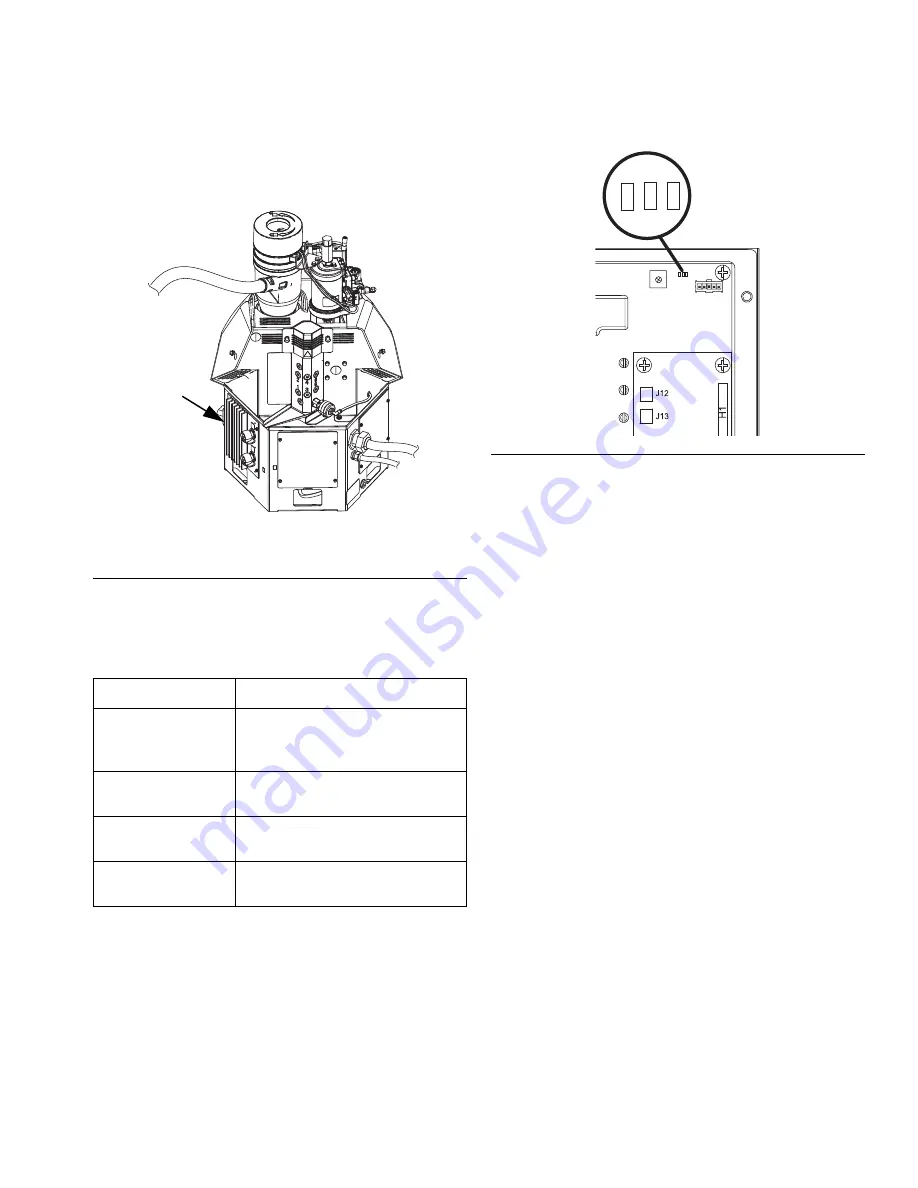
Troubleshooting
333347F
55
MZLP Troubleshooting
NOTE:
The MZLP LED is located on the inside of the
electrical enclosure. To view, remove the electrical
enclosure front access door.
F
IG
. 29: MZLP LED Signals
Signal
Description
Green On
MZLP is powered up and input
voltage is within operating con-
ditions.
Yellow On
Internal communication in pro-
cess
Red Solid
MZLP failure. See troubleshoot-
ing table.
Red Flashing
Software update in process or
missing software.
WLD
MZLP
F
IG
. 30: MZLP Diagnostic LED Location
J3
1
456
7
89 23
0
Green
Y
ellow
Red
ti20348a
Содержание 24T918
Страница 16: ...Component Identification 16 333347F ...
Страница 103: ...Accessories 333347F 103 ...
Страница 129: ...Technical Data 333347F 129 ...