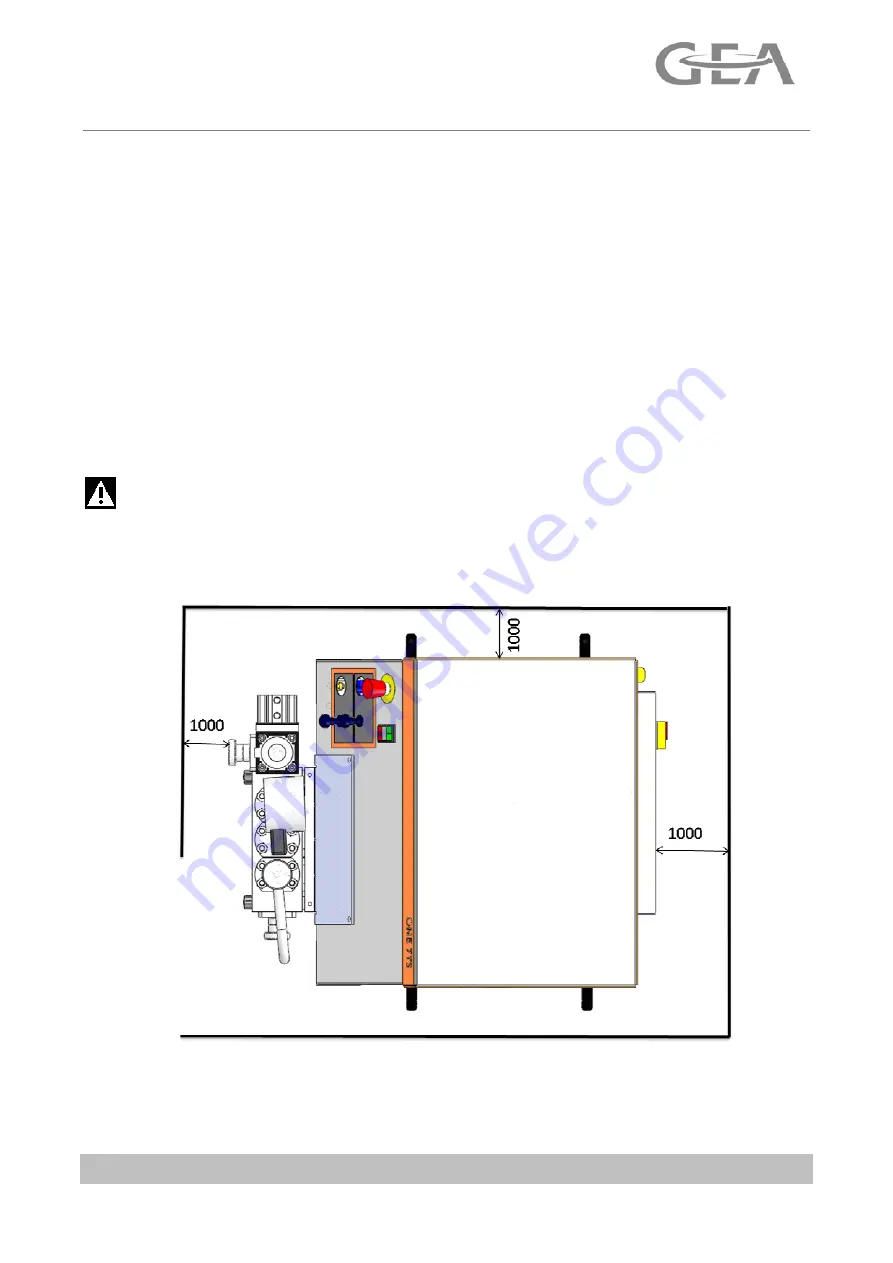
ONE 7TS – Installation
4.6.2 Positioning
Correct positioning of the machine in the customer’s production line will enable optimal operation and easy
access for ordinary maintenance procedures.
For this reason, considering its dimensions, it is important to keep a clear area around the machine for
maintenance activities, as shown in the figure below.
In particular, sufficient space should be allowed to enable replacement of the main motor using adequate
hoisting equipment (bridge crane, or forklift truck).
The front part and head require regular maintenance; you should leave enough space to enable complete
removal of the head.
The machine should also be installed away from heat sources which could affect the cooling process, and
ensure that no objects are obstructing the flow of air.
Water drainage must be provided to prevent flooding in the area where the machine is installed and prevent
water from entering through the ventilation openings.
ATTENTION:
The floor on which the machine is installed must support at least 150% its weight.
The weight is shown in the installation drawing enclosed in chapter 11 of this manual.
FIG. 4- 8
page
4.16
This manual is property of GEA Niro Soavi S.p.A. and no part of it may be reproduced.
Содержание ONE 11TS
Страница 2: ...GEA Niro Soavi S p A COVER02 DOC REV DESCRIPTION DATE SIGN 0 1 EDITION 05 07 2011 ANC ...
Страница 235: ......
Страница 245: ......
Страница 247: ......
Страница 255: ......
Страница 263: ......
Страница 264: ......
Страница 265: ......
Страница 266: ......
Страница 267: ......
Страница 268: ......
Страница 269: ......
Страница 270: ......
Страница 271: ......
Страница 272: ......
Страница 273: ......
Страница 274: ......
Страница 275: ......
Страница 276: ......
Страница 277: ......
Страница 278: ......
Страница 279: ......
Страница 280: ......
Страница 281: ......
Страница 282: ......
Страница 283: ......
Страница 284: ......
Страница 285: ......