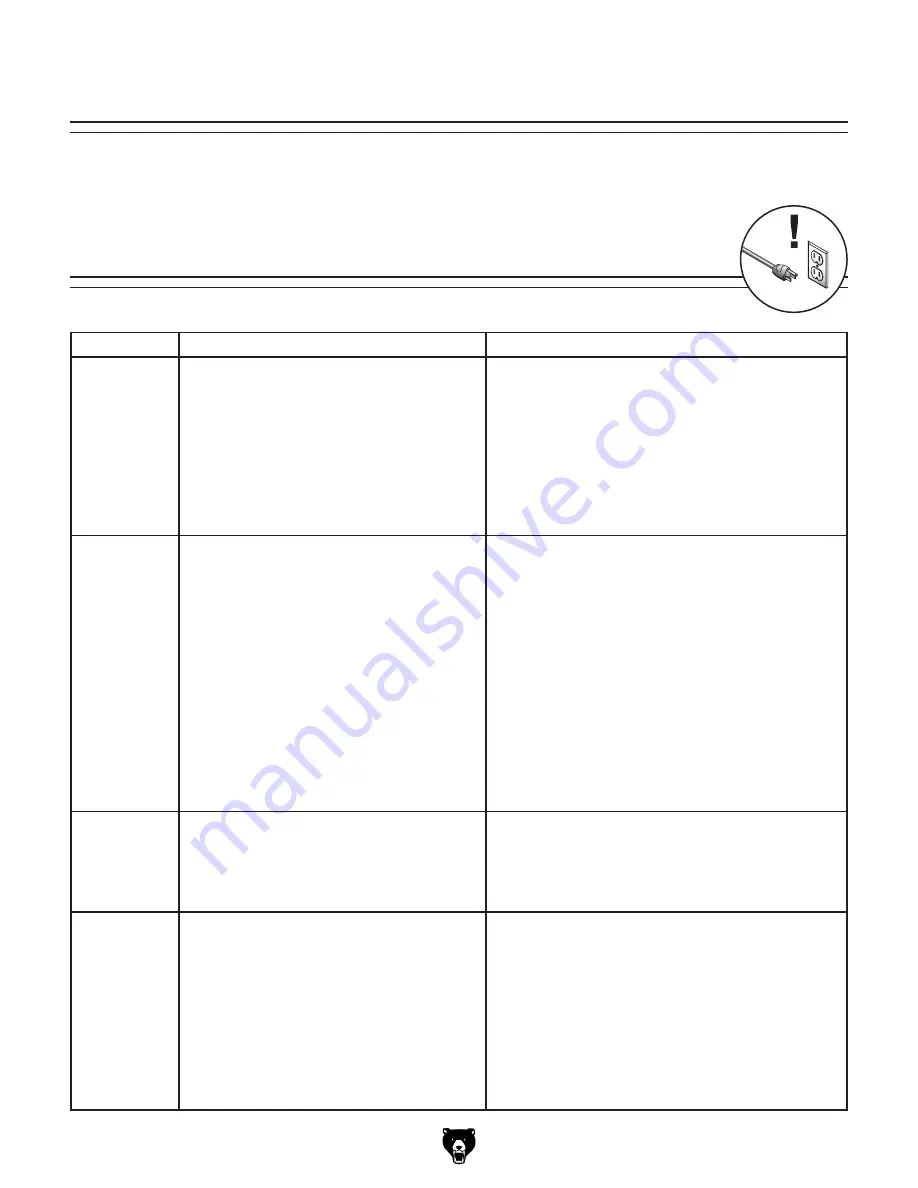
Model G0879 (Mfd. Since 6/19)
-31-
Review the troubleshooting procedures in this section if a problem develops with your machine. If you need
replacement parts or additional help with a procedure, call our Technical Support.
Note: Please gather the
serial number and manufacture date of your machine before calling.
SECTION 7: SERVICE
Troubleshooting
Motor & Electrical
Symptom
Possible Cause
Possible Solution
Machine does
not start, or
power supply
breaker
immediately
trips after
startup.
1. Thermal overload has tripped/duty cycle
exceeded.
2. Incorrect power supply voltage or circuit size.
3. Power supply circuit breaker tripped or fuse
blown.
4. Blown fuse.
5. Wiring broken, disconnected or corroded.
6. ON/OFF switch at fault.
1. Rest. Allow machine to cool with fan ON (
Page 22).
2. Ensure correct power supply voltage and circuit size.
3. Ensure circuit is free of shorts. Reset circuit breaker or
replace fuse (see
Page 30).
4. Replace fuse/ensure no shorts.
5. Fix broken wires or disconnected/corroded
connections.
6. Replace switch.
Wire does not
feed properly or
does not feed
at all.
1. Machine has run out of wire.
2. Incorrect contact tip size.
3. Insufficient wire feed spring tension.
4. Wire guide sheath/contact tip in welding torch
assembly is blocked.
5. Wire spool nut is too tight/too loose.
6. Wire spool has oxidized or poorly wound wire.
7. Wire burned back and welded to contact tip.
8. Duty cycle exceeded.
9. Drive roller groove does not match wire
gauge.
1. Replace welding wire spool (
Page 16).
2. Match contact tip to wire gauge.
3. Tighten tension knob (
Page 21).
4. Clean wire sheath; replace contact tip; replace welding
torch assembly.
5. Adjust nut so spool moves freely (
Page 16).
6. Replace welding wire spool (
Page 16).
7. Replace contact tip. DO NOT run trigger. This will
unravel wire spool.
8. Leave machine plugged in; allow to cool until orange
light goes out, then attempt to power up machine again.
9. Match drive roller groove to wire gauge (
Page 21).
Reduced
welding power.
1. Ground cable is not connected or is poorly
connected.
2. One or more rectifiers failed.
3. If using extension cord, cord is too long.
1. Check ground cable for proper connection (
Page 13).
2. A qualified welding technician should open unit and
check for burnt rectifiers.
3. Use a shorter extension cord or none at all.
Inconsistent
welding circuit.
1. Improperly cleaned workpiece/ wrong type of
material.
2. Incorrect size of contact tip for wire.
3. Contact tip loose.
4. Contact tip damaged.
5. Feed rollers are worn.
6. Welding wire corroded.
7. Ground clamp not connected to workpiece/
too far from weld location/bad ground
connection.
1. Clean workpiece/ use correct type of material.
2. Replace with correct contact tip (
Page 20).
3. Tighten contact tip.
4. Replace with new contact tip.
5. Replace worn components.
6. Replace welding wire spool (
Page 16).
7. Connect the ground clamp close to your workpiece.
Make sure ground clamp is connected/terminals are
clean.
Содержание G0879
Страница 36: ......