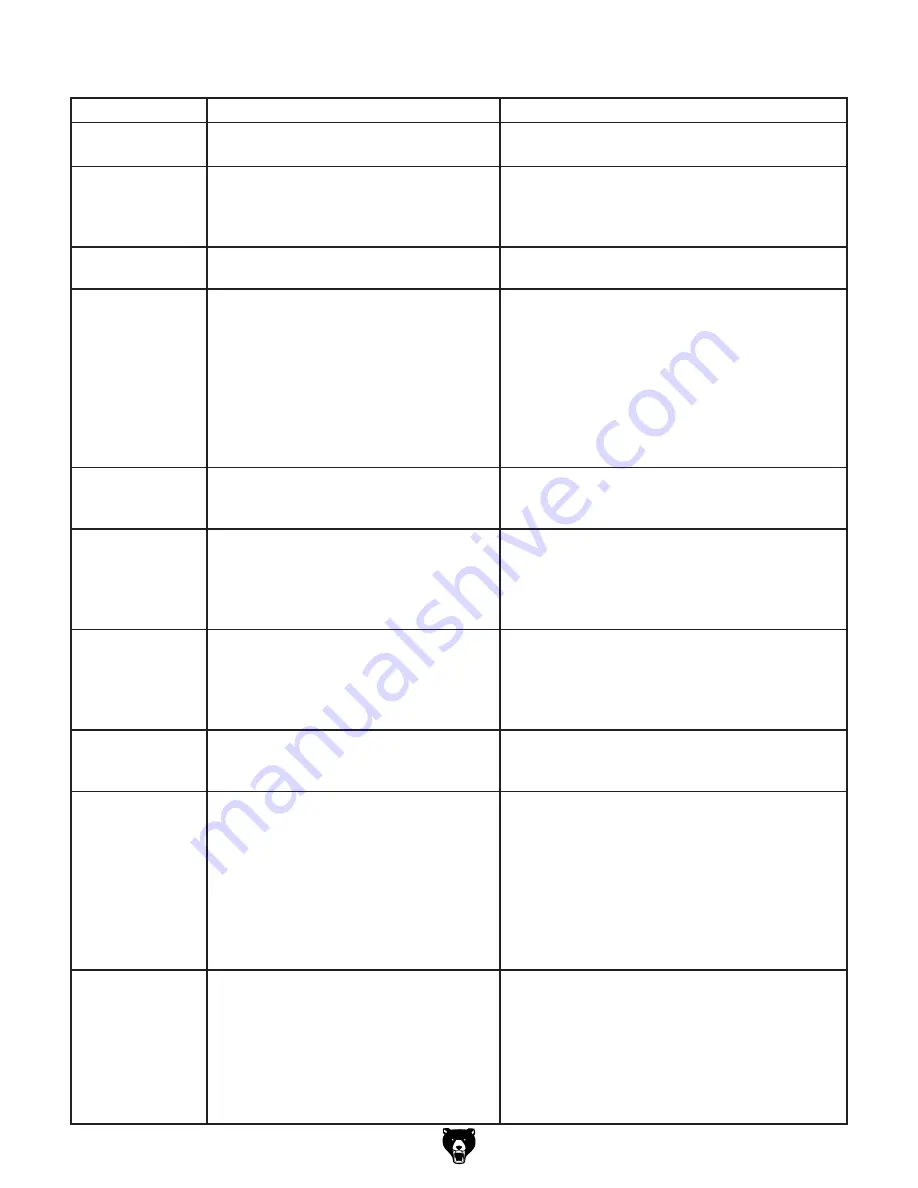
Model G0821 (Mfd. Since 03/18)
-37-
Symptom
Possible Cause
Possible Solution
Infeed table is hard
to adjust.
1. Sawdust, wood chips, or pitch/resin built up
on table leadscrew or moving parts.
1. Clean and lubricate infeed table leadscrew (
Page
32).
Excessive snipe
(gouge in end of
board that is uneven
with rest of cut).
1. Outfeed table is out of alignment with
cutterhead.
2. Operator is pushing down on trailing edge
of the workpiece.
1. Align cutterhead with outfeed table.
2. Reduce/eliminate downward pressure on that end of
the workpiece.
Workpiece stops in
middle of cut.
1. Outfeed table is set lower than cutterhead.
1. Align cutterhead inserts with outfeed table at top
dead center.
Workpiece chipping,
tear-out, indenta-
tions, or overall
rough cuts.
1. Not feeding workpiece to cut "with" the
grain.
2. Dull inserts.
3. Workpiece not okay for jointing.
4. Nicked or chipped inserts.
5. Feeding workpiece too fast.
6. Excessive depth of cut.
7. Lack of proper dust collection or clogged
dust port.
1. Rotate workpiece 180° before feeding again.
2. Rotate/replace insert(s) (
Page 35).
3. Ensure workpiece is okay for jointing (
Page 22).
4. Rotate/replace insert(s) (
Page 35).
5. Reduce feed rate.
6. Reduce depth of cut.
7. Clear blockages, ensure dust collection is operating
efficiently; upgrade dust collector.
Fuzzy grain left in
workpiece.
1. Wood has high moisture content.
2. Dull inserts.
1. Ensure wood moisture content is less than 20%.
Allow to dry if necessary.
2. Replace/rotate inserts (
Page 35).
Long lines or ridges
that run along the
length of the board.
1. Nicked or chipped inserts.
2. Loose or incorrectly installed insert(s).
3. Dirt or debris under carbide inserts.
1. Replace/rotate inserts (
Page 35).
2. Remove/replace insert(s) and install properly (
Page
35).
3. Remove inserts, properly clean mounting pockets
and re-install.
Uneven cutter
marks, wavy
surface, or chatter
marks across face
of workpiece.
1. Feeding workpiece too fast.
2. Inserts not adjusted at even heights in the
cutterhead.
3. Dirt or debris under carbide inserts.
1. Reduce feed rate.
2. Remove, clean, and re-install any inserts that are
"raised" in the cutterhead (
Page 35).
3. Remove inserts, properly clean mounting pockets,
and re-install.
Glossy surface;
scorching or burn
marks on workpiece.
1. Dull inserts.
2. Feed rate too slow.
1. Rotate/replace insert(s) (
Page 35).
2. Increase feed rate.
Workpiece is
concave or convex
along its length after
jointing.
1. Board not held with even pressure on
infeed and outfeed table during cut.
2. Board started too uneven.
3. Board has excessive bow or twist along its
length.
4. Insufficient number of passes.
1. Hold board with even pressure as it moves over the
cutterhead.
2. Take partial cuts to remove extreme high spots
before doing a full pass.
3. Surface plane one face so there is a good surface to
position against the fence.
4. It may take extra passes to achieve a correct edge,
depending on starting condition of board and depth
of cut.
Overall, cut quality
is poor; inconsistent
snipe problems; or
consistent difficulty
feeding workpiece.
1. Debris under inserts.
2. Outfeed table height is not even with
cutterhead.
3. Fence stops are set incorrectly.
4. Fence bracket parts are loose or parts are
misaligned.
1. Remove inserts, properly clean mounting pockets,
and re-install.
2. Reset inserts to correct height and alignment with
cutterhead assembly.
3. Recalibrate fence stops (
Page 36).
4. Check/tighten fence bracket fasteners.
Operations
Содержание G0821
Страница 52: ......