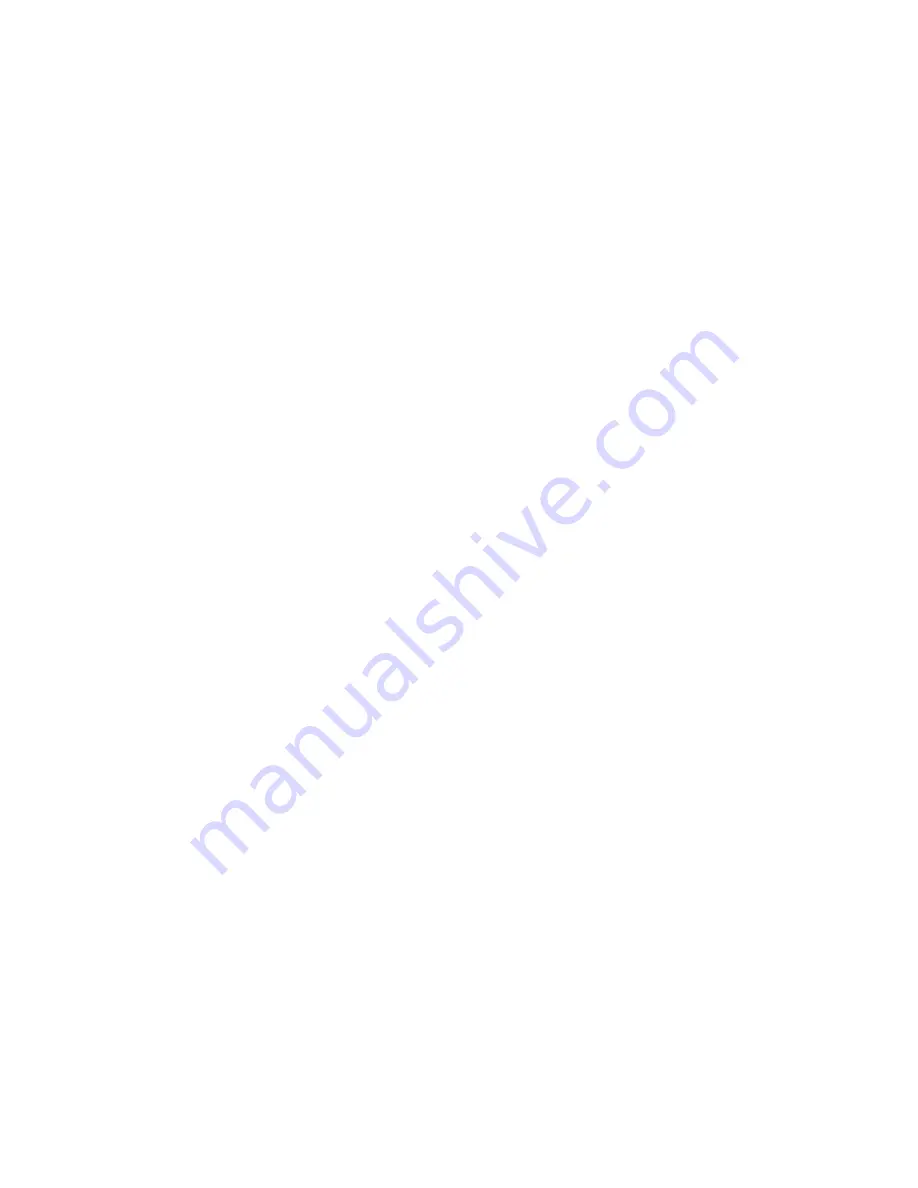
30
NOTE: A bearing frame which feels hot to the touch of
the hand is not necessarily running hot. Check
with an accurate temperature measuring device
to be sure.
Stuffing box
The standard stuffing box consists of rings of packing,
(See assembly section for number of rings) a seal cage,
and a gland. A shaft sleeve which extends through the
box and under the gland is normally provided to
protect the shaft.
A tapped hole is supplied in the stuffing box directly
over the seal cage to introduce a clean, clear sealing
medium. The stuffing box must at all times be supplied
with sealing liquid at a high enough pressure to keep
the box free from foreign matter, which would quickly
destroy the packing and score the shaft sleeve.
Water lubrication
Only a sufficient volume of sealing liquid to create a
definite direction of flow from the stuffing box inward
to the pump casing is required, but the pressure is
important. Apply seal water at a rate of 0.5 - 1.0 GPM,
at 5 - 10 PSI above stuff box operating pressure.
We recommend that piping supplying sealing liquid to
stuffing box be sized to supply a sufficient volume of
water at the required pressure, based on the location
of the pump (or pumps) with respect to the liquid
source. A small pipe can be utilized for the connection
to the stuffing box. A valve should be installed to
adjust and regulate sealing liquid and a gauge
installed to check pressure to the box.
External sealing liquid should be adjusted to the point
where the packing runs only slightly warm, with a very
slow drip from the stuffing box. Excess pressure from
an external source can be very destructive to packing.
More pressure is required, however, for abrasive
slurries than for clear liquids. Examination of the
leakage will indicate whether to increase or decrease
external pressure. If slurry is present in the leakage,
increase the pressure until only clear liquid drips from
the box. If the drippage is corrosive or harmful to
personnel, it should be collected and piped away.
A common error is to open the external piping valve
wide and then control the drippage by tightening the
packing gland. Actually, a combination of both
adjustments is essential to arrive at the optimum
condition. The life of packing and sleeve depends on
this careful control more than any other factor.
Grease lubrication
Pump stuffing boxes are also suitable for grease
lubrication. Several types of grease lubricators are
available. When using a grease lubricator, grease
pressure to the stuffing box should be equal to the
pump discharge pressure.
Packing
All pumps are packed before shipment, unless
otherwise requested. All packings used are the
highest grade material. Before pump is put into
operation, check the condition of the packing. If
pump is installed within 60 days after shipment, the
packing will be in good condition with a sufficient
supply of lubrication. If pump is stored for a longer
period, it may be necessary to repack the stuffing box.
In all cases, however, we recommend an inspection of
the packing before pump is started.
Fiber packing
The standard packing is a soft, square asbestos,
impregnated with oil and graphite. A soft well-
lubricated packing reduces stuffing box resistance,
and prevents excessive wear on the shaft or shaft
sleeve. Many brands of packing on the market have
the desired qualities. For specific recommendations,
consult the factory.
When a pump with fiber packing is first started, it is
advisable to have the packing slightly loose without
causing an air leak. As pump runs in, gradually tighten
the gland bolts evenly. The gland should never be
drawn to the point where packing is compressed
too tightly, and no leakage occurs. This will cause
the packing to burn, score the shaft or shaft sleeve,
and prevent liquid from circulating through the
stuffing box, cooling the packing. The stuffing box is
improperly packed or adjusted if friction in the box
prevents turning the rotating element by hand. A
properly operated packed stuffing box should run
lukewarm with a slow drip of sealing liquid. After the
pump has been in operation for some time and the
packing has been completely run-in, drippage from
the stuffing box should be at least 40 to 60 drops per
minute. This will indicate proper packing and shaft
sleeve lubrication and cooling.
NOTE: Eccentric operation of the shaft, or sleeve,
through the packing could result in excess leakage
that cannot be compensated for. Correction of this
defect is very important.
Packing should be checked frequently and replaced
as service indicates. Six months might be a reasonable
expected life, depending on operating conditions. It is
impossible to give any exact predictions. A packing
tool may be used to remove all old packing from the
stuffing box. Never reuse old and lifeless packing
or merely add some new rings. Make sure that
the stuffing box is thoroughly cleaned before new
packing is installed. Also check the condition of the
shaft or sleeve for possible scoring or eccentricity,
making replacements where necessary.