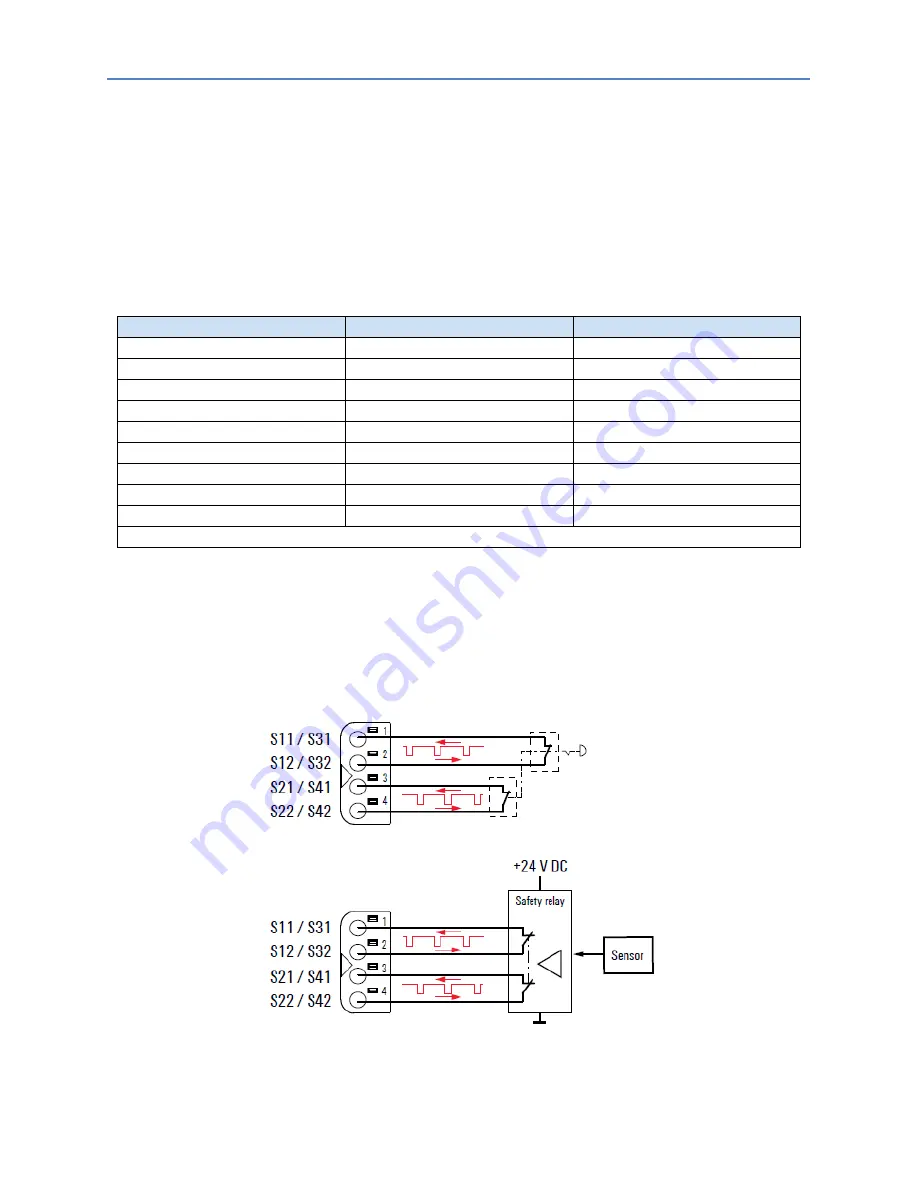
Chapter3
.
Configuration
GFK-2956A
November 2017
13
4.1
Switch-off Delay Time
The turn-off time of a EP-19xx module is 20 ms, caused by the hardware and firmware delay time.
The time required until the output voltage even of the last switchable module of a safety segment is
below 5 V, can be calculated as follows:
Switch off delay [ms] =
Turn-off time of a EP-19xx module
+ S
um of all modules’ hardware delay
Switch-off Delay and Current Consumption
Module
Hardware Delay (ms)
Current Consumption (mA)
EP-2214
2
8
EP-2614
2
8
EP-2634
3
15
EP-2218
1
15
EP-225F
1
10
EP-5422
5
10
EP-5442
5
10
EP-4164
150
†
10
EP-4264
150
†
10
†
The delay time is always 150 ms, irrespective of the amount of these modules.
4.2
Operation With and Without Test Pulses
All safe power-feed modules provide a test pulse evaluation, so that the highest safety levels can be
achieved (see technical data).
Example of Operation with Test Pulses
Содержание RSTi-EP
Страница 2: ......
Страница 76: ...1 800 433 2682 1 434 978 5100 www ge ip com GFK 2956A g ...