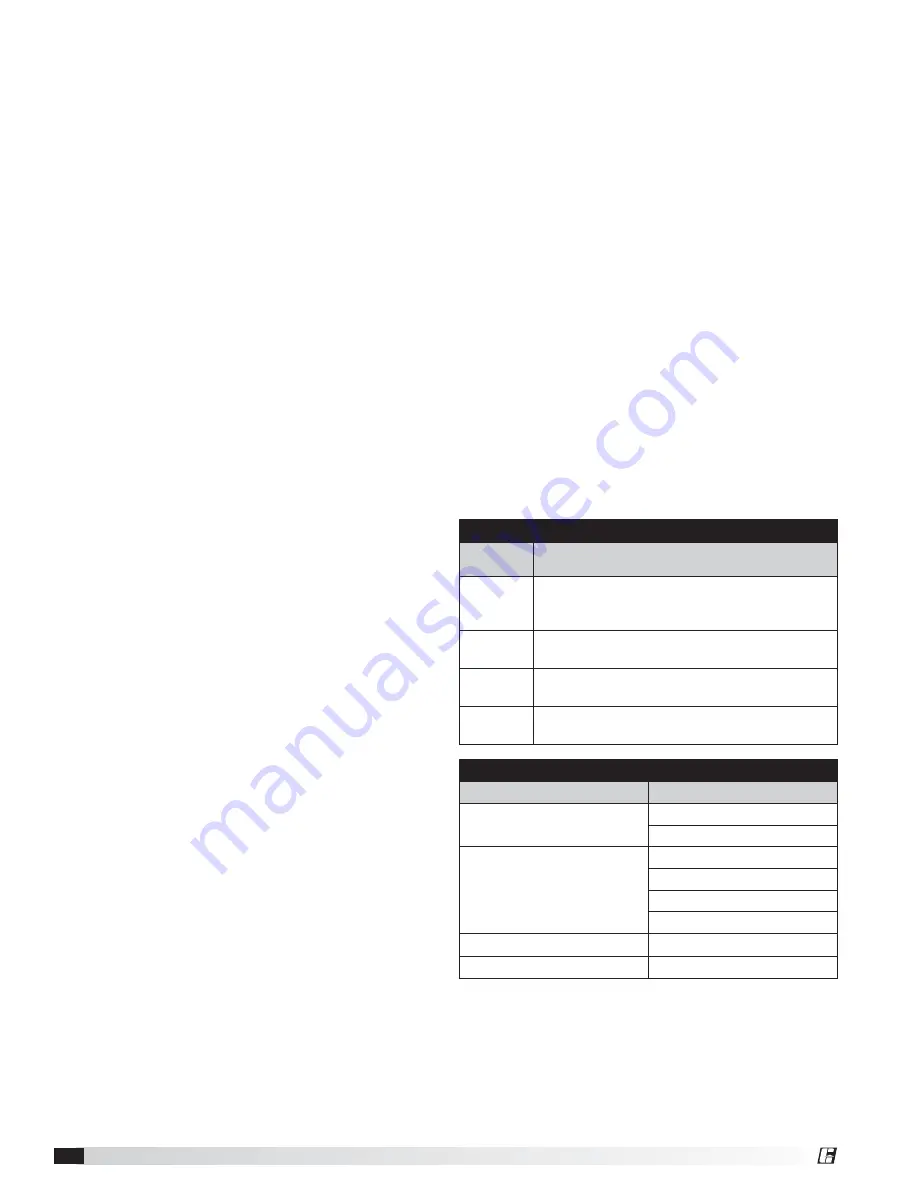
Centrifugal Inline Fans
10
®
Grease Manufacturers
Manufacturer
Grease (NLGI #2)
Chevron U.S.A. Inc
Chevron SRI Grease 2
Chevron Multifak EP 2
Exxon Mobil
Mobilux EP 2
Mobilith SHC 220
Mobilith AW-2
Unirex N2
BP Amoco
Rykon Premium #2 EP
Shell
Shell Gadus S2 V220 2
Suggested Fan Bearing Greasing Intervals
Interval
(months)
Type of Service
1 to 3
Heavy duty in dirty, dusty locations; high
ambient temperatures; moisture laden
atmosphere; vibration.
3 to 6
12 to 24 hours per day, heavy duty, or if
moisture is present
6 to 12
8 to 16 hours per day in clean, relatively dry
atmosphere
12 to 18
Infrequent operation or light duty in clean
atmosphere
5. Shaft bearings can be classified in two groups:
relubricating and non-relubricating. All bearings
on standard belt drive fans are factory lubricated
and require no further lubrication under normal use
(between -20ºF and 180ºF
(-29
º
C and 82ºC)
in a
relatively clean environment).
6. Units installed in hot, humid or dirty locations should
be equipped with special bearings. These bearings
will require frequent lubrication. Caution should be
employed to prevent overpacking or contamination.
7. Grease fittings should be wiped clean. The unit
should be in operation while lubricating. Extreme
care should be used around moving parts.
8. Grease should be pumped in very slowly until a slight
bead forms around the seal. A high grade lithium
base grease should be used.
Recommended Relubrication Frequency
in Months
NOTE: If unusual environment conditions exist (extreme
temperature, moisture or contaminants) more frequent
lubrication is required.
A good quality lithium base grease, conforming to
NLGI Grade 2 consistency, such as those listed here
may be used with fan bearings.
3.
Standard Mounting:
Take the two socket head cap
screws that were removed and install them into the
visibly threaded holes on the wheel hub.
Reverse Mounting:
Install the two socket head cap
screws into the visibly threaded holes of the bushing
flange.
4. Once both socket head cap screws are installed,
tighten them an eighth of a turn at a time, alternating
between the two until the hub comes loose from the
bushing.
Bushing Installation
1. Clean all surfaces of hub and bushing to remove any
oil or residue present and do not use any lubricant to
install bushing into the hub. For both standard and
reverse mounting styles, the socket head cap screws
are adjustable from the inlet of the fan.
2.
Standard Mounting:
Slide the bushing and shaft
key onto the fan shaft followed by the wheel and hub
assembly. If present, use the keyway setscrew to
hold the shaft key and bushing in place but DO NOT
overtighten as this can damage the bushing. Align
the unthreaded holes of the hub with the threaded
holes of the tapered bushing.
Reverse Mounting:
Slide the wheel and hub
assembly onto the fans shaft followed by the bushing
and shaft key. If present, use the keyway setscrew to
hold the shaft key and bushing in place but DO NOT
overtighten as this can damage the bushing. Align
the unthreaded holes of the tapered bushing with the
threaded holes of the hub.
3. Install the two bushing socket head cap screws
into the aligned holes by hand (or without excessive
torque) until the heads of the socket head cap
screws are seated against the mating surface.
4. Adjust the height of the wheel in the fan relative to
the inlet venturi then tighten the two socket head
cap screws an eighth turn at a time in an alternating
fashion and to a torque of 10 ft-lbs.
Belt/Bearing Maintenance - Belt Drive
1. Belts tend to stretch after a period of time. They
should be checked periodically for wear and
tightness. When replacing belts, use the same type
as supplied with the unit.
2. Matched belts should always be used on units with
multi-groove pulleys.
3. For belt replacement, loosen the tensioning device
enough to allow removal of the belt by hand. Do not
force belts on or off. This may cause cords to break,
leading to premature belt failure.
4. Once installed, adjust belts as shown in
Pre-Start-Up Checks.