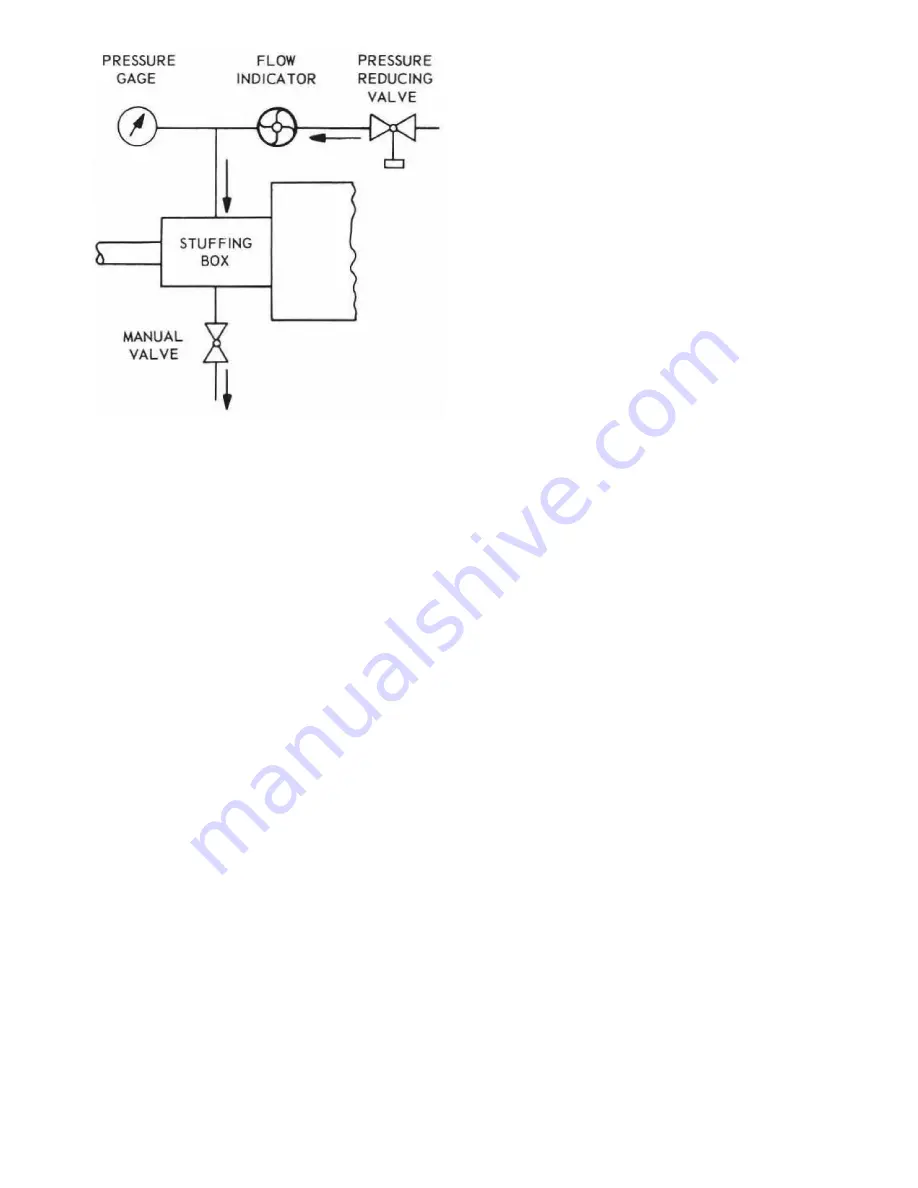
22
therefore, is to use the lowest possible flushing
pressure which the operating conditions will permit.
If the pump system pressure conditions vary during
the day, the packing problem becomes difficult.
Consideration should be given to using a mechanical
seal. (See "Mechanical Seals".)
One recommended method to minimize error in
regulating flushing water is a "Controlled Pressure
System" (Figure 12). Most important is the pressure
reducing valve adjusted to a value slightly exceeding
the maximum stuffing box operating pressure
(assuming it is reasonably constant). A flow indicating
device will serve to indicate a failing of the bottom
packing rings allowing leakage into the pump.
With this arrangement, the packing gland need be
tightened only against the lowest necessary pressure.
Longer packing life and less frequent adjustments
are possible with the "Controlled Pressure System" if
properly installed and operated. (See "Stuffing Box
Operating Pressure".)
Packing
Standard pumps are normally packed before
shipment. If the pump is installed within 60 days after
shipment, the packing will be in good condition with
a sufficient supply of lubrication. If the pump is stored
for a longer period, it may be necessary to repack the
stuffing box. In all cases, however, inspect the packing
before the pump is started.
NOTE: Packing adjustment is covered on page 31.
Figure 12 - Controlled pressure system
for stuffing box
Packing lubrication
Internal liquid lubricant
Pumped liquid may be used to lubricate the packing
when the following conditions prevail:
1. Liquid is clean, free from sediment and chemical
precipitation and is compatible with seal materials.
2. Temperature is above 32°F and below 160°F.
3. Suction pressure is below 75 psig.
4. Liquid has lubricating qualities.
5. Liquid is non-toxic and non-volatile.
External liquid lubricant
When the liquid being pumped contains solids or is
otherwise not compatible with packing materials, an
outside supply of seal liquid should be furnished. In
general, external-injection liquid (from an outside
source) is required when the following conditions
prevail:
1. Liquid being pumped contains dirt, grit, or
other impurities.
2. Temperature of the pumped liquid is below
32°F or above 160°F.
3. Liquid being pumped has non-lubricating
properties.
4. Liquid is toxic or volatile.
5. Suction pressure is above 75 psig, vacuum,
or high lift.
Stuffing box operating
pressure
The actual stuffing box operating pressure may be
obtained by installing a pressure gauge on the box.
This is done with an extra seal cage temporarily
replacing the two rings of packing in the bottom
of the box to obtain accurate gauge readings. Take
gauge readings with the pump running under
various head and capacity conditions. Then set the
pressure of flushing or lubrication liquid at a value
5 to 10 psi above the maximum expected stuffing box
operating pressure.
Even under the best conditions, a properly packed
stuffing box should be watched closely. If pressure
conditions change slightly, there will be a resultant
change in packing "seating" which should be
compensated by a change in gland adjustment.
Consideration should also be given to the lubrication
pressure. A wide variation indicates a need to use a
mechanical seal.
Mechanical seals
Mechanical seals are preferred over packing on some
applications because of better sealing qualities and
longer serviceability. Leakage is eliminated when
a seal is properly installed, and normal life is much
greater than that of packing on similar applications.