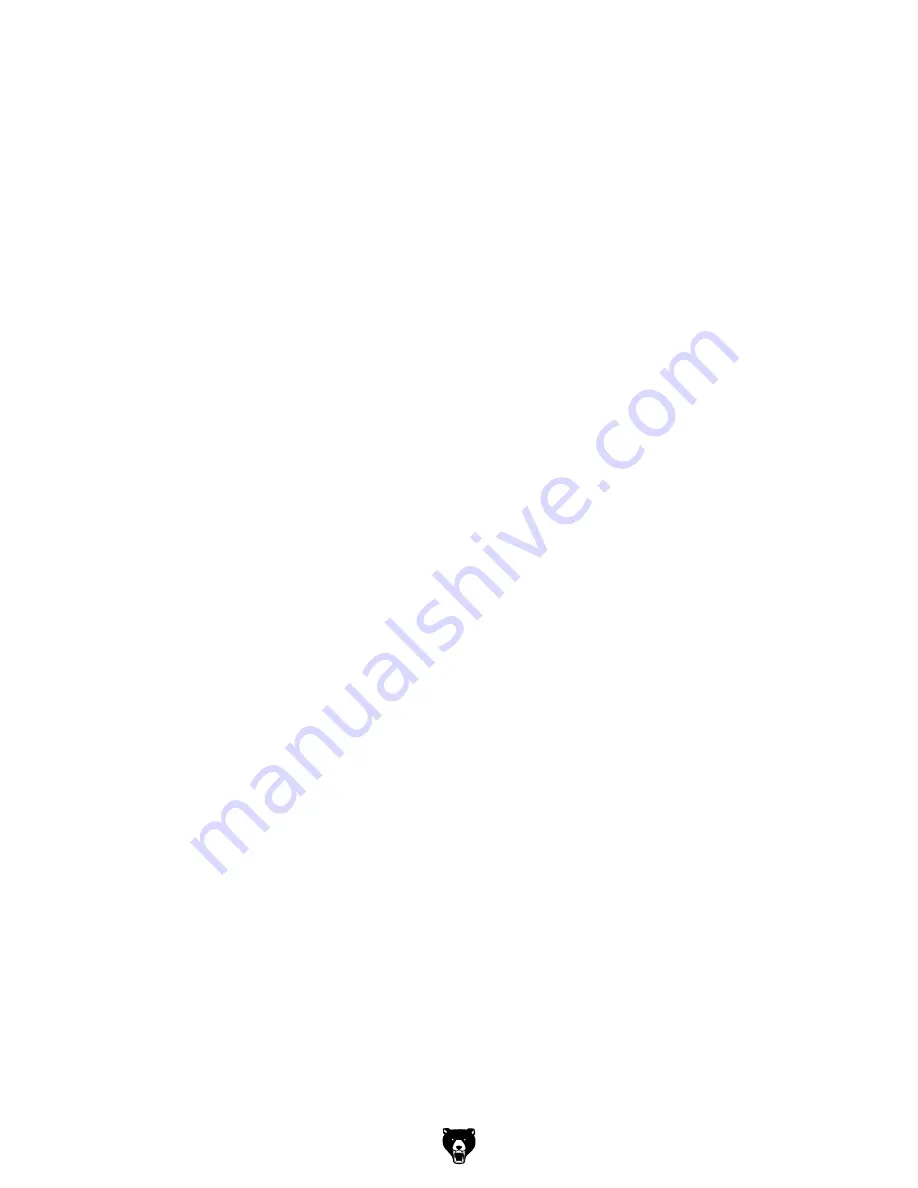
Model G0835 (Mfd. Since 11/17)
-3-
The information contained herein is deemed accurate as of 4/2/2018 and represents our most recent product specifications.
Due to our ongoing improvement efforts, this information may not accurately describe items previously purchased.
PAGE 2 OF 3
Model G0835
Spindle Information
Spindle Taper............................................................................................................................................ MT#2
Spindle Thread Size.................................................................................................................. 1-1/4 in. x 8 TPI
Spindle Thread Direction.................................................................................................................. Right-Hand
Spindle Bore......................................................................................................................................... 0.625 in.
Type of Included Spindle Center................................................................................................................. Spur
Indexed Spindle Increments.................................................................................................................. 7.5 deg.
No of Indexes................................................................................................................................................. 48
Outboard Spindle Thread Direction............................................................................................................ Right
Outboard Spindle Size........................................................................................................................... 1-1/4 in.
Outboard Spindle TPI................................................................................................................................ 8 TPI
Tool Rest Information
Tool Rest Width................................................................................................................................... 14-1/4 in.
Tool Rest Post Diameter.............................................................................................................................. 1 in.
Tool Rest Post Length......................................................................................................................... 5-5/16 in.
Tool Rest Base Height......................................................................................................................... 2-5/16 in.
Tailstock Information
Tailstock Taper.......................................................................................................................................... MT#2
Type of Included Tailstock Center............................................................................................................... Live
Construction
Bed....................................................................................................................................................... Cast Iron
Frame................................................................................................................................................... Cast Iron
Stand.................................................................................................................................................... Cast Iron
Headstock............................................................................................................................................ Cast Iron
Tailstock............................................................................................................................................... Cast Iron
Paint Type/Finish.................................................................................................................................... Enamel
Other Related Information
Bed Width............................................................................................................................................ 8-5/16 in.
Faceplate Size....................................................................................................................................... 3-1/4 in.
Other Specifications:
Country of Origin ................................................................................................................................................ China
Warranty ........................................................................................................................................................... 1 Year
Approximate Assembly & Setup Time .............................................................................................................. 1 Hour
Serial Number Location .................................................................................................................................. ID Label
ISO 9001 Factory .................................................................................................................................................. Yes
Certified by a Nationally Recognized Testing Laboratory (NRTL) ......................................................................... Yes
Features:
Electronic Variable-Speed Spindle Control with Digital RPM Readout
Forward/Reverse Switch
15" Maximum Distance from Tool Rest to Spindle Centerline
Low Spindle Speed Range of 60-1200 RPM and High Spindle Speed Range of 120-2300 RPM
Capability to Position Headstock Anywhere Along the Bed
7.5 Degree Spindle Indexing
Tailstock, Headstock, and Tool Rest Support have Lever-Action Cam-Locks for Quick Positioning
Adjustable Leveling Feet
4-1/2" Tailstock Quill Travel
Built-In Tool Holder
Содержание G0835
Страница 34: ...Model G0799 G0800 Mfd Since 11 17 17 5mm Hardware Recognition Chart ...
Страница 79: ......