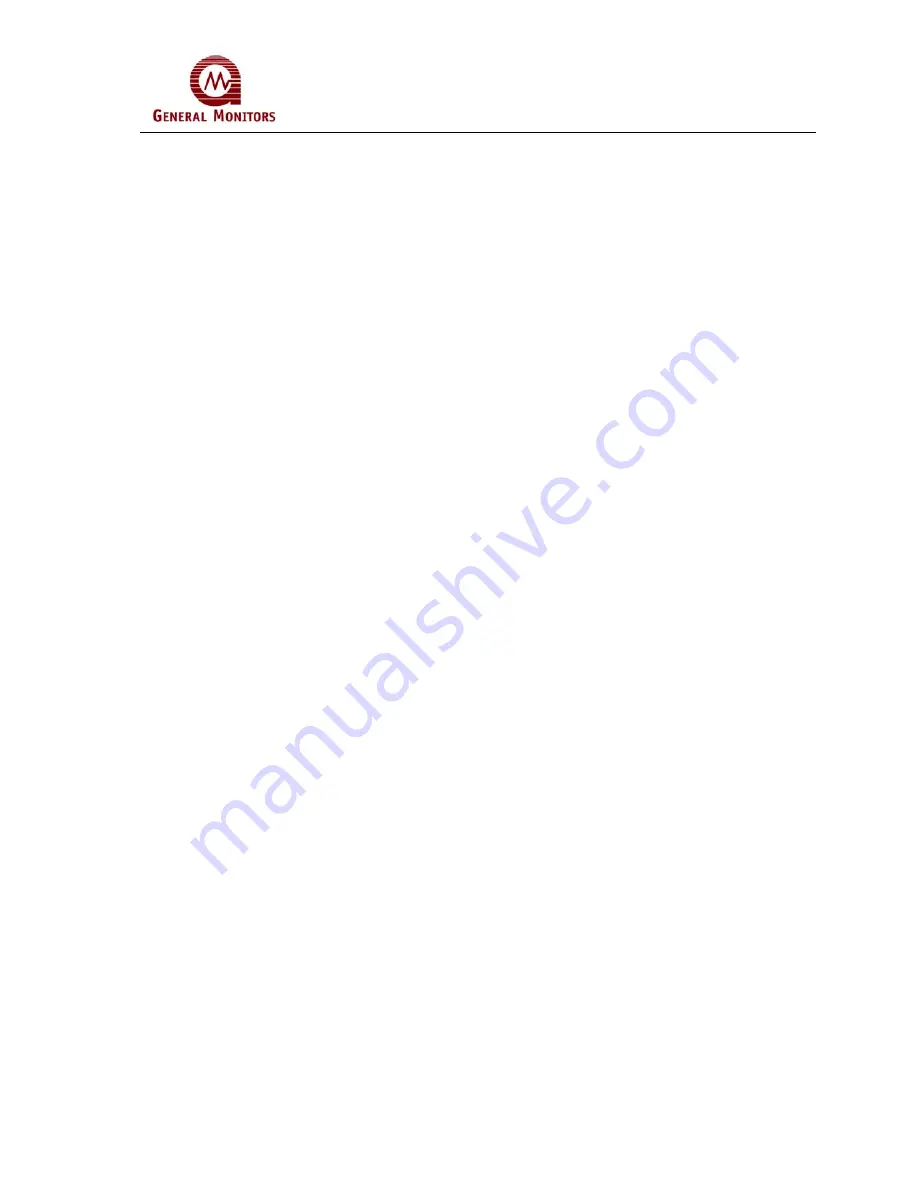
iv
Model TA502A
System Integrity Verification
General Monitors’ mission is to benefit society by providing solutions through industry
leading safety products, services and systems that save lives and protect capital
resources from the dangers of hazardous flames, gases and vapors.
The safety products you have purchased should be handled carefully and installed,
calibrated and maintained in accordance with the respective product instruction
manual. Remember these products are for your safety. To ensure operation at
optimum performance, General Monitors recommends that certain maintenance
items be performed.
Commissioning Safety Systems
Before power up, verify wiring, terminal connections and stability of mounting for all
integral safety equipment including, but not limited to:
•
Power
supplies
•
Control
modules
•
Field detection devices
•
Signaling / output devices
•
Accessories connected to field and signaling devices
After the initial application of power (and any factory specified warm-up period) to the
safety system, verify that all signal outputs, to and from devices and modules, are
within the manufacturers’ specifications. Initial calibration, calibration checking, and
testing should be performed per the manufacturers’ recommendations and
instructions. Proper system operation should be verified by performing a full,
functional test of all component devices of the safety system, ensuring that the proper
levels of alarming occur.
Fault/Malfunction circuit operation should be verified.
Periodic Testing/Calibration of Field Devices
Periodic testing/calibrating should be performed per the manufacturers’
recommendations and instructions. Testing/Calibrating procedures should include,
but not be limited to:
•
Verify
zero
reading
•
Apply a known concentration of gas, or a simulated test device provided by
the manufacturer
•
Verify integrity of all optical surfaces and devices
•
For flame detectors, use the appropriate test lamp