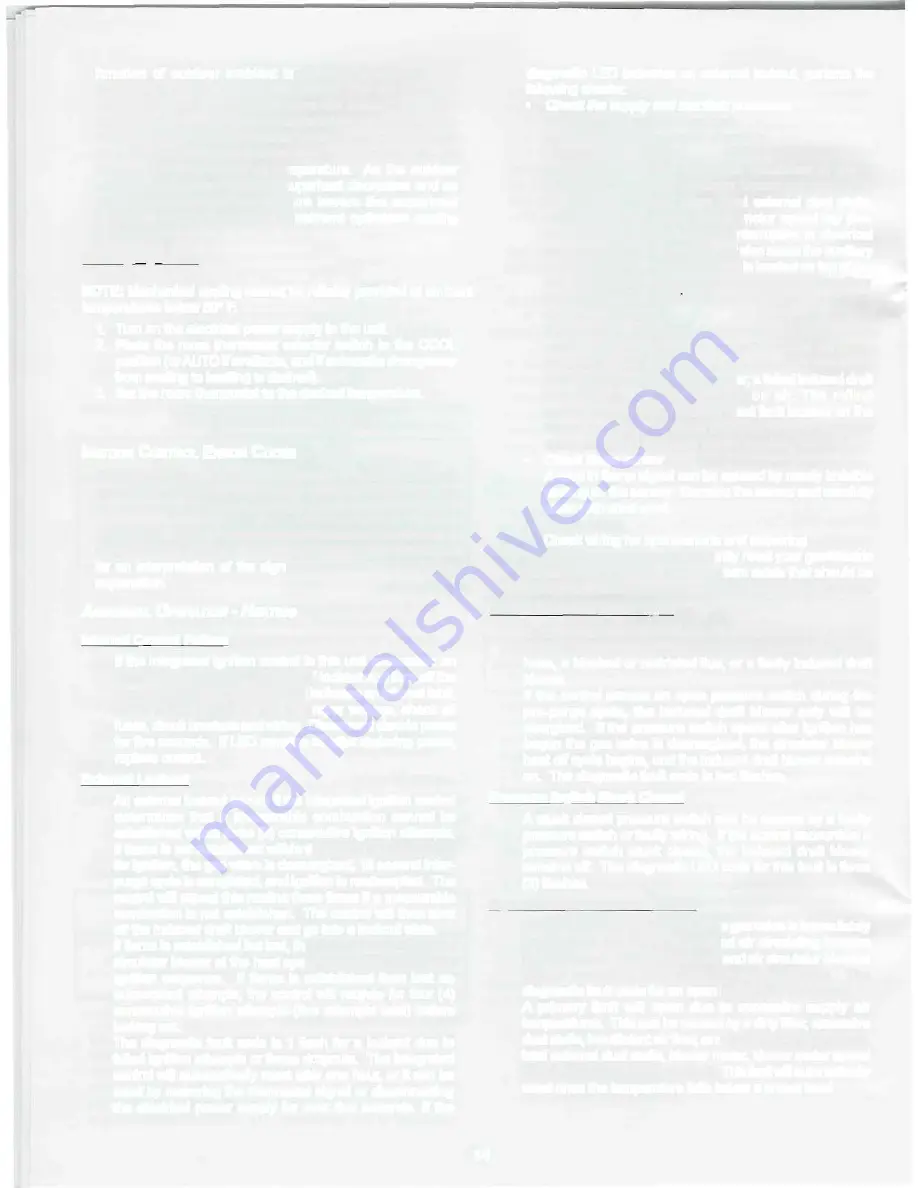
function of outdoor ambient temperature and return air
temperature of the conditioned space. It is the installing
contractors responsibility to ensure the proper refrigerant
superheat at the compressor is adjusted for each application.
For example, 10 degree refrigerant superheat level is adequate
for a 95 degree outdoor ambient temperature and a 78 - 80
degree for indoor return air temperature. As the outdoor
ambient temperature rises the superheat decreases and as
the outdoor ambient temperature lowers the superheat
increases. Proper superheat adjustment optimizes cooling
performance.
Cooling Operation
NOTE: Mechanical cooling cannot be reliably provided at ambient
temperatures below 50° F.
1. Turn on the electrical power supply to the unit.
2. Place the room thermostat selector switch in the COOL
position (or AUTO if available, and if automatic changeover
from cooling to heating is desired).
3. Set the room thermostat to the desired temperature.
TROUBLESHOOTING
IGNITION CONTROL ERROR CODES
The following presents probable causes of questionable unit
operation. Refer to Diagnostic indicator Chart for an
interpretation of the signal and to this section for an explanation.
Remove the control box access panel and note the number of
diagnostic LED flashes. Refer to Diagnostic Indicator Chart
for an interpretation of the signal and to this section for an
explanation.
ABNORMAL OPERATION - HEATING
Internal Control Failure
If the integrated ignition control in this unit encounters an
internal fault, it will go into a "hard" lockout and turn off the
diagnostic LED. If diagnostic LED indicates an internal fault,
check power supply to unit for proper voltage, check all
fuses, circuit breakers and wiring. Disconnect electric power
for five seconds. If LED remains off after restoring power,
replace control.
External Lockout
An external lockout occurs if the integrated ignition control
determines that a measurable combustion cannot be
established within three (3) consecutive ignition attempts.
If flame is not established within the seven (7) second trial
for ignition, the gas valve is deenergized, 15 second inter-
purge cycle is completed, and ignition is reattempted. The
control will repeat this routine three times if a measurable
combustion is not established. The control will then shut
off the induced draft blower and go into a lockout state.
If flame is established but lost, the control will energize the
circulator blower at the heat speed and then begin a new
ignition sequence. If flame is established then lost on
subsequent attempts, the control will recycle for four (4)
consecutive ignition attempts (five attempts total) before
locking out.
The diagnostic fault code is 1 flash for a lockout due to
failed ignition attempts or flame dropouts. The integrated
control will automatically reset after one hour, or it can be
reset by removing the thermostat signal or disconnecting
the electrical power supply for over five seconds. If the
diagnostic LED indicates an external lockout, perform the
following checks;
• Check the supply and manifold pressures
• Check the gas orifices for debris
• Check gas valve for proper operation
• Check secondary limit
A dirty filter, excessive duct static, insufficient air flow, a
faulty limit, or a failed circulator blower can cause this
limit to open. Check filters, total external duct static,
circulator blower motor, blower motor speed tap (see
wiring diagram), and limit. An interruption in electrical
power during a heating cycle may also cause the auxiliary
limit to open. The secondary limit is located on top of the
circulator blower assembly. The automatic reset auxiliary
limit is located on the circulator blower scroll.
• Check rollout limit
If the burner flames are not properly drawn into the heat
exchanger, the flame rollout protection device will open.
Possible causes are restricted or blocked flue passages,
blocked or cracked heat exchanger, a failed induced draft
blower, or insufficient combustion air. The rollout
protection device is a manual reset limit located on the
burner bracket. The cause of the flame rollout must be
determined and corrected before resetting the limit.
• Check flame sensor
A drop in flame signal can be caused by nearly invisible
coating on the sensor. Remove the sensor and carefully
clean with steel wool.
• Check wiring
Check wiring for opens/shorts and miswiring.
Important: If you have to frequently reset your gas/electric
package unit, it means that a problem exists that should be
corrected. Contact a qualified servicer for further information.
Pressure Switch Stuck Open
A pressure switch stuck open can be caused by a faulty
pressure switch, faulty wiring, a disconnected or damaged
hose, a blocked or restricted flue, or a faulty induced draft
blower.
If the control senses an open pressure switch during the
pre-purge cycle, the induced draft blower only will be
energized. If the pressure switch opens after ignition has
begun the gas valve is deenergized, the circulator blower
heat off cycle begins, and the induced draft blower remains
on. The diagnostic fault code is two flashes.
Pressure Switch Stuck Closed
A stuck closed pressure switch can be caused by a faulty
pressure switch or faulty wiring. If the control encounters a
pressure switch stuck closed, the induced draft blower
remains off. The diagnostic LED code for this fault is three
(3) flashes.
Open Thermal Protection Device
If the primary limit switch opens, the gas valve is immediately
deenergized, the induced draft and air circulating blowers
are energized. The induced draft and air circulator blowers
remain energized until the limit switch recloses. The
diagnostic fault code for an open limit is four (4) flashes.
A primary limit will open due to excessive supply air
temperatures. This can be caused by a dirty filter, excessive
duct static, insufficient airflow, or a faulty limit. Check filters,
total external duct static, blower motor, blower motor speed
tap (see wiring diagram), and limit This limit will automatically
reset once the temperature falls below a preset level.
14