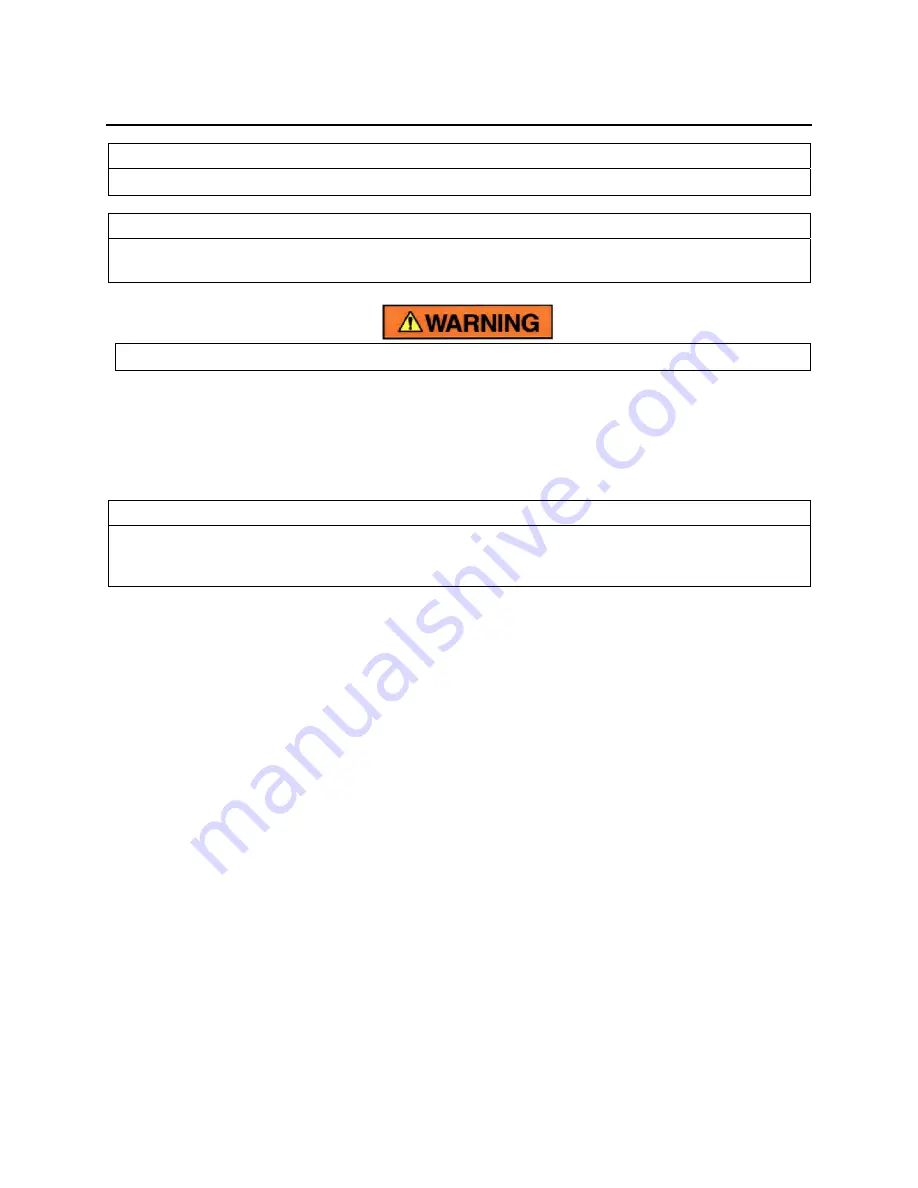
37-1-614 Page 40
SECTION 7
ASSEMBLY INSTRUCTIONS
NOTICE
The fastener & locknut torque values required during assembly are shown in
FIGURE 7-33
.
NOTICE
Illustrations for Assembly Instructions are taken from various sizes of Cycloblower minor
variations in construction of some parts should not cause concern.
Numbers in parentheses ( ) refer to key numbers in assembly drawings on pages 31 and 32.
The CycloBlower® is manufactured with close tolerances for efficient operation. All parts must be
handled carefully to prevent burrs which will give false clearance readings and/or cause rapid wear.
All parts and oil passages must be thoroughly cleaned of dirt which will cause galling of close running
parts. Clean work area, washing tank, tools and wiping rags must be provided.
Refer to Parts List, Section 5, page 31 and 32, for sectional views showing complete assembly of parts.
NOTICE
The following illustrations are of a standard blower with top inlet, bottom discharge, main rotor
discharge end drive, main rotor discharge end drive. Some variations will be noticed in the
following illustrations for blowers of other arrangements.
There may be cases where foreign materials have entered the blower, or other causes have resulted in
galling of the rotor ends, carrier faces, rotor lobes, or housing walls. Since the blower is designed with no
contact of parts within the rotor chambers, these parts may be cleaned and polished for reuse unless
galling is severe. Reuse of parts severely galled may result in loss of blower efficiency. All damaged
parts which have been reworked should be checked for run-out or warpage before reuse.
Assembly of the “P” Series CycloBlower differs from earlier models in the approach to installing the oil
seals. On previous models the installation of the lip seals into the bearing carriers was the first step in the
assembly process. This was acceptable for seals with compliant lips but the hydrodynamic lip seals are
made of Teflon and could be damaged by mishandling. On the “P” Series, the lip seals are not installed
into the bearing carriers until after the rotors have been assembled. This requires that the lip seal is
slipped over the rotor shaft so a hollow cylindrical pusher is needed as well as a short installation sleeve.
1. Oil the O.D. of the rotor shaft seals (18, 19) to prevent seizure and press into each bore of the
gear end bearing carrier (4) (FIGURE 7-1, page 41). NEVER REUSE SHAFT SEALS. Refer to
“Rotor Shaft Seals,” page 28, for an explanation. A simple press utilizing a bolt and two bars, one
across the seal and one underneath across the bearing bore, is an effective method for installing
the seal. Tightening the nut on bolt presses the seal into place. Press the seal .010” to .015”
below the face of the carrier to prevent the end of the rotor from rubbing the end of the seal. A
simple method is to place a .010” to .015” shim on the end of the seal under the press bar which
will allow the seal to be pressed the correct distance below the face of the carrier. Handle the
seal with care to prevent damage to babbitt lining.