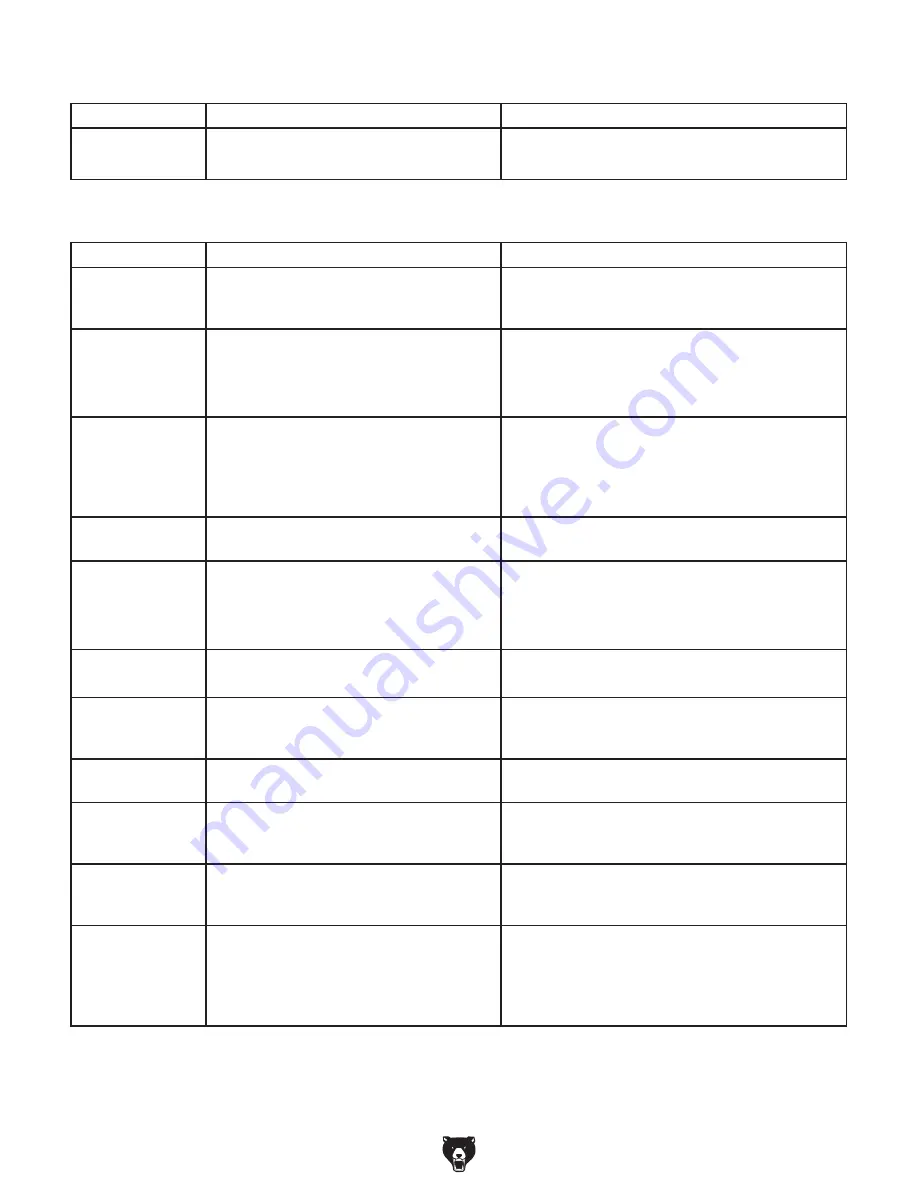
-34-
Model G0449/G0450 (Mfd. Since 8/13)
Motor & Electrical Continued
Symptom
Possible Cause
Possible Solution
Machine stalls or is
overloaded.
10. Motor is at fault.
11. Air circulation through the motor restricted.
10. Test/repair/replace.
11. Clean off motor to provide normal air circulation.
Machine Operations
Symptom
Possible Cause
Possible Solution
Drums run
backwards (G0450
only).
1. Two of the power wires are reversed
(G0450 only).
1. Switch two of the current carrying wires at the main
power block (G0450 only). (Page 20)
Machine slows
when sanding,
making squealing
noise, especially on
start-up.
1. V-belts loose.
2. V-belts worn out.
1. Tighten V-belts (Page 36).
2. Replace V-belts (Page 37).
Loud repetitious
noise coming from
machine.
1. Pulley setscrews or keys are missing or
loose.
2. Motor fan is hitting the cover.
3. V-belts are defective.
1. Inspect keys and setscrews. Replace or tighten if
necessary.
2. Adjust fan cover mounting position, tighten fan, or
shim fan cover.
3. Replace V-belts (Page 37).
Vibration when
sanding.
1. Loose drum pillow bearings.
2. Worn drum pillow bearings.
1. Tighten drum pillow bearings.
2. Replace drum pillow bearings.
Grinding,
screeching, or
rubbing noise when
sanding drums are
powered up.
1. Drum bearings lack sufficient grease.
2. Drum bearings worn.
1. Grease the pillow bearings (Page 31).
2. Replace the drum bearings.
Short V-belt
lifespan.
1. Pulleys not aligned correctly.
2. Improperly tensioned.
1. Align pulleys (Page 37).
2. Properly tension V-belts (Page 36).
Machine lacks
power; drums stop
turning under load.
1. V-belts loose.
2. Too much pressure on pressure rollers.
1. Tighten V-belts (Page 36).
2. Reduce pressure roller pressure (Page 46).
Conveyor slips
under load.
1. Conveyor is too loose.
2. Too much load.
1. Tension conveyor (Page 40).
2. Decrease load.
Conveyor tracks to
one side; conveyor
hits the roller cover.
1. Conveyor tracking is incorrect.
1. Track the conveyor so it runs straight (Page 41).
Workpiece pulls
to one side during
sanding operations.
1. One of the sanding drums is not parallel
with the table.
1. Adjust the sanding drums parallel to the table (Page
41
).
Excessive snipe.
1. Too much pressure roller pressure.
2. Too much pressure from rear pressure
rollers.
3. Lack of outfeed support.
1. Reduce pressure roller pressure (Page 46).
2. Reduce rear pressure roller pressure (Page 46).
3. Set up outfeed table or have someone catch the
workpiece as it comes out.
Содержание G0449
Страница 80: ......