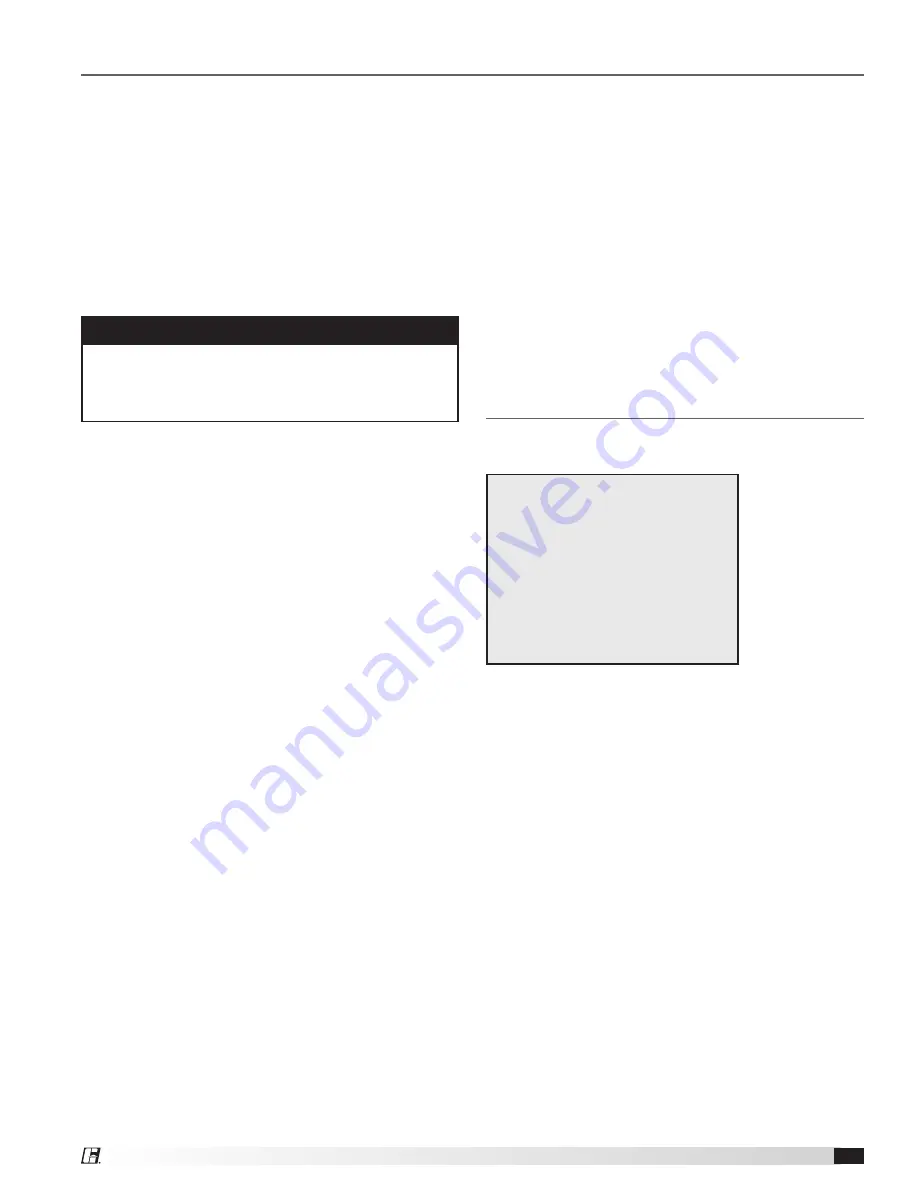
Centrifugal, Industrial and Filtered Supply
9
Visual Inspection of Equipment
The equipment type and arrangement should be verified
as ordered at once when it arrives at the job site. When
a discrepancy is found, the local sales representative
must be notified immediately so that corrective action
may be investigated, also verify electrical conformance
to specifications. Unauthorized alterations and
unauthorized back charges will not be recognized by the
manufacturer.
After the unit has been assembled, installed and all
utilities have been hooked up, the unit is now ready for
operation.
Before starting the unit, check the following:
1. Disconnect and lock-out all power switches to fan.
See warning below.
2. Check all fasteners, set screws and locking collars
on the fan, bearings, drive, motor base and
accessories for tightness.
3. Rotate the fan wheel manually to be sure that it is
free to operate. Remove any dirt or debris that may
have accumulated during installation.
4. Check for bearing alignment and lubrication.
5. Check for coupling alignment (Arr. 8 only).
6. Check the V-belt drive for proper alignment and
tension.
7. Check all guarding (if supplied) to ensure that it is
securely attached and not interfering with rotating
parts.
8. Check operation of variable inlet vanes or discharge
dampers (if supplied) for freedom of movement.
9. Check all electrical connections for proper
attachment.
10. Check housing and ductwork, if accessible, for
obstructions and foreign material that may damage
the fan wheel.
Additional Steps for Initial Start-Up
1. Check for proper wheel rotation by momentarily
energizing the fan. Rotation is always determined
by viewing the wheel from the drive side and should
correspond to the rotation decal affixed to the unit.
One of the most frequently encountered problems
with centrifugal fans is motors which are wired to run
in the wrong direction. This is especially true with
3-phase installations where the motor will run in
either direction, depending on how it has been wired.
To reverse rotation of a 3-phase motor, interchange
any two of the three electrical leads. Single phase
Vibration
Excessive vibration is the most frequent problem
experienced during initial start-up. Left unchecked,
excessive
vibration
can cause a
multitude of
problems,
including
structural and/
or component
failure.
Many of these
conditions can
be discovered
by careful observation. Refer to the troubleshooting
section of this manual for corrective actions. If
observation cannot locate the source of vibration, a
qualified technician using vibration analysis equipment
should be consulted. If the problem is wheel unbalance,
in-place balancing can be done providing there is
access to the fan wheel. Any correction weights added
to the wheel should be welded to either the wheel back
(single-plane balance) or to the wheel back and wheel
cone (two-plane balance).
Greenheck performs a vibration test on all centrifugal
fans before shipping. Three vibration readings are taken
on each bearing in the horizontal, vertical, and axial
directions. The allowable maximum vibration for belt
drive units is 0.15 in/sec. peak velocity filter-in for rigid
mount and 0.20 in/sec. peak velocity filter-in for flexible
mount at the fan RPM per AMCA Standard 204. These
vibration signatures are a permanent record of how the
fan left the factory and are available upon request.
Generally, fan vibration and noise is transmitted to other
parts of the building by the ductwork. To eliminate this
undesirable effect, the use of heavy canvas connectors
is recommended. If fireproof material is required,
Flexweave™1000 - Type FN-30 can be used.
Common Sources of Vibration
1. Wheel unbalance
2. Drive pulley misalignment
3. Incorrect belt tension
4. Bearing / coupling misalignment
5. Mechanical looseness
6. Faulty belts
7. Drive component unbalance
8. Poor inlet / outlet conditions
9. Foundation stiffness
WARNING
Disconnect and secure to the “Off” position all
electrical power to the fan prior to inspection or
servicing. Failure to comply with this safety precaution
could result in serious injury or death.
motors can be reversed by changing internal
connections as described on the motor label or
wiring diagram.
2. If the fan has inlet vanes, they should be partially
closed to reduce power requirements. This is
especially important if the fan is designed for a high
temperature application and is being started at room
temperature.
3. Fans with multi-speed motors should be checked on
low speed during initial start-up.
4. Check for unusual noise, vibration or overheating of
bearings. Refer to the “Troubleshooting” section of
this manual if a problem develops.
5. Grease may be forced out of the bearing seals during
initial start-up. This is a normal self-purging feature
of this type of bearing.
Unit Start-Up