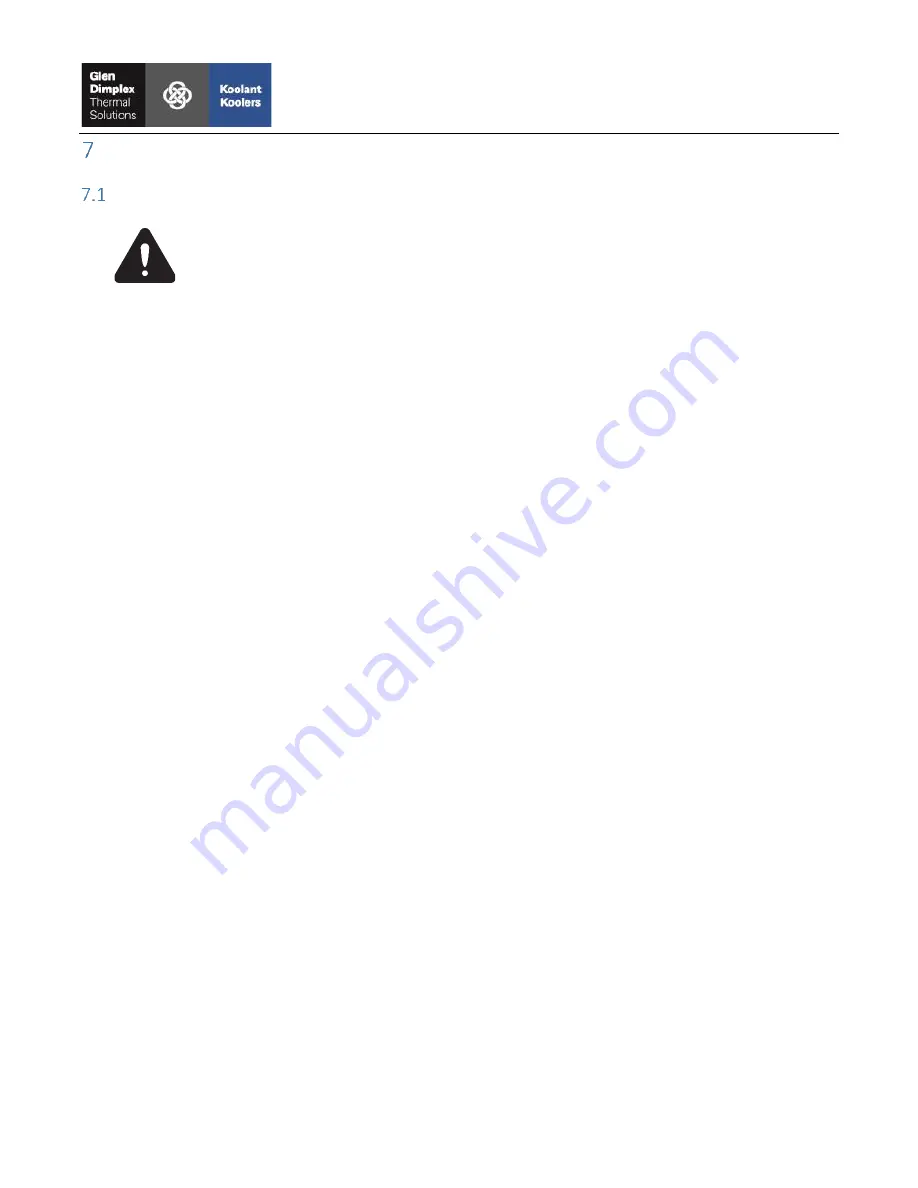
Operation
19
Operation
Initial Startup
WARNING
Risk of improper startup. Failing to complete the installation checklist could cause
damage to the chiller.
The following startup procedures must be adhered to in sequence. This outline should be used as a checklist for
the initial startup and for subsequent startups if the chiller is taken out of service for a prolonged period.
1.
Verify that the main power sourc
e to the chiller meets the requirements on the chiller’s data tag
(located on the electrical enclosure).
2.
Verify that all electrical connections have been correctly and securely wired.
3.
Verify that all process plumbing connections between the chiller and process are installed correctly,
securely, free of leaks and are not dead-headed (no kinks in hoses, valves fully opened, etc.).
4.
Verify that the coolant reservoir level on the visual indicator is between the high and low levels
5.
Enable the main power to the chiller (turn on any breakers or switches upstream of the chiller if
required).
6.
Allow the chiller to be energized in this state for at least 8 hours prior to commissioning.
7.
Phase monitor light must be green and master controller alarms should be clear.
8.
If pump motors do not start, check incoming power for correct sequence. If incoming power is present,
check any faults on the master controller. Reset any faults which may be present.
9.
Proceed to run the chiller pump for five minutes or more to allow any air in the system to be vented.
Check the fluid level after the air has been purged from the piping and refill the reservoir as needed.
10.
Check the controller for fault messages. Clear faults that may have occurred during startup procedure. If
faults do not re-occur, the system is ready for continuous duty.
NOTICE
The chiller must be powered (supplied with incoming power and main disconnect
handle turned to the ON position) for at least 8 hours before being started for the
first time. (Power can be off for 30 minutes without observing the 8-hour pre-heat
requirement) This is required to energize the compressor
’
s crankcase heaters to
vaporize any liquid refrigerant in the compressor crankcase.
Starting the chiller
with liquid refrigerant in the compressor crankcase will damage the compressor
and eventually lead to failure of the compressor and refrigeration circuit. This
will also void the warranty.
7.1.1
Temperature control
The chiller will maintain coolant supply temperatures to the process according to its set-point. Temperature
control over a wide range of heat loads is achieved through closed-loop control mechanisms. No manual
intervention is required other than during the occurrence of faults.
Содержание Koolant Koolers WO2-2-10000
Страница 1: ...Original Instructions 800 968 5665 dimplexthermal com User Manual...
Страница 17: ...Installation 11 Figure 7 Removal or Doors Blockers 3 8 DOOR BOLT 3 8 BLOCKER BOLT BLOCKER DOOR...
Страница 18: ...Installation 12 Figure 8 Removal of Lower Doors LATCHES...
Страница 28: ...Operation 22 Figure 10 Controller Restart Warning Figure 11 Controller Home Page...
Страница 30: ...Operation 24 Figure 15 Controller On Off Menu Figure 16 Controller Pump Enable Disable Menu...
Страница 31: ...Operation 25 Figure 17 Controller Setpoint Menu Figure 18 Controller Alarm Menu...
Страница 37: ...Internal Components 31 Figure 20 Door Side PUMP 2 PUMP 1 FLOAT SWITCH...
Страница 44: ...Appendix A Plumbing 38 Appendix A Plumbing...
Страница 45: ...Appendix B Pump Curve 39 Appendix B Pump Curve...
Страница 46: ...Appendix C Refrigeration WO2 2 5000 40 Appendix C Refrigeration WO2 2 5000...
Страница 47: ...Appendix C Refrigeration WO2 2 7500 41 WO2 2 7500...
Страница 48: ...Appendix C Refrigeration WO2 2 10000 42 WO2 2 10000...
Страница 53: ...Appendix G Chiller Registration 47...