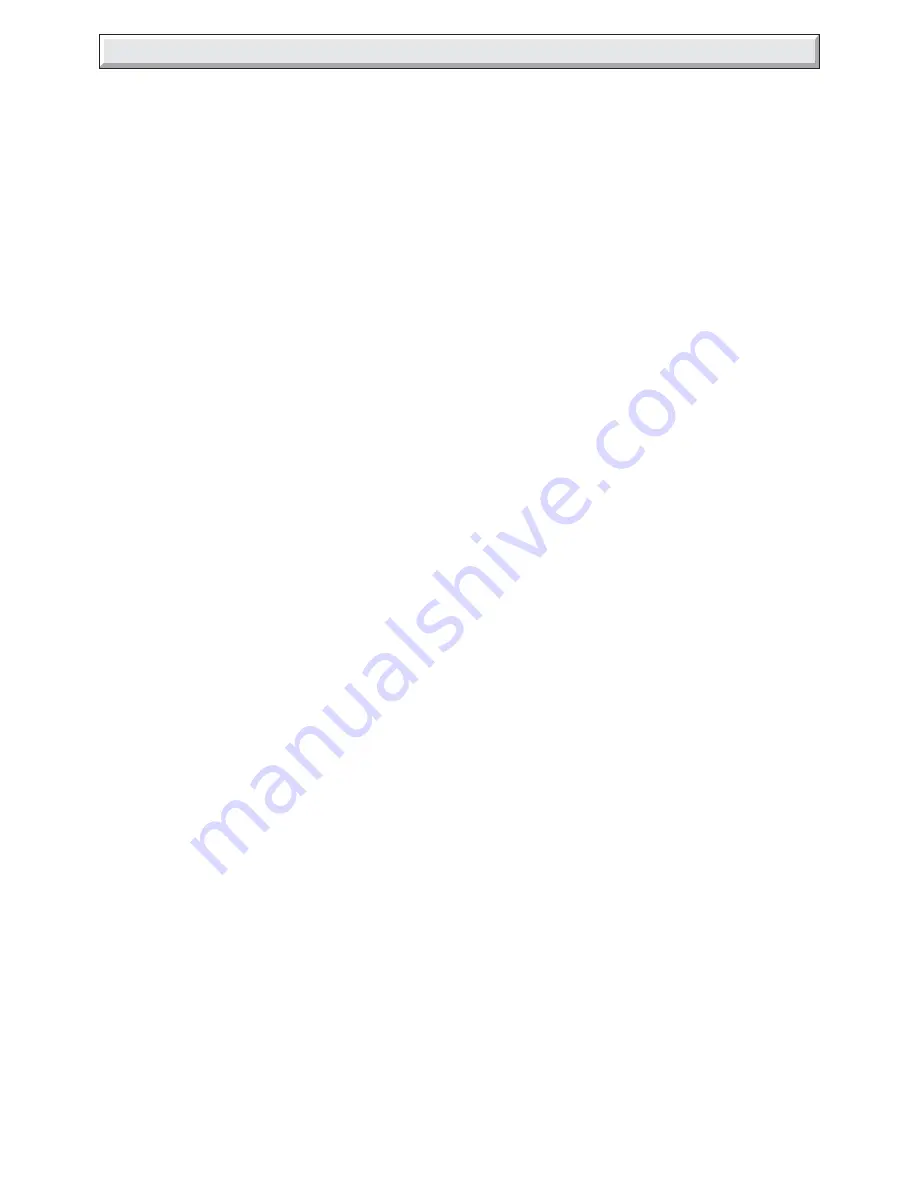
27
2000225065A
11 Commissioning
Note that after first power up the firing sequence for central
heating changes. After one minute stabilisation time the boiler
will ramp slowly to full rate rather than going immediately to full
rate. This is an adaptive feature to cope with small system
requirements.
11.5 Testing - Gas
Should any doubt exist about the gas rate, check it using the
gas meter test dial and stop watch at least 10 minutes after the
burner has lit, making sure that all other gas burning appliances
and pilot lights are off.
The approximate gas rates: 24cxi : 2.24m
3
/h (79ft
3
/h)
30cxi : 2.8m
3
/h (99ft
3
/h)
38cxi : 3.6m
3
/h (127ft
3
/h)
are for guidance only.
The gas valve is factory set and should need no adjustment. It
should be checked that the supply pressure is 20mbar when the
boiler is firing at full rate. This can be achieved by turning on
several hot water taps and checking the inlet pressure at the
tapping on the gas valve shown in diagram 11.2. Turn taps off
and disconnect pressure gauge.
Note that the burner pressure cannot be measured at the gas
valve as it is altered by the suction of the fan and modulated
according to demand.
11.6 Testing - Heating System
Check that all remote controls are calling for heat. The boiler will
fire automatically. Fully open all radiator valves, flow control
valve ‘A’, if fitted, see diagram 4.1.
Balance the radiators as required and if fitted adjust valve ‘A’ to
give the required system differential. Turn off all radiators that
can be shut off by the user and check to see if less than the
maximum differential allowed of 20
o
C can be achieved across
flow and return.
This boiler has a built in bypass, see diagram 11.3.
The boiler is supplied with the bypass open half a turn. It should
not be necessary to adjust the bypass, but if required turn the
adjustment screw clockwise to close the valve, see diagram
11.3.
Allow the system to reach maximum temperature then switch
off the boiler by isolating from the electrical supply.
Drain the entire system rapidly whilst hot, using the drain tap at
the lowest part of the system. Fill and vent the system as
described previously in section 11.2.
Lock or remove the handle from control valve ‘A’, if fitted.
Replace inner casing panel and front casing panel.
11.7 User Controls and Options
The mains reset on/off switch is used to restart the boiler after
a fault condition has occurred, i.e. ignition failure, low water
pressure or high water temperature.
The central heating and domestic hot water control knobs allow
the user to set the temperatures in each mode.
Note: If there is no demand the digital display shows the water
pressure.
Temperature Display
The digital display normally shows the operating temperature
of the unit when there is a central heating demand.
Holiday Mode
Normal mode uses the domestic hot water and central heating
temperatures selected.
By turning the domestic hot water and central heating control
knobs to minimum setting the holiday mode is set up. However,
frost protection and pump exercise programme remain active.
By doing this the DHW will operate without pre-heat and DHW
will set at maximum temperature. To resume normal operation
after a holiday period, return the control knobs to their original
position.
11.8 Pump Exercise Program
After a power cut or every 24 hours in holiday mode the three
way valve will switch and the pump will run to prevent the
components from sticking. This will also occur during normal
operating if there is no domestic or central heating demand for
more than 24 hours.
11.9 Frost Protection
The boiler has a built in frost protection programme as long as
the electricity and gas are left switched on.
This device operates the appliance pump when the temperature
inside the boiler falls below 7
°
C and circulates water around the
appliance only.
If the temperature falls to 3
°
C the burner is lit and water
circulates around the heating system.
When the temperature inside the appliance reaches 10
°
C the
burner will shut down and after a short period the pump will stop.
This device primarily protects the boiler. Any other exposed
areas of the system should be protected by a separate frost
thermostat.
11.10 Instruct the User
Instruct and demonstrate the lighting procedure and advise the
user on the safe and efficient operation of the boiler.
Instruct on and demonstrate the operation of any heating
system controls.
Advise the user on the use and maintenance of any scale
reducer and pass on any relevant instructional documents.
Advise that to ensure the continued efficient and safe operation
of the boiler it is recommended that it is checked and serviced
at regular intervals. The frequency of servicing will depend upon
the installation conditions and usage, but in general, once a
year should be enough.
Draw attention, if applicable, to the current issue of the Gas
Safety (Installation and Use) Regulations, Section 35, which
imposes a duty of care on all persons who let out any property
containing a gas appliance in the UK.
It is the Law that any servicing is carried out by a competent
person.
Advise the user that, like all condensing boilers this appliance
will produce a plume of condensation from the flue terminal in
cool weather. This is due to the high efficiency and hence low
flue gas temperature of the boiler.
Advise the user of the precautions necessary to prevent damage
to the system, boiler and the building, in the event of the heating
system being out of use during frost or freezing conditions.
Advise the user that the permanent mains electrical supply
SHOULD NOT be switched off, as the built in frost protection
and pump/valve saver program would not be operable.
Reminder, leave these instructions and the ‘Benchmark’ logbook
with the user.
For IE, it is necessary to complete a "Declaration of Conformity"
to indicate compliance to I.S.813. An example of this is given in
the current edition of I.S.813.