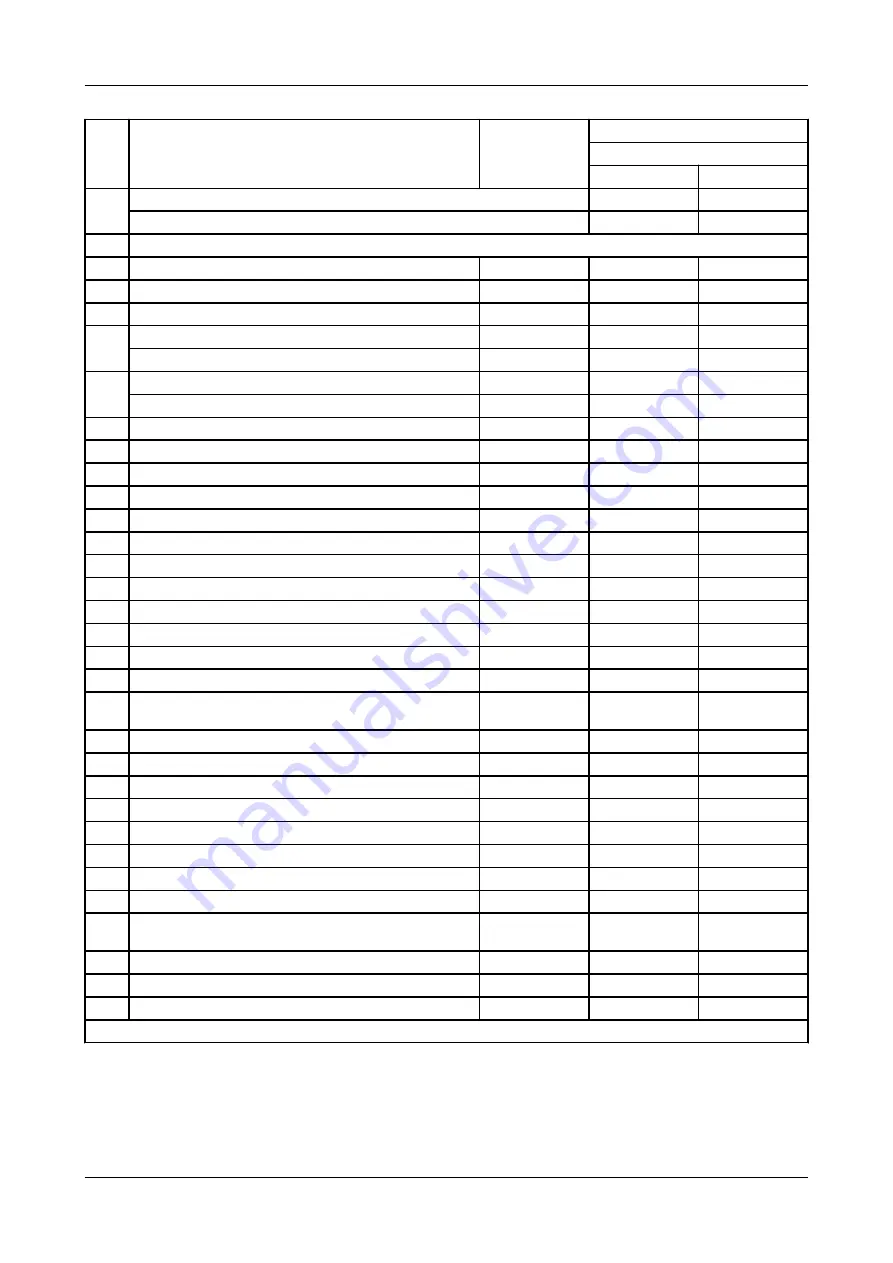
Item
Designation
Material
Material no.
Air connections
Metric
Inch
B
Control Top T.VIS P-15
221-739.33
221-739.35
Control top T.VIS P-15/RM (for position feedback only, binary signals)
221-739.34
221-739.36
1*
For switch bar T.VIS P-15 refer to spare parts list 221ELI010731DE
5
Base T.VIS T-18
PA12/L
221-646,100
221-646,100
5.1
Filter
PE
221-003869
221-003869
6
Screw-in plug connection
MS CV
933-176
933-173
7*
Cap T.VIS P-15/A-15 with button
PA12/L
221-646.87
221-646.87
Hood T.VIS M/A-15
PA12/L
221-646.88
221-646.88
8
Pneumatic block T.VIS-18/3PV/NOT
PA12/L
221-646.90
221-646.90
Pneumatic block with NOT/ASG for ASEPTOMAG valves*
PA12/L
221-646.93
221-646.93
9
Sensor module T.VIS P/A-15
--
221-589.74
221-589.74
15*
Clamp connection KU
--
221-507.08
221-507.08
21
Sound absorber G1/8''
MS CV
933-175
933-175
22
Locking screw
PE-HD
922-369
922-369
23
Plug
PP
922-281
922-280
24
Connector M12/5-pin/A-coded/M20/cpl.
--
221-005101
221-005101
26
Sound absorber G1/4''
MS CV
933-174
933-174
31
O-ring
NBR
930-041
930-041
41
O-ring
NBR
930-436
930-436
42
O-ring
NBR
930-169
930-169
43
Circuit board T.VIS P-15
--
221-005024A
221-005024A
48
Locking screw (not for T.VIS P-15/RM)
PA
922-370
508-370
50
Connector M12/ 5-pin/B-coded/M16/cpl. (only for T.VIS
P-15/RM)
PA
221-005822
221-005822
53
O-ring
NBR
930-833
930-833
54
O-ring
NBR
930-116
930-116
55
O-ring
NBR
930-038
930-038
57
Thread-forming screw
A2
514-750
514-750
63
Solenoid valve 3/2 way NC 24VDC
PBT
512-169
512-169
64
Solenoid valve 3/2 way NO 24VDC
PBT
512-168
512-168
65
Control plate without screws incl. seals
PPO
221-589.27
221-589.27
66
Thread-forming screw
A2
514-761
514-761
75
Throttle valve
Brass, nickel-
plated
603-042
603-042
77
Thread-forming screw
galv. steel
514-763
514-763
78
Adapter
PA 6
221-589.69
221-589.69
79
Locking screw
1.4404
922-316
922-316
Items marked with an * are not included in the control top subassemblies, item B!
Spare parts list - control top type T.VIS P-15
430BAL010747EN_3
24.07.2020
59
Содержание T.VIS P-15
Страница 65: ...Appendix 430BAL010747EN_3 24 07 2020 65...
Страница 66: ......