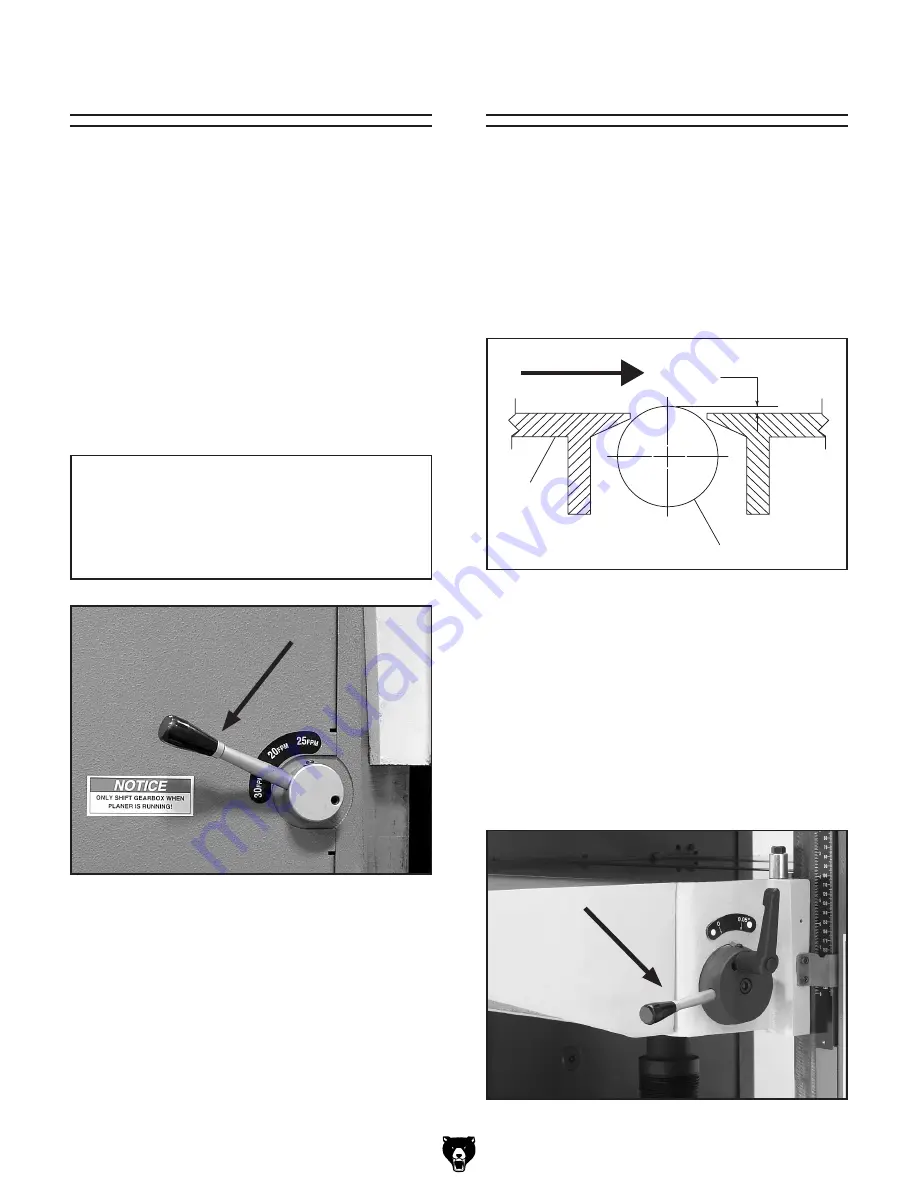
-28-
G0603X 25" Extreme Series Planer
Power Feed Rate
The infeed and outfeed rollers power the stock
through the planer while keeping boards flat and
providing a consistent rate of movement.
The Model G0603X power feed features three
feed rates—20, 25, and 30 FPM. Use the different
feed rates as recommended below:
20 or 25 FPM ....................... Dimensioning Pass
25 or 30 FPM ...............................Finishing Pass
The feed rate control on the left side of the table
(see
Figure 20
) is used to adjust the speed of
the infeed and outfeed rollers. The speed should
ONLY be changed when the machine is running
.
NOTICE
ONLY change the speeds when the planer
is running, but DO NOT attempt to change
speeds during a cutting operation or dam-
age to the gearbox will result.
Figure 20.
Feed rate control.
Table Rollers
Adjustment Height Range .........0.002"–0.050"
The height of the table rollers will vary, depending
on the condition of the wood you intend to plane.
When planing rough cut stock, set the rollers high
to keep the lumber from dragging along the bed.
When planing milled lumber, set the rollers low to
help minimize snipe (gouging at the ends of the
workpiece).
���������������
�����
������������
����������������
Figure 21.
Table roller height range.
To adjust the table rollers:
1.
Rotate the locking handle counterclockwise
to loosen the table roller lever (see
Figure
22
).
2.
Move the table roller lever to the desired
height on the scale.
3.
Retighten the locking handle.
Figure 22.
Table roller height control.
Содержание G0603X
Страница 2: ... ...
Страница 5: ...G0603X 25 Extreme Series Planer 3 Machine Data Sheet ...
Страница 6: ... 4 G0603X 25 Extreme Series Planer ...
Страница 10: ... 8 G0603X 25 Extreme Series Planer ...
Страница 11: ...G0603X 25 Extreme Series Planer 9 Safety Instructions for Machinery ...
Страница 50: ... 48 G0603X 25 Extreme Series Planer Page 47 Page 47 Page 47 Page 47 Page 50 Page 50 Page 49 Page 51 Page 51 ...
Страница 51: ...G0603X 25 Extreme Series Planer 49 Page 47 Page 51 Page 51 Page 50 Page 50 Page 50 Page 48 ...
Страница 52: ... 50 G0603X 25 Extreme Series Planer Page 49 Page 48 Page 49 ...
Страница 53: ...G0603X 25 Extreme Series Planer 51 Page 49 ...
Страница 54: ... 52 G0603X 25 Extreme Series Planer Base Parts Breakdown ...
Страница 57: ...G0603X 25 Extreme Series Planer 55 Column Parts Breakdown ...
Страница 59: ...G0603X 25 Extreme Series Planer 57 Electric Parts Breakdown ...
Страница 61: ...G0603X 25 Extreme Series Planer 59 Gearbox Parts Breakdown ...
Страница 63: ...G0603X 25 Extreme Series Planer 61 Headstock Parts Breakdown ...
Страница 65: ...G0603X 25 Extreme Series Planer 63 Table Parts Breakdown ...
Страница 68: ......
Страница 69: ... ...
Страница 70: ... ...
Страница 72: ... ...