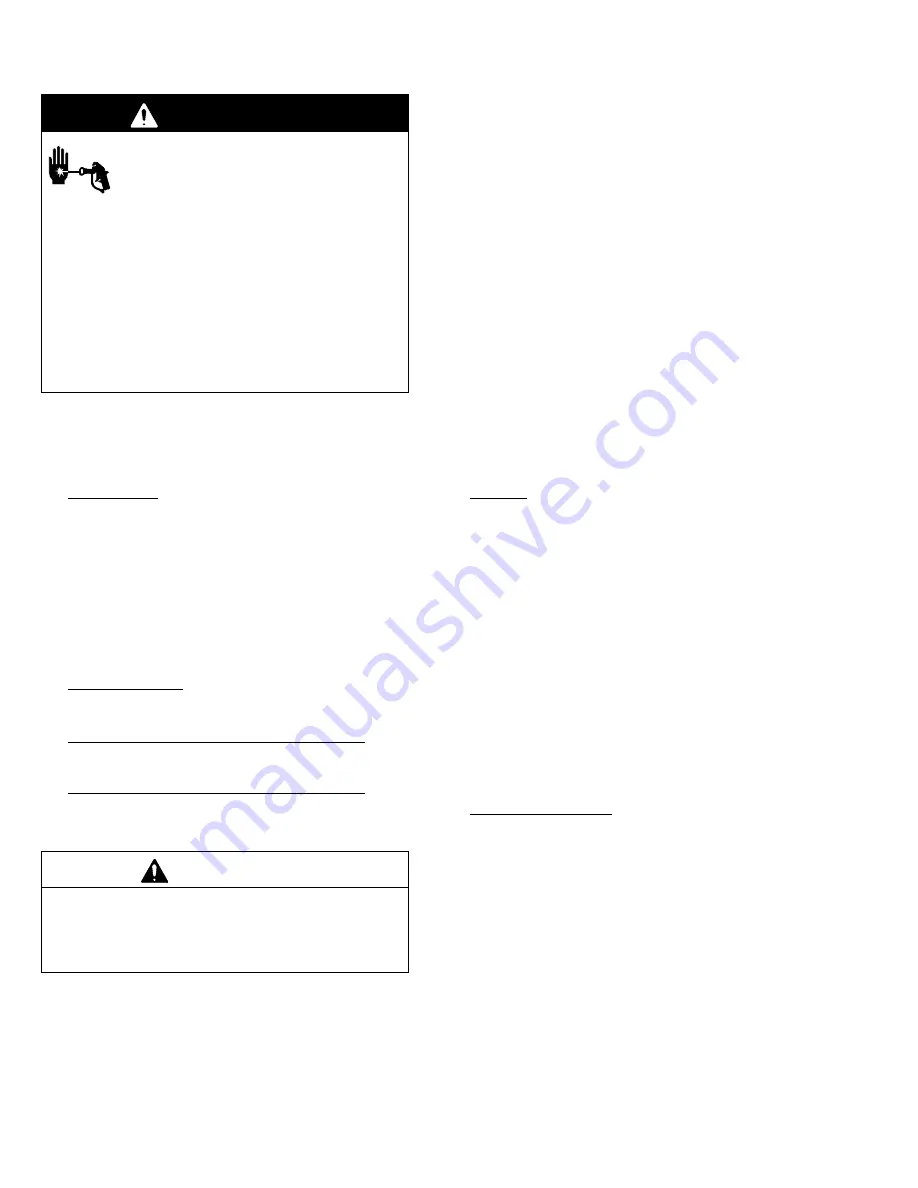
308620
12
Pressure Relief Procedure
WARNING
INJECTION HAZARD
The system pressure must be manually
relieved to prevent the system from
starting or spraying accidentally. Fluid
under high pressure can be injected through the
skin and cause serious injury. To reduce the risk of
an injury from injection, splashing fluid, or moving
parts, follow the
Pressure Relief Procedure
whenever you:
D
are instructed to relieve the pressure,
D
stop spraying,
D
check or service any of the system equipment,
D
install or clean the spray tip.
1. Engage the gun safety latch.
2. Turn the engine switch to OFF.
3. Move the pressure control ON/OFF switch to OFF.
4.
Disengage the gun safety latch. Hold a metal part
of the gun firmly to a grounded metal pail. Trigger
the gun to relieve pressure.
5. Engage the gun safety latch.
6. Open the pressure drain valve. Leave the pressure
drain valve open until you are ready to spray
again.
7. Disconnect the spark plug cable.
If you suspect that the spray tip or hose is completely
clogged, or that pressure has not been fully relieved
after following the steps above,
VERY SLOWLY
loosen the tip guard retaining nut or hose end coupling
to Relieve the pressure gradually, then loosen com-
pletely. Now clear the tip or hose.
Flushing
When to Flush
1.
New Sprayer. This sprayer was factory tested in
lightweight oil,which was left in to protect the pump
parts.
Before using water–base paint,
flush with mineral
spirits, followed by a soapy water flush, and then a
clean water flush.
Before using oil–base paint,
flush with mineral
spirits.
2.
Changing Colors. Flush with a compatible solvent
such as mineral spirits or water.
3.
Changing from water–base to oil–base paint.
Flush
with warm, soapy water, then mineral spirits.
4.
Changing from oil–base to water–base paint.
Flush
with mineral spirits, followed by warm, soapy
water, and then a clean water flush.
CAUTION
To prevent pump corrosion or damage to pump
components, never leave water or any type of paint
in the sprayer when it is not in use. Pump the water
or the paint out with mineral spirits.
5.
Storage.
Water base paint:
flush with water, then mineral
spirits and leave the pump, hose and gun filled
with mineral spirits. Shut off the sprayer, remove
the spark plug cable, and open the pressure drain
valve to Relieve the pressure. Leave the drain
valve open.
Oil base paint:
flush with mineral spirits and leave
the pump, hose and gun filled with mineral spirits.
Shut off the sprayer, remove the spark plug cable,
and open the pressure drain valve to Relieve the
pressure. Leave the drain valve open.
6.
Startup after storage.
Before using water–base paint
, flush out the
mineral spirits with soapy water, and then with
clean water.
When using oil–based paint,
flush out the mineral
spirits with the paint to be sprayed.