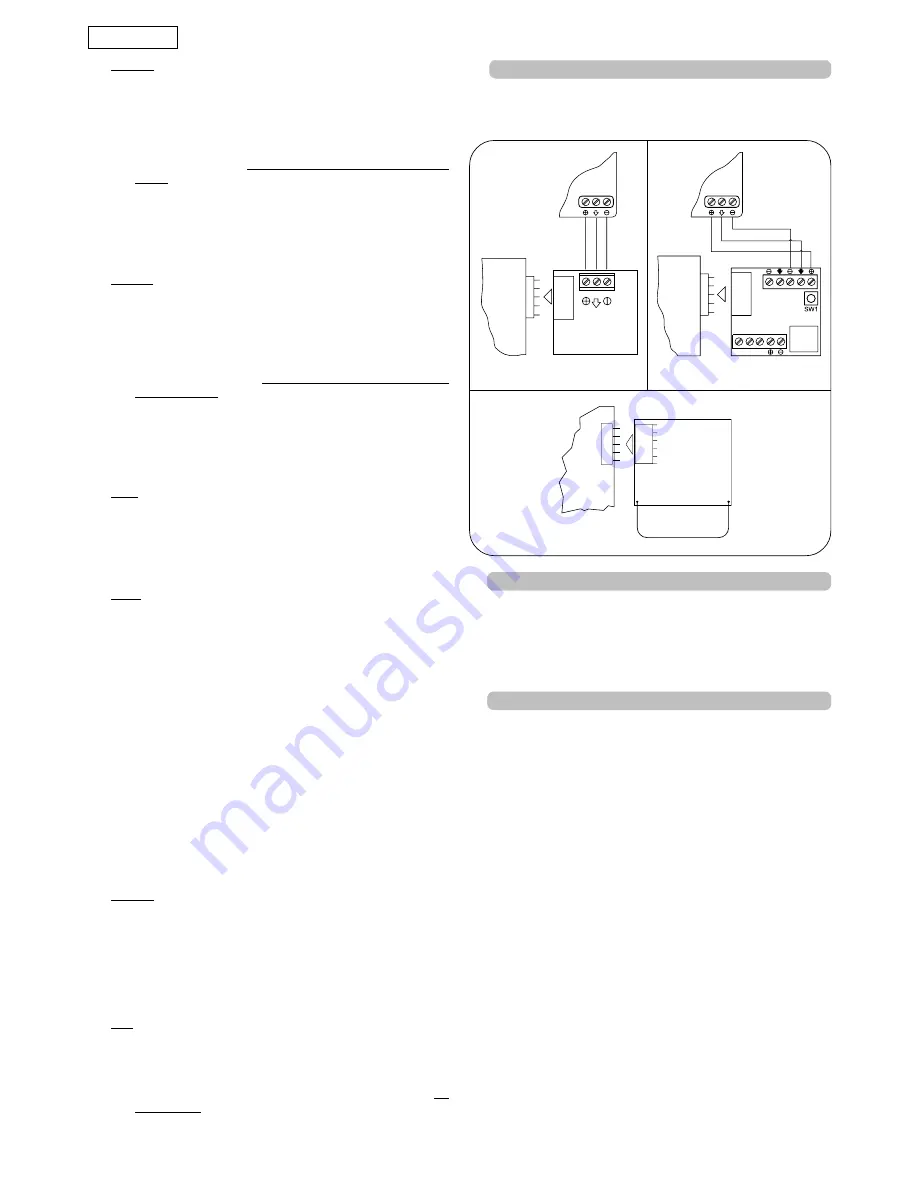
12
ENGLISH
FSW OP - Opening safety devices contact (terminal 3):
The
purpose of the opening safety devices is to protect the leaf
movement area during opening.
During opening, in the
A-
AP-S-E-EP
logics the safety devices reverse the movement
of the gate leaves, or stop and restart the movement when
they are released (see advanced programming in Chpt
5.2). During the opening cycle in logics
B
and
C
, they
interrupt movement. They never operate during the closing
cycle.
If the
Opening safety devices
are engaged when the gate
is closed, they prevent the leaf opening movement.
To install several safety devices, connect the N.C. contacts
in series (fig.4).
NB.: If no opening safety devices are connected, jumper
connect inputs OP and -TX FSW
(fig. 5).
FSW CL - Closing safety devices contact (terminal 4):
The
purpose of the closing safety devices is to protect the leaf
movement area during closing. During closing, in the
A-
AP-S-E-EP
logics, the safety devices reverse the movement
of the gate leaves, or stop and reverse the movement
when they are released (see advanced programming in
Chpt 5.2). During the closing cycle in logics
B
and
C
, they
interrupt movement. They never operate during the
opening cycle. If the
Closing safety devices
are engaged
when the gate is open, they prevent the leaf closing
movement.
To install several safety devices, connect the N.C. contacts
in series (fig.4).
NB.: If no closing safety devices are connected, jumper
connect terminals CL and -TX FSW
(fig. 5).
STOP
- STOP contact (terminal 5):
any device (e.g. a push-
button) which, by opening a contact, is able to stop
gate movement.
To install several STOP devices, connect the N.C. contacts
in series.
NB.:
If STOP devices are not connected, jumper connect
the
STP
and
-
terminals.
EDGE - EDGE safety device contact (terminal 6):
The purpose of
the "edge" safety device is to protect the leaf movement
area during opening/closing against fixed obstacles (pillars,
walls, etc.). In all logics, during opening and closing, the
safety devices reverse gate leaf movement for 2 seconds.
If the safety devices operate again during the 2-seconds
reversing time, they STOP movement without any reversing.
If the
Edge safety devices
are engaged while the gate is
closed or open, they prevent the leaves movement.
To install several safety devices, connect the N.C. contacts
in series (fig.4).
NB.: If edge safety devices are not connected, jumper
connect the EDGE and - inputs.
(fig. 5).
–
Negative for power supply to accessories (terminals 7 and
8)
+
24 Vdc - Positive for power supply to accessories (terminals
9 and 10)
Important:
Accessories max. load is 500 mA. To calculate
absorption values, refer to the instructions for individual
accessories.
TX -FSW - Negative for power supply to photocell transmitters
(terminal 11)
If you use this terminal for connecting the negative for
supplying power to the photocell transmitters, you may,
if necessary, also use the FAIL SAFE function (see advanced
programming in Chpt 5.2).
If this function is enabled, the equipment checks
operation of the photocells before every opening or
closing cycle.
W.L. - Power supply to indicator-light / timed output (terminal
12)
Connect a 24 Vdc - 3 W max indicator-light or timed
output, if necessary, between this terminal and the +24V
supply (see advanced programming in Chpt 5.2).To
avoid geopardising correct operation of the system,
do
not exceed
the indicated power.
Fig. 16
Fig. 15
Fig. 17
MINIDEC
PLUS
PLUS
DECODER
RP
4.5. Connector J2 - Rapid connection to Minidec, Decoder and RP
This is used for rapid connection of Minidec, Decoder and RP
receivers (see fig. 15, 16 and 17). Connect the accessory, with the
components side facing the inside of the board. Insert and remove
after cutting power.
4.6. Connector J6 - Limit-switches rapid connection (fig.2)
This input is intended for rapid connection of the opening and
closing limit-switches designed to stop the leaf, or for start of
decelerations or for braking (see advanced programming in
Chpt. 5.2.). In gearmotors with a built-in control unit, this connection
is pre-wired as standard (fig. 2). For leaf opening direction, see
advanced programming in Chpt 5.2.
4.7. Connector J3 - Encoder rapid connection (fig.2)
This input is designed for rapid connection of the Encoder
(optional). To fit the encoder on the motor, refer to the relevant
instructions.
The presence of the encoder is signalled - when the gearmotor
is running - by the flashing of the "Encoder" LED on the board.
When the encoder is used, the control unit knows the exact
position of the gate while it is moving.
The encoder controls the adjustments of some of the control
unit's functions in a different way (partial opening or deceleration
- see advanced programming in Chpt 5.2) and as an anti-
crushing device.
If the gate strikes an obstacle during opening or closing, the
encoder immediately reverses the gate leaf for 2 seconds. If the
encoder operates again during the 2-seconds reversing time,
it STOPS movement without commanding any reversing.
JA383
JA383
JA383
Содержание JA383
Страница 23: ...note notes note notas anmerkung ...
Страница 24: ...note notes note notas anmerkung ...
Страница 25: ...note notes note notas anmerkung ...
Страница 26: ...note notes note notas anmerkung ...