taking precautions as necessary based on fluid
being pumped. Flush, if necessary. Allow adequate working area
around pump for maintenance or disassembly.
8.2 Seal replacement (VLSE)
1. Complete preparations noted.
2. Remove coupling guard (34F).
3. Remove coupling bolts (8E). Pry apart the coupling halves
(23D), remove keys (12B) and set aside.
4. Unscrew tubing connector from pipe tee of air vent assembly.
Pipe dope is applied to threads during factory assembly, and
resulting bond may retard but will not prevent manual
disassembly.
5. Remove seal cap bolts and slide seal cap (2N) up shaft to
remove.
6. Remove seal head assembly manually from shaft (6A).
Water-soluble lubricant may be applied to shaft to ease
removal of shaft seal (14A). Pull seal head assembly manually
from shaft, using slight twisting motion (as necessary) to
loosen bellows from shaft.
7. Remove and discard seal spring and retainer.
8. remove and discard seal seat from seal cap (2N) and
thoroughly clean the inside cavity of seal cap.
9. Interior surface of bellows on new seal head is coated with
bonding agent that adheres to motor shaft. When old seal
head is removed, bonding agent no longer exists and bellows
may crack or split during removal. Installation of new
mechanical seal is always recommended if it becomes
necessary to remove existing seal from shaft.
10. Clean and lubricate shaft (6A) with water-soluble lubricant and
make sure no sharp edges exist to cut or scratch bellows of
new seal.
11. Press new seal seat firmly into seal cap. Avoid direct contact
of seal face with metallic or abrasive objects and wipe clean
after installation to ensure abrasive free sealing surface.
12. Slide new seal head assembly onto shaft by applying even
pressure to base of assembly.
13. Install seal cap (2N) down shaft.
14. See reassembly instructions.
Warning
Do not attempt any maintenance, inspection,
repair or cleaning in the vicinity of rotating
equipment. Before attempting any inspection or
repair on the pump, the driver controls must be in
the "OFF" position, locked and tagged to prevent
injury to personnel performing service on the
pump. Inspection, maintenance and repair should
be performed by trained, qualified personnel
only.
Motor RPM
Motor HP
Operating conditions
Standard
Severe
Extreme
1750
0.33 - 7.50
3 yrs
1 yr
6 mo
10 - 40
1 - 3 yrs
6 mo - 1 yr
3 mo
50 - 150
1 yr
6 mo
3 mo
200 and up
1 yr
6 mo
3 mo
above 1750
all hp
6 mo
3 mo
3 mo
Warning
Turn off power, lock-out electrical breaker and
provide appropriate "Do Not Operate" or
equivalent signage prior to any work on
equipment. Verify all power is off at pump using
appropriate electrical instrumentation.
Work should be performed only by qualified and
trained personnel.
1
1RWH
1
1RWH
Mark or measure the original position of the
pump coupling on the motor side.
Содержание VLSE
Страница 2: ...Table of contents 2 VLSE Pump Information 3 Motor information 12...
Страница 44: ...44...
Страница 45: ...45...
Страница 46: ...46...