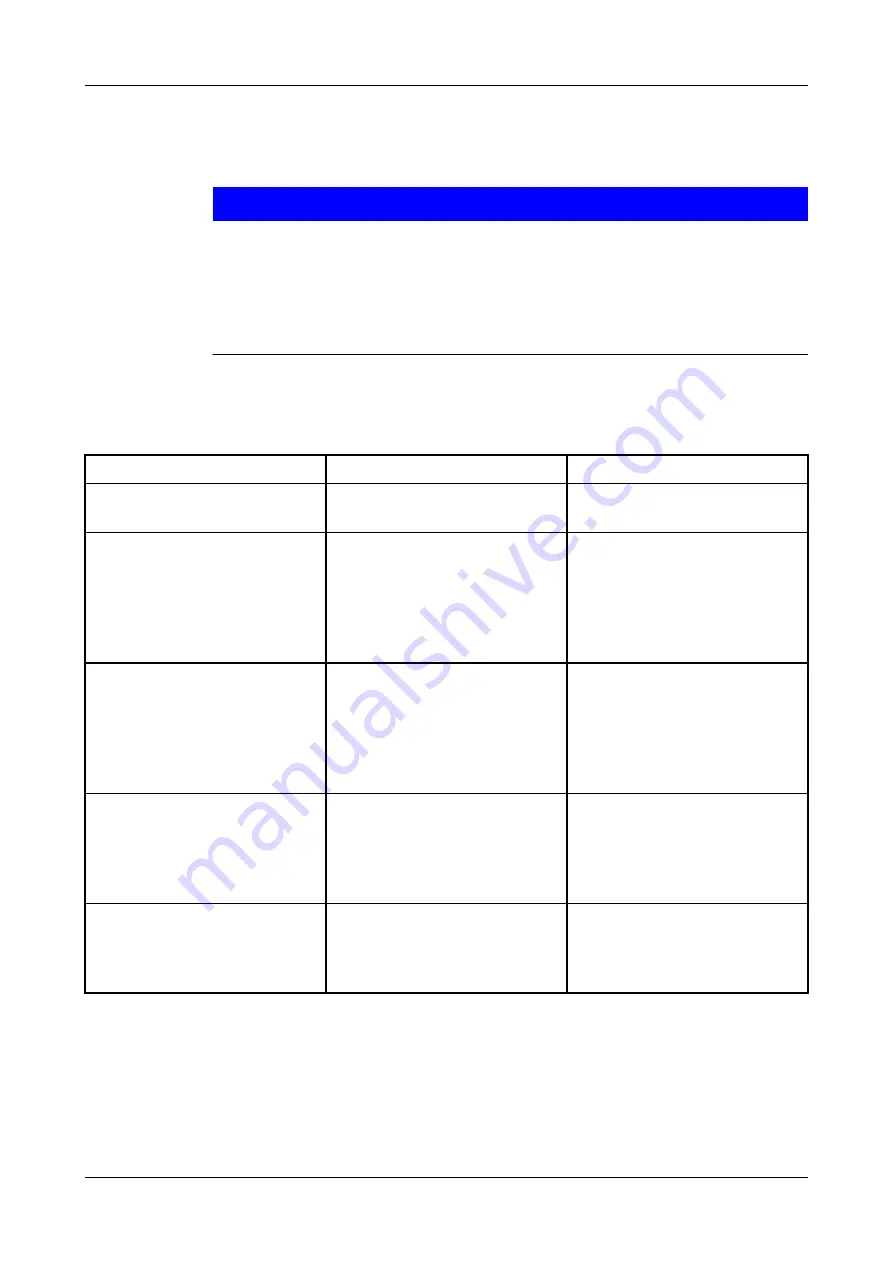
11
Alarms
11.1
Malfunctions and remedies
Notice!
Warning of damage to property/loss of product
Ignoring malfunctions may cause considerable damage to property and loss
of product. The safe operation of the valve in the event of a fault can no
longer be taken for granted and in the worst case can result in a loss of
sterility in the process.
► Make sure that malfunctions are quickly identified and promptly fixed.
In the event of malfunctions immediately deactivate the valve and secure it
against inadvertent reactivation. Malfunctions may only be remedied by qualified
staff, who must observe the safety instructions. For malfunctions not listed in the
table below, contact the manufacturer.
Malfunction
Cause
Remedy
Medium is leaking from the
clamp.
The housing seal is not fitted
correctly or damaged.
Fit the housing seal correctly
or replace it if damaged.
Medium is leaking from the
leakage holes of the internal
assembly.
The metal bellows on the
internal assembly is defective.
•
Replace the complete
internal assembly.
•
Send the defective internal
assembly to the
manufacturer for repair.
During pressure testing of the
internal assembly, air escapes
from the metal bellows.
The metal bellows on the
internal assembly is defective.
•
Replace the complete
internal assembly.
•
Send the defective internal
assembly to the
manufacturer for repair.
Leak at the valve seat.
•
The valve seat seal is
defective.
•
Product deposits on the
valve seat.
•
Replace the valve seat
seal.
•
Check the housing.
The maximum valve stroke is
not reached when the valve is
actuated pneumatically.
Leakage in the actuator.
•
Check the sealing surfaces
in the actuator for damage.
•
Replace the seals.
Alarms
Malfunctions and remedies
430BAL012727EN_1
60
03.01.2018
Содержание Aseptomag GD
Страница 65: ...Appendix 430BAL012727EN_1 03 01 2018 65...
Страница 66: ......