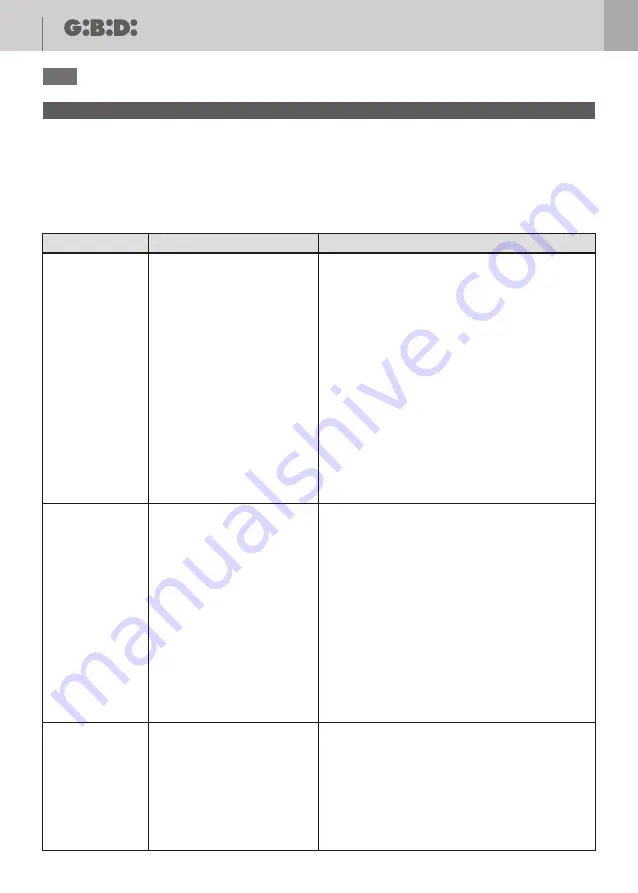
36
DPT260
11 - PROBLEMS AND SOLUTIONS
The bollard rises
of about 10 cm,
stops and then
returns in low
position (without
any lowering
control). (C001)
The bollard rises
but not comple-
tely. (C002)
When in low
position the
moving cylinder is
about 7 mm lower
than the fix crown
device. (C003)
The safety pressure switch which
detects the presence of about
40 Kg weight on the bollard head is
constantly in ON position and for
this reason it must be adjusted or
replaced.
• The hydraulic unit does not have
enough oil in the tank.
• Bollard's electric cables are not
well placed in the pit, so when
the bollard rises the upper limit
switch gets stuck in the cable,
blocking the complete rising.
The vulcanized hard rubber of the
lower base supports is worn.
PROBLEM
POSSIBLE CAUSE
SOLUTION
When the bollard is in low position check the LEDs L1 on
the master and/or the slave unit in the control unit:
switched off = the pressure switch is ok – turned on = the
pressure switch is in alarm (it is on) – if the LED is always
turned ON or turns ON when the bollard starts rising, the
problem is caused by the safety pressure switch which
must be adjusted or replaced.
For the pressure switch adjustment please consult the
chapter 10: SPECIFIC OPERATIONS.
Note: generally only the pressure switches of old supply
are adjustable and recognizable from a waterproof
protection made by black soft rubber; the current
pressure switches are preadjusted and hermetic to
increase the IP grade of protection.
• Check and fix any possible oil leak in the hydraulic
system, verifying the proper fastening of the hydraulic
fittings. Top up oil in the hydraulic pump. For the
topping up procedure please read the chapter 10:
SPECIFIC OPERATIONS.
• Pull the bollard out from the pit and perform a rising in
order to verify if the rising is complete up to the top; if
confirmed, replace the bollard in the pit making sure that
the electrical cables are placed adhere to the wall of the
pit and that they do not tangle themselves too close to
the bollard.
Replace the lower base supports.
UK
This guide shows the most common problems that can occur while using a Gi.Bi.Di. system.
Client's technicians can solve some problems indipendently (especially if they are equipped with spare parts), while
for other troubles it may be necessary to be supported by Gi.Bi.Di. S.r.l assistance department.
In this case they have to contact Gi.Bi.Di. S.r.l., communicate the reference number of the system (or the reference
number of the order confirmation).