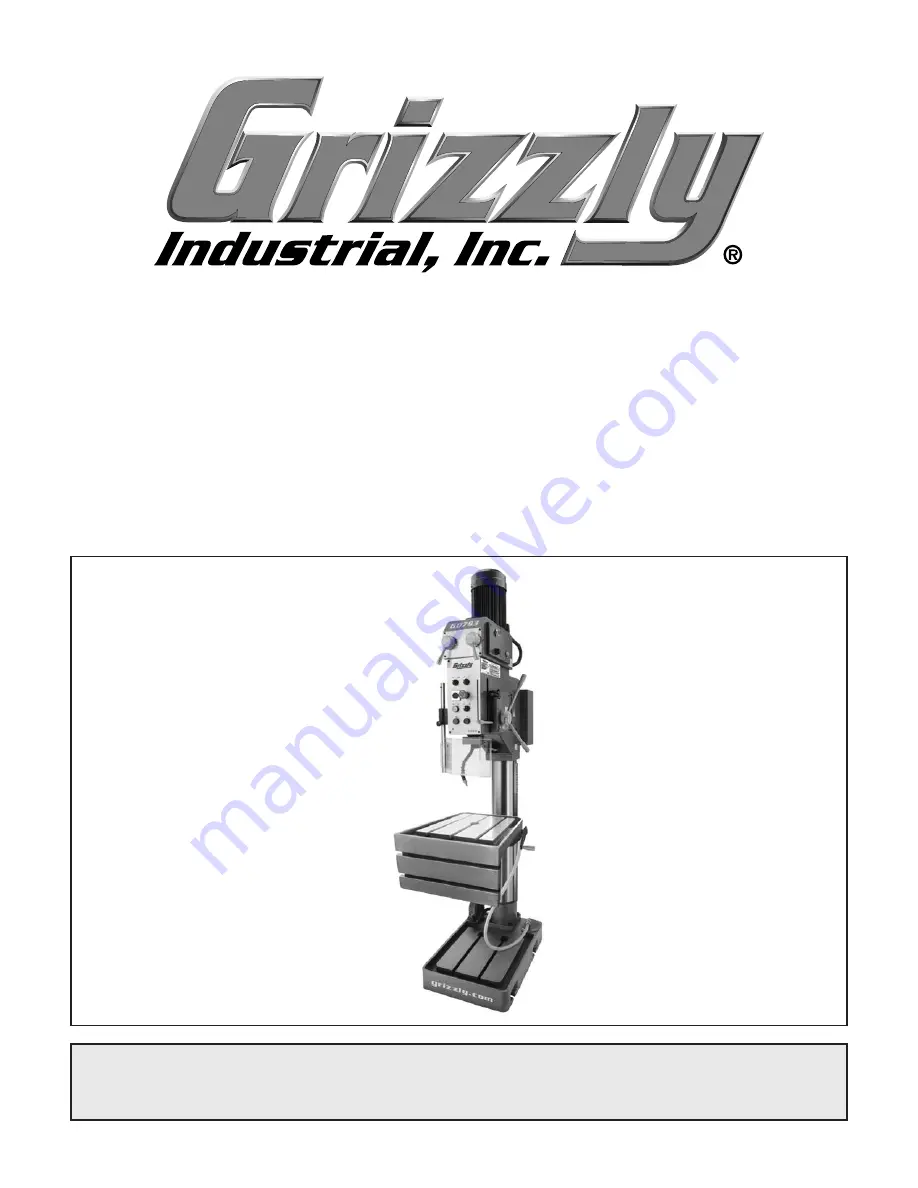
MODEL G0793
HEAVY-DUTY DRILL PRESS
w/AUTO-FEED & L-TABLE
OWNER'S MANUAL
(For models manufactured since 02/15)
COPYRIGHT © MAY, 2015 BY GRIZZLY INDUSTRIAL, INC. REVISED FEBRUARY, 2019 (MN)
WARNING: NO PORTION OF THIS MANUAL MAY BE REPRODUCED IN ANY SHAPE
OR FORM WITHOUT THE WRITTEN APPROVAL OF GRIZZLY INDUSTRIAL, INC.
#BB17384 PRINTED IN CHINA
V1.02.19
Содержание G0793
Страница 60: ......