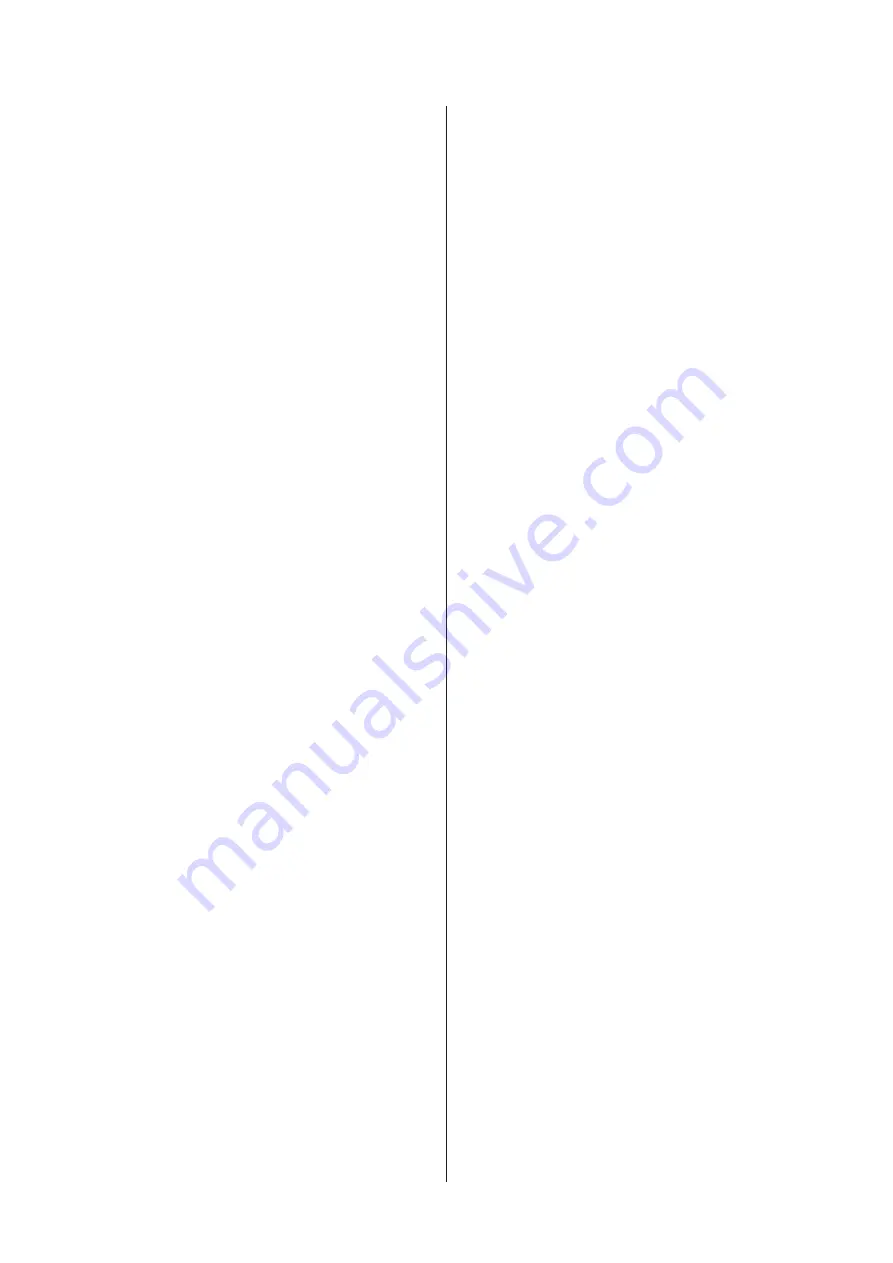
3
IMPORTANT:
CONNECTING THE MACHINE TO THE EARTHING SYSTEM
IS MANDATORY.
To this purpose, the terminal block is fitted with a specific contact,
which must be connected according to the regulations in force. The
manufacturer disclaims all responsibility for damage resulting
from non-observance of this accident prevention principle.
In compliance with the latest accident prevention provisions, the
machine is provided with an external terminal for equipotential
connection.
At the beginning of the power supply line there must be an
automatic all-pole circuit breaker with settings meeting the
maximum rated input (cfr. rating plate details of the equipment).
Provide for a 20 mm cable carrier duct (outer diameter) between the
circuit breaker and the power supply inlet to the equipment. Use the
cable clamp existing at the back of the machine to introduce the
power cord and, once the cables have been connected to the terminal
board following the sequence shown on the same, stop the cable by
the plastic nut.
Caution!
These appliances are equipped with electronic control devices like
a control card and an inverter. To be CE type-approved, such
devices must include noise filters complying with EMC standards
on eddy current emission. To operate properly, these filters leak a
small current of approximately 10-15mA through the earth lead.
Therefore every machine must be fitted with its own system-
protecting residual current cutoff switch (RCD). Avoid connecting
more than one appliance, whatever their capacity or brand,
downstream of a single RCD.
THE WARRANTY DOES NOT COVER DAMAGE CAUSED
BY INCORRECT INSTALLATION.
3. REQUIREMENTS FOR INSTALLATION
3.1 SPACE REQUIRED FOR INSTALLATION, USE AND
MAINTENANCE
The equipment requires the minimum space indicated in dimensional
figures 1 and 1a:
1) power supply line with RCBO (Residual Current Circuit Breaker
with Overcurrent Protection) at the beginning of the line*.
2) Interlocked socket including fuses and manual all-pole switch.
3) Power supply plug.
4) Shutoff taps for water inlets.
5) Grille or plate (preferred) for closing the drain trap.
6) Rubber hose for water drain (included).
7) Drain trap.
8) Circular door.
9) Hard water inlet.
10) Warm water inlet.
11) Soft water inlet.
12) Steam inlet (only for steam-heated models).
13) Cable clamp for the power supply inlet.
14) Template to be used for positioning machine-anchoring bolts.
15) 3 tubes for hard, warm and soft water intakes (included)
16) Flexible steam connection tube (included with steam-heated
models only).
17) 3/4" mechanical filter (provided with steam-heated models
only).
18) Steam supply line, pressure comprised between 4 and 6 bar; as
for consumption rates, cfr. rating plate details.
19) Steam shutoff tap (steam-heated models only).
20) 3/4" condensed water drain (only for indirect-steam models).
* The automatic circuit breaker must be in a position allowing easy
access to the operator in any EMERGENCY event.
4. HANDLING, UNPACKING AND STORING
4.1 SHIPPING AND HANDLING
To handle and/or ship the machine follow carefully the ensuing
recommendations:
Move the machine on its own pallet or on a similar platform; use a
fork lift, either manual or electric, provided it is adequate for
handling such appliances and it has the requisite lifting capacity
(cfr. technical data). Check beforehand that the equipment can
surmount any existing obstacle, like staircases, doors, etc. Do not
drag the machine by the sides or by any other part.
For shipping purposes, use only the original packaging, which
helps ensure sufficient stability during transportation.
4.2 STORING
If the equipment must be stored for a long period of time before
being put into operation, keep it inside the original package, since
this guarantees excellent protection. Also ensure that the
environmental conditions in the storehouse meet those indicated in
the next paragraphs. On the other hand, if the machine must be left
inoperative for a long period after use, be sure it is materially
disconnected from the electric supply and cover it the original
protection bag.
4.3 UNPACKING
1) Prior to accepting the machine from the carrier, check the
conditions of the packaging. If it is showing visible damage, the
machine may have been damaged too. In this case, unpack the
machine in the presence of the carrier and sign, under
reservation, the delivery slip. The manufacturer undertakes no
liability for any damage caused by transportation or improper
storage.
2) Unpack the machine with the utmost care to avoid damage. To
remove the platform, take off the screws from the inside of the
same, which are in the machine floor-fastening holes.
3) For all washing machines: open the door (cfr. next paragraphs)
and check that the following items are in the package:
- # 2 metal straps
- # 1 90° rubber elbow
- # 2 flexible pipes with ¾ ferrule
- # 1* brass strain for the steam inlet (steam-heated model only)
- # 2 flexible metal pipe
- keys to the coin box and 15 coins (only for coin-operated
versions)
- the keys to the machine's hood (only for machines featuring
a key-operated lock).
ON HIGH-SPEED WASHERS THE BRACKETS THAT
FASTEN THE TUB MUST ABSOLUTELY BE REMOVED
BEFORE MACHINE STARTUP.
4) For all ironers in the ranges with diam. 18cm, 25cm and 30cm,
install the linen-rest wood board on the respective supports
using the grub-screws and bolts as in the sticker appearing on
the roller. The head of the screw and the longer side of the board
must face upwards.
5) The packaging material (plastic bags, expanded polystyrene,
wood, cardboard, nails, etc.) represent a safety hazard and
consequently must not be left within the reach of children.
Collect and keep for further transportation or long-term storage.
Before connecting up the appliance, check that the rating plate
details match those of the existing electric line. The appliance
must only ever be used for the purposes it was explicitly
designed for.
6) For tumble dryers: check that the steam electrical valve* is in
the drum.
7) Ensure that the instruction booklet is not left in the package and
lost.
(*Steam-heated machines only).
Before connecting up the appliance, check that the rating plate
details match those of the electric line the equipment is going to be
connected to. The appliance must only ever be used for the purposes
it was explicitly designed for.
4.4 GETTING THE APPLIANCE STARTED
4.4.1 LAYOUT REQUIREMENTS
This equipment offers no positioning difficulty other than a flat,
www.groupdynamics-laundry.com