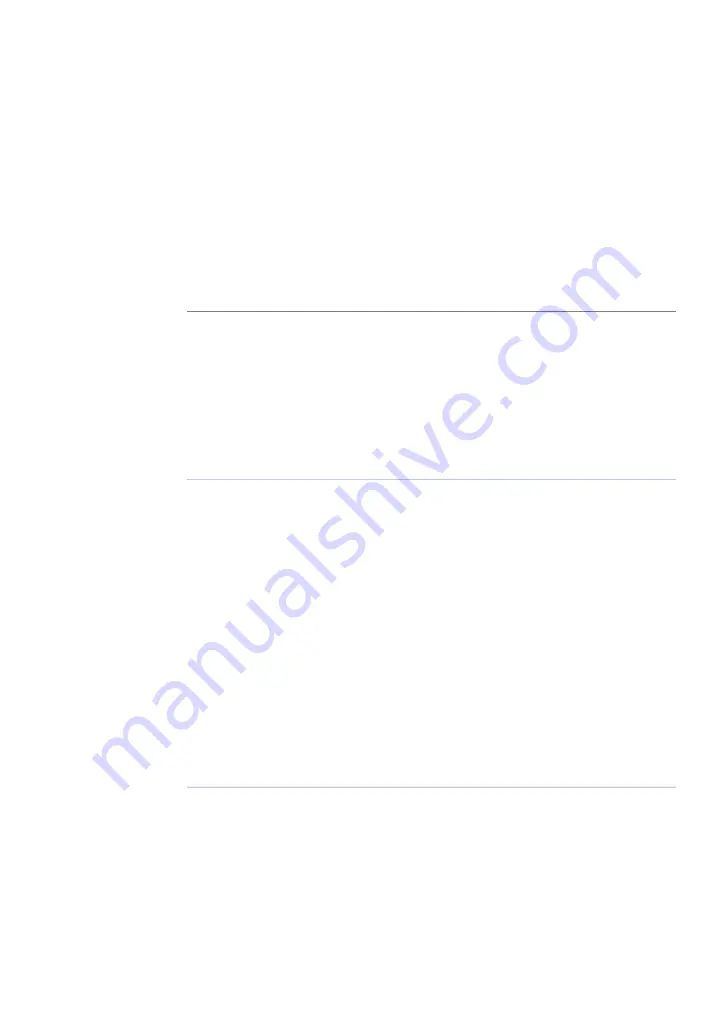
5.1.4
Set pressure control valve parameters
Introduction
After the priming and leakage test, and before a run is started, the pressure control valve
(PCV) or valves on the system need to be adjusted. The purpose of this adjustment is to
achieve correct flow through the system as a result of the feed pressure on the inlets.
This section describes procedures for pressure control valve adjustment and describes
how to set two other parameters for the PCV valves, (Hold backpressure and Boost).
PCV adjustment
Pressure control valve set up is performed using UNICORN functions to adjust the low
flow limit of the valve.
Follow the instructions in this section in the order presented below (start by adjusting
PCV-341 and then PCV-342 if your system has this option).
Action
Step
Start with opening the flow path (inlet needs to be pressurized).
1
Switch the PCV-341 valve positioner to manual mode.
2
Close the valve slowly, until no flow is detected by FT-141. The valve can be
operated manually through instruction PCV-341 valvepositioner.
3
Open the valve slowly until flow is detected by FT-141.
4
Close the valve slowly until no flow is detected by FT-141. The valve is opened
and closed once more for accuracy.
5
Take the percentage (%) value obtained in the step before and lower the
result by 4%.
6
Write the calculated result into the instruction PCV-341 valvepositioner.
7
Result: This value is the low limit of the valve.
Record the value in PCV-341 settings as the lower limit.
8
PCV-342 is set in the same way as described above, using pressure transmitter
PT-116 instead of PT-115.
Note:
ÄKTAprocess Operating Instructions 29-0252-49 AA
121
5 Operation
5.1 Prepare the system
5.1.4 Set pressure control valve parameters
Содержание AKTAprocess
Страница 1: ...GE Healthcare Life Sciences ÄKTAprocess Operating Instructions Original instructions ...
Страница 2: ......
Страница 179: ......