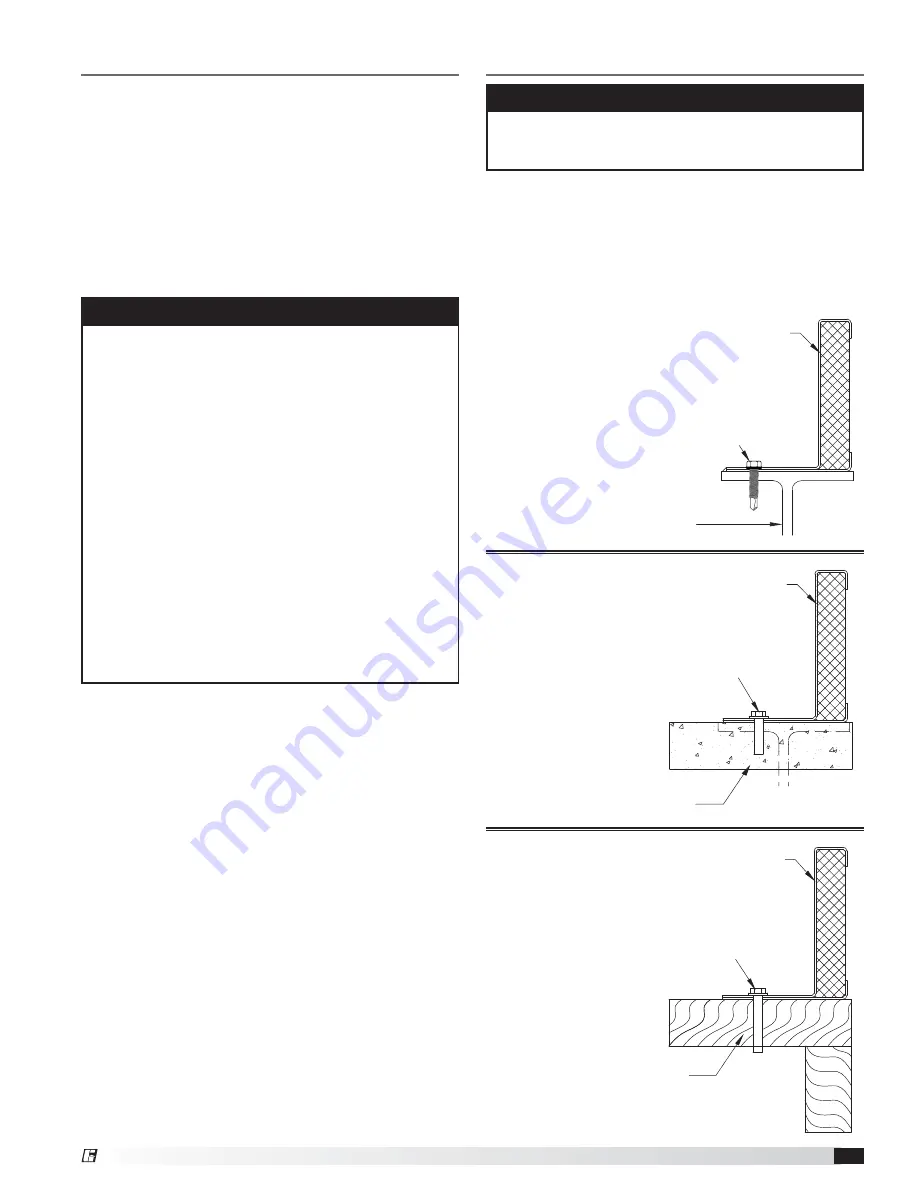
FumeJet
®
Fume Exhaust Fans
7
®
Move the fan to the desired location. Check and tighten
fasteners throughout the unit and then fasten securely
through mounting holes provided in the base angles.
The unit must be set level (shimming may be necessary).
Flexible duct connections and vibration isolators should
be used where noise is a factor.
The motor voltage and ampere rating must be checked
for compatibility with the electrical supply prior to final
electrical connection. Supply wiring to the fan must
be properly fused, and conform to local and national
electrical codes.
IMPORTANT
When installing a fan, ensure the proper protective
devices are used to protect personnel from moving
parts and other hazards.
Electrical Disconnects
All fan motors should have disconnects located in
close visual proximity to turn off electrical service.
Service disconnects shall be locked out when
maintenance is being performed.
Moving Parts
All moving parts must have guards to protect
personnel. Refer to local codes for requirements as to
the number, type and design. Fully secure fan wheel
before performing any maintenance. The fan wheel
may start “free wheeling” even if all electrical power
has been disconnected. Before the initial start-up
or any restart, check the guards (motor cover and
weatherhood) and check the access doors to ensure
that they are installed and secure.
Installation
Roof Curb and Mounting Details
Required with curb cap inlet box or mega stack.
The
figures below illustrate three common methods used
to install roof curbs for FumeJet
®
systems. Methods
used to attach a unit are dependent on local codes, roof
construction design and roof construction materials.
Consult an architect or structural engineer for proper
means of attachment.
NOTE
Steel, concrete or wood roof support is per structural
engineer and in accordance with load requirements
and applicable building codes.
Steel
STEEL STRUCTURAL SUPPORT
(BY OTHERS, SEE NOTE ABOVE)
Continuous weld or stitch weld.
Minimum 6 inch
(152.4 mm)
stitch weld by
3.25 inch
(82.5 mm)
spacing minimum.
Minimum 6 inch
(152.4 mm)
weld on each corner.
OR
Install 5/16 inch
(7.9375 mm)
24 Dril-Flex® Self-Drilling
Tapping Screws. 3/16 inch
(4.7625 mm)
minimum thread
engagement into A36 steel, centered in flange.
4.5 inch
(114.3 mm)
spacing
5/8 inch
(15.875 mm)
minimum edge distance
ALL HARDWARE BY OTHERS
Greenheck Roof Curb GPFHL
Concrete
CONCRETE STRUCTURAL SUPPORT
(BY OTHERS, SEE NOTE ABOVE)
Install 3/8 inch
(9.525 mm)
SS power wedge bolts
2.5 inch
(63.5 mm)
maximum spacing from curb corners
4.5 inch
(114.3 mm)
maximum bolt spacing
3.5 inch
(88.9 mm)
minimum embedment
4.5 inch
(114.3 mm)
minimum edge
distance centered in flange
ALL HARDWARE BY OTHERS
Greenheck Roof Curb GPFHL
Wood
WOODEN STRUCTURAL SUPPORT
(BY OTHERS, SEE NOTE ABOVE)
Greenheck Roof Curb GPFHL
Install 3/8 inch
(9.525 mm)
SS lag or thru-bolt with
1 inch
(25.4 mm)
O.D. washer
2.5 inch
(63.5 mm)
maximum spacing from curb corners
4.5 inch
(114.3 mm)
maximum bolt spacing
3.5 inch
(88.9 mm)
minimum tread engagement,
not including tapered tip
2 inch
(50.8 mm)
minimum edge distance,
centered in flange
Pre-drill holes 40-60% of lag diameter
ALL HARDWARE BY OTHERS