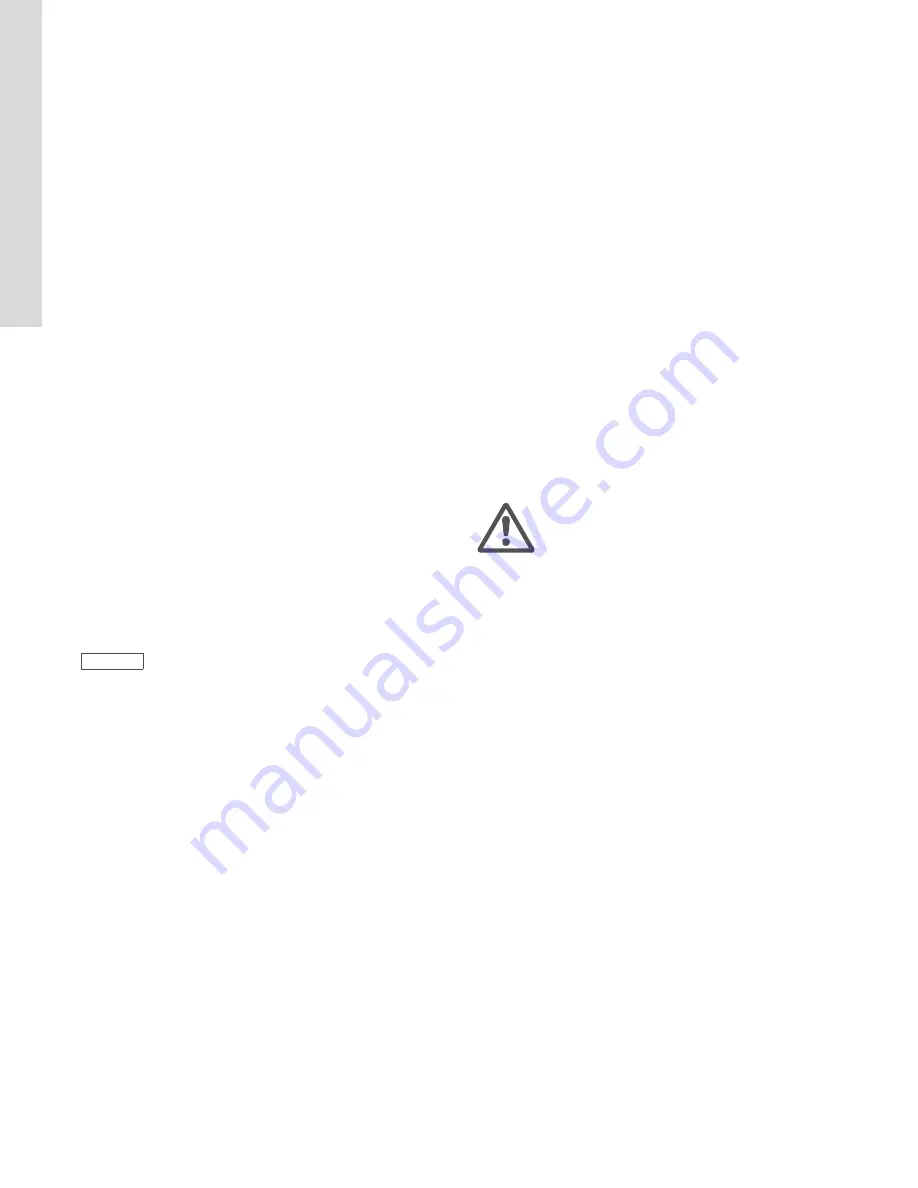
Eng
lish (US)
6
Install a valve in the suction line to isolate the pump during
shutdown and maintenance, and facilitate pump removal.
Where two or more pumps are connected to the same suction
line, install a valve for each pump to isolate pump from the line.
Valves should always be installed in positions that avoid air
pockets. Globe valves should not be used, particularly when
NPSH is critical. During pumping operation, valves on suction line
must always be at FULL OPEN. Properly sized pressure gauges
can be installed in gauge taps on pump suction and discharge
nozzles. Gauges enable the operator to monitor pump
performance and determine that the pump conforms to the
parameters of the performance curve. If cavitation, vapor binding,
or other unstable operation occurs, pressure gauges will indicate
wide fluctuation in suction and discharge pressures. Gauge cocks
are recommended for use with pressure gauges, to protect
gauges from constant wear and vibration when not in use.
4.10 Discharge (outlet) piping
Short discharge piping can be the same diameter as the pump
discharge opening. Longer piping should be one or two sizes
larger depending on length. An even gradient is best for long
horizontal runs of discharge piping. Install a valve near the
discharge opening to prime and start the pump. The discharge
gate valve is also used to isolate the pump during shutdown,
maintenance, and facilitate pump removal. Any high points in
discharge piping may entrap air or gas and thus retard pump
operation.
4.11 Shaft sealing - general comments
Grundfos Type VLSE pumps are equipped with mechanical shaft
seals.
4.12 Mechanical seals
Grundfos mechanical seals are matched to conditions for which
the pump was sold. Unlike packing, mechanical seals require no
field adjustments. Observe the following precautions to avoid seal
damage and obtain maximum seal life: Do not exceed
temperature or pressure limitations for the mechanical seal used.
Clean and purge suction piping in new installations before
installing and operating pump. Pipe scale, welding slag and other
abrasives can cause rapid seal failure.
5. Installation-electrical
5.1 Motors general
The motor control circuit must have the following components in
order to comply with the National Electrical Code.
• Motor Disconnecting Device: A motor disconnecting device
must be installed that is capable of disconnecting both the
controller (motor starter) and the motor from their source of
power.
• The disconnecting device must be located so that the
controller (motor starter) can be seen from the disconnecting
means. In all cases, the distance from the disconnecting
device to the controller must be less than 50.
• In most installations the disconnecting device will be a circuit
breaker or fusible disconnect switch.
Motor short circuit and ground fault protection:
• Short circuit and ground fault protection are usually provided
by means of a circuit breaker or fusible disconnect switch.
• The selection of the size of the circuit breaker or fuse must be
in accordance with Section 430-52 and Table 430-152 of the
National Electrical Code.
Motor controller with running over current protection (magnetic
starter):
• These components must be installed in accordance with
applicable local and state electrical codes in addition to the
National Electrical Code.
&DXWLRQ
Do not run the pump dry or against a closed
valve! Dry operation will cause seal failure within
minutes.
Warning
Whenever powered equipment is being used in
explosive surroundings, the rules and
regulations generally or specifically imposed by
the relevant responsible authorities or trade
organizations must be observed.
Содержание VLSE
Страница 2: ...Table of contents 2 VLSE Pump Information 3 Motor information 12...
Страница 44: ...44...
Страница 45: ...45...
Страница 46: ...46...