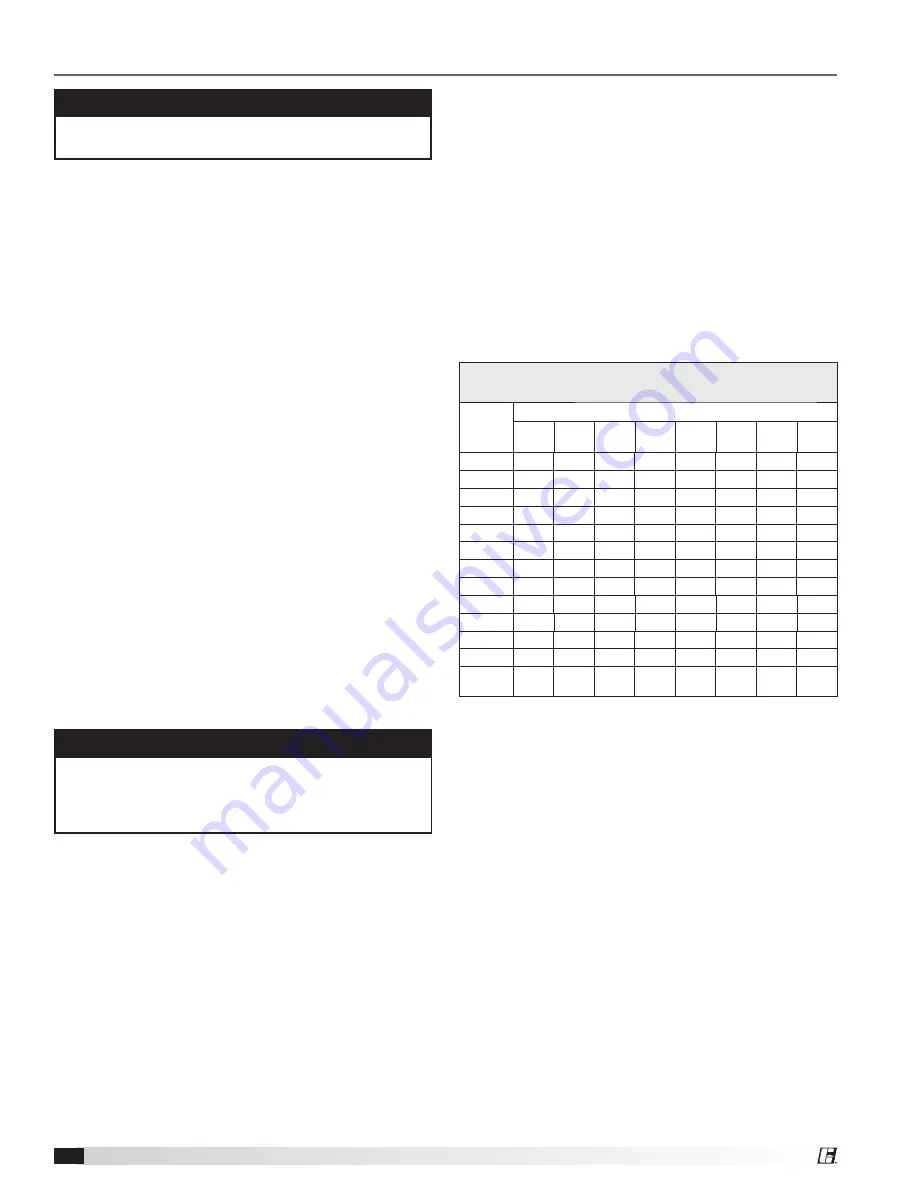
Centrifugal, Industrial and Filtered Supply
10
Once the unit has been put into operation, a routine
maintenance schedule should be set up to accomplish
the following:
1. Lubrication of bearings and motor (see below).
2. Wheel, housing, bolts and set screws on the entire
fan should be checked for tightness.
3. Any dirt accumulation on the wheel or in the housing
should be removed to prevent unbalance and
possible damage.
4. Isolation bases should be checked for freedom
of movement and the bolts for tightness. Springs
should be checked for breaks and fatigue. Rubber
isolators should be checked for deterioration.
5. Inspect fan impeller and housing looking for fatigue,
corrosion or wear.
When performing any service to the fan, disconnect the
electrical supply and secure fan impeller.
Motors
Motor maintenance is generally limited to cleaning
and lubrication. Cleaning should be limited to exterior
surfaces only. Removing dust and grease build up on
the motor housing assists proper motor cooling. Never
wash-down motor with high pressure spray.
Greasing of motors is only intended when fittings are
provided. Many fractional motors are permanently
lubricated for life and require no further lubrication.
Motors supplied with grease fittings should be
greased in accordance with the manufacturer’s
recommendations.
CAUTION
When operating conditions of the fan are to be
changed (speed, pressure, temperature, etc.), consult
Greenheck to determine if the unit can operate safely
at the new conditions.
Shaft Bearings
The bearings for Greenheck fans are carefully selected
to match the maximum load and operating conditions
of the specific class, arrangement, and fan size. The
instructions provided in this manual and those provided
by the bearing manufacturer will minimize any bearing
problems. Bearings are the most critical moving part
of the fan, therefore special care is required when
mounting them on the unit and maintaining them.
Refer to the following chart and the manufacturers
instructions for grease types and intervals for various
operating conditions. Never mix greases made with
different bases. This will cause a breakdown of the
grease and possible failure of the bearing.
Recommended Bearing Lubrication Schedule
Relubrication Schedule in Months*
Fan
RPM
Bearing Bore (inches)
1
⁄
2
-
1
1
1
⁄
8
-
1
1
⁄
2
1
5
⁄
8
-
1
7
⁄
8
1
15
⁄
16
-
2
3
⁄
16
2
7
⁄
16
- 3
3
3
⁄
16
-
3
1
⁄
2
3
15
⁄
16
-
4
1
⁄
2
4
15
⁄
16
-
5
1
⁄
2
To 250
12
12
12
12
12
12
10
8
500
12
12
11
10
8
7
5
4
750
12
9
8
7
6
4
3
2
1000
12
7
6
5
4
3
2
1
1250
12
6
5
4
3
2
1
.5
1500
12
5
4
3
2
1
.75
2000
12
3
3
2
1
.5
.25
2500
12
2
2
1
.5
.25
3000
12
2
1
.5
.25
3500
12
1
.5
.25
4000
12
.5
.25
5000
12
.25
Number
of shots**
4
8
8
10
16
25
41
57
* Lubrication interval is based on 12 hour day operation and
maximum 160˚F housing temperature. For 24 hour per day
operation, the interval should be cut in half.
** Lubricant should be added with the shaft rotating and
until clean grease is seen purging from the bearing. The
lubrication interval may be modified based on the condition
of the purged grease. If bearing is not visible to observe
purged grease, lubricate with number of shots indicated for
bore size.
• For conditions including high temperatures, moisture, dirt
or excessive vibration, consult the factory for a specific
lubrication interval for your application.
• Lubricant should be a high quality lithium complex grease
conforming to NLGI Grade 2. Factory recommends Mobilux
EP-2 or synthetic Mobilith SHC100.
• The use of synthetic lubricants will increase lubrication
intervals by approximately three times.
• Storage periods of three months or longer require monthly
rotation of the shaft and purging grease prior to storage and
start-up.
Routine Maintenance
WARNING
Before taking any corrective action, make certain unit
is not capable of operation during repairs.