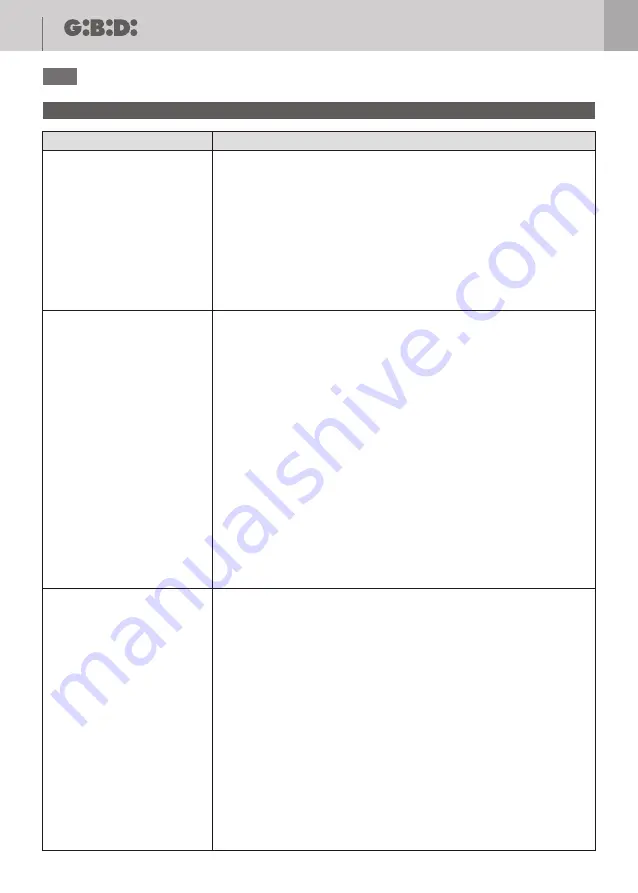
32
DPT260
10 - SPECIFIC OPERATIONS
Topping up of the hydraulic
unit. (B001)
Oil topping up of the hydraulic
unit with E.F.O. circuit. (B002)
Operation
Procedure
• Lift the bollard out of pit, lower it to down position then turn the power off.
• Unfasten and remove the black cap of the hydraulic pump (placed above the
transparent spyhole) and fill it with the same oil up to half of the spyhole.
• ATTENTION: USE ONLY ORIGINAL OIL.
• ATTENTION: CHECK IF IT IS MINERAL OIL OR BIODEGRADABLE OIL.
• Turn the 230V power supply on and rise the bollard to up position.
• Once the bollard is up and the hydraulic unit is still (end of the rising cycle),
close the black cap of the hydraulic pump.
• Lift the bollard out of pit, lower it to down position then turn the power off.
• Discharge the hydraulic accumulator of the E.F.O circuit by pushing
simultaneously the two red push buttons for 10s: the one for E.F.O solenoid
valve and the one for emergency lowering. To confirm that the hydraulic
accumulator is completely discharged, check that the moving cylinder remains
down after pushing the push button of the E.F.O solenoid valve.
• Check the oil level in the hydraulic pump through the suitable spyhole.
• Unfasten and remove the black cap of the hydraulic pump (generally placed
above the transparent spyhole) and fill it with the same oil up to about half of the
spyhole.
• ATTENTION: USE ORIGINAL OIL ONLY.
• ATTENTION: CHECK IF IT IS MINERAL OR BIODEGRADABLE OIL.
• Turn the 230V power supply on and rise the bollard to up position.
• Once the bollard is up and the hydraulic unit is still (end of the rising cycle) close
the black cap of the hydraulic pump.
Check/replacement of the
lowering solenoid valve. (B003)
• Lift the bollard out of pit, lower it to down position then turn the power off.
• Unfasten the black cap of the hydraulic pump of about 2 turns (to reset the
internal pressure of the pump).
• Remove the coil from the solenoid valve.
• Unfasten and remove the solenoid valve by means of a fixed wrench size 24
(some oil leaks may occur, use cloth to wipe it clean).
• Verify that the lower part of the solenoid valve is not mechanically obstructed by
impurities such as metal swarf or similar (in presence of impurities, it is
suggested to clean, reassemble the solenoid valve and run functional tests;
otherwise use a new solenoid valve).
• Fasten the solenoid valve and the coil.
• In case of negative logic solenoid valve, on the top there is a push button for
emergency manual lowering, it is recommended to lubricate it and check the
proper operation.
UK
CONTINUES NEXT PAGE