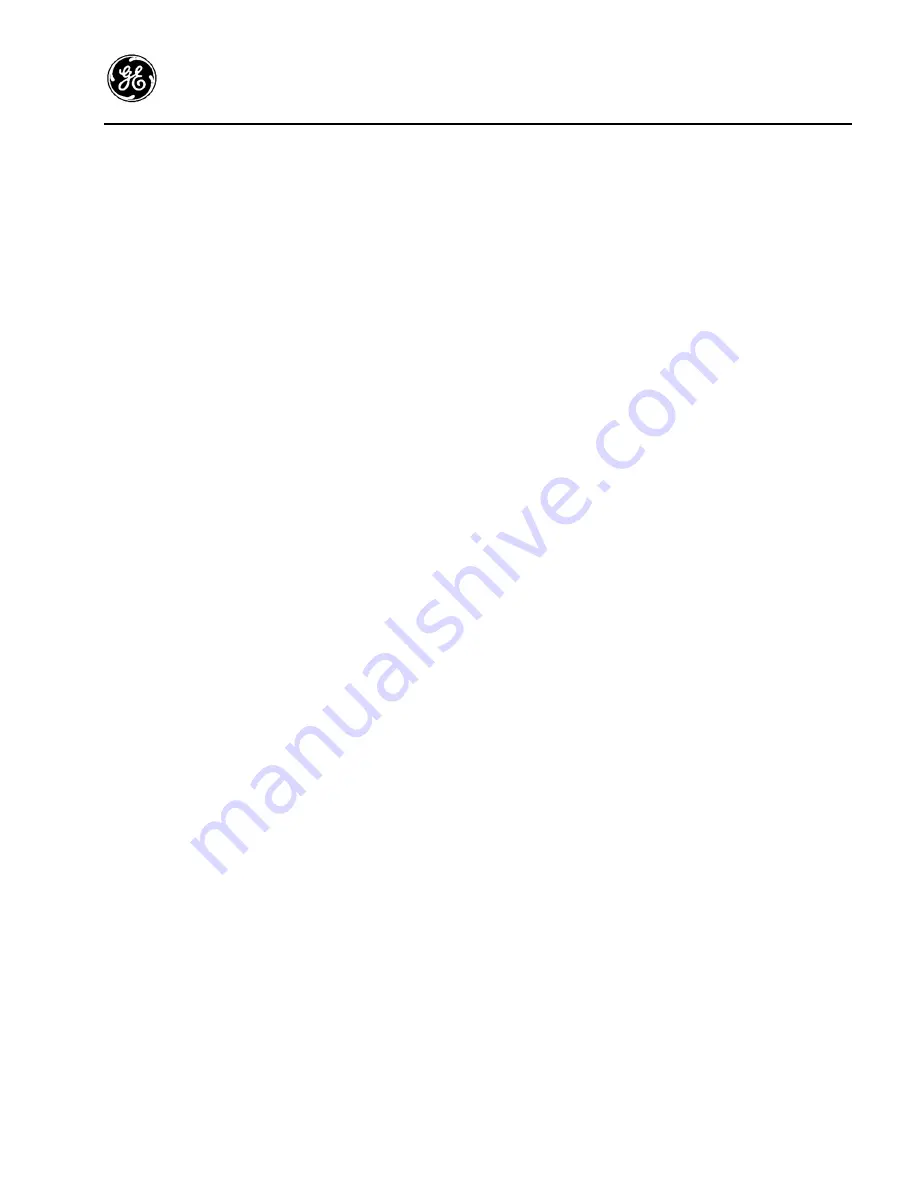
GE Industrial Control Systems GEEP-124-I Copyright 1997,1998 The General Electric Company, USA
23
GEEP-124-I Horizontal Induction Motor
WPI, Antifriction Bearing
Maintenance - Grease Recommendation
General
Bearings must carry the weight of the rotor;
normal magnetic forces between the rotor and stator; any
lateral belt pull; and still maintain the rotor in accurate
location relative to the stator bore. Accordingly, they
constitute a very important part of the unit and have
been selected to give long life on a unit which has been
correctly installed, aligned and maintained.
The antifriction bearings used on this unit are
grease lubricated. The grease consists of a lithium base
soap impregnated with a suitable lubricating oil. It is
placed in close proximity to the bearing and the oil seeps
out of the soap structure and lubricates the balls or
rollers as they move relative to the inner and outer race.
Although the amount of grease required to lubricate
antifriction bearings is not great, it is essential that
grease always be present, that the grease be of the
correct type and that it be clean and free of
contamination. The correct grease viscosity, specified in
SSU units at 100F, is given on the nameplate. The
antifriction bearings used are specified on the
nameplate.
Bearings should be lubricated once every six
months for normal, applications associated with
moderate to average environmental conditions of dirt,
moisture and heat. For more severe conditions of any
one or more of the above environmental conditions, the
lubrication frequency should be increased to every two
months.
To lubricate the bearings, first stop the unit and
remove voltage from all circuits. Remove the grease
plug, located on the outboard side of the end shield, at
the bottom of the bearing housing, and make certain that
the grease-relief hole is free of hardened grease. The
grease fitting is located at the end of the pipe below the
horizontal split. (on totally-enclosed, air-to-air cooled
machines the grease fittings are located on the side of
the external fan casing. The grease relief plug is
connected to a spiral rod which assists in purging grease
from the bearing cavity). Wipe the grease fitting clean.
Using a hand-operated grease gun, apply the
specified grease. Continue to apply grease until old
grease cases to purge from the grease-relief hole and it is
a apparent that new grease is purging. Make certain that
the purged grease is captured and removed from the side
area. Leave the grease-relief hole plug temporarily off.
Start the unit and operate for about 30 minutes. Any
excess grease will be expelled from the grease-relief
hole. Again, stop the unit and remove voltage from all
circuits. Then, replace the grease plug and remove the
excess grease which was just purged.
It is important that end shield vibration and
bearing noise be monitored.
Some conditions which can cause bearing failures
to occur are:
1.
Insufficient grease, or too much grease.
2.
Incorrect grease specification.
3.
Ambient temperature conditions either too
hot or too cold for the viscosity of the grease being used.
4.
Contaminated grease.
5.
Misalignment of unit and driven equipment
(in parallel, angular or axial misalignment).
6.
Seals too tight.
7.
Bearing operated longer than design life (L
10
130.000 hours for direct drive) (L
10
40.000 hours for
belted drive) will have an increased risk of failure.
If one or both bearings exhibit an increase in
vibration, noise or temperature, above the normal
operating conditions, the unit should be shut down and
the cause determined and corrected.
DLCGEEP-124-I/000, Approved, 2016-11-11, CampinasDM