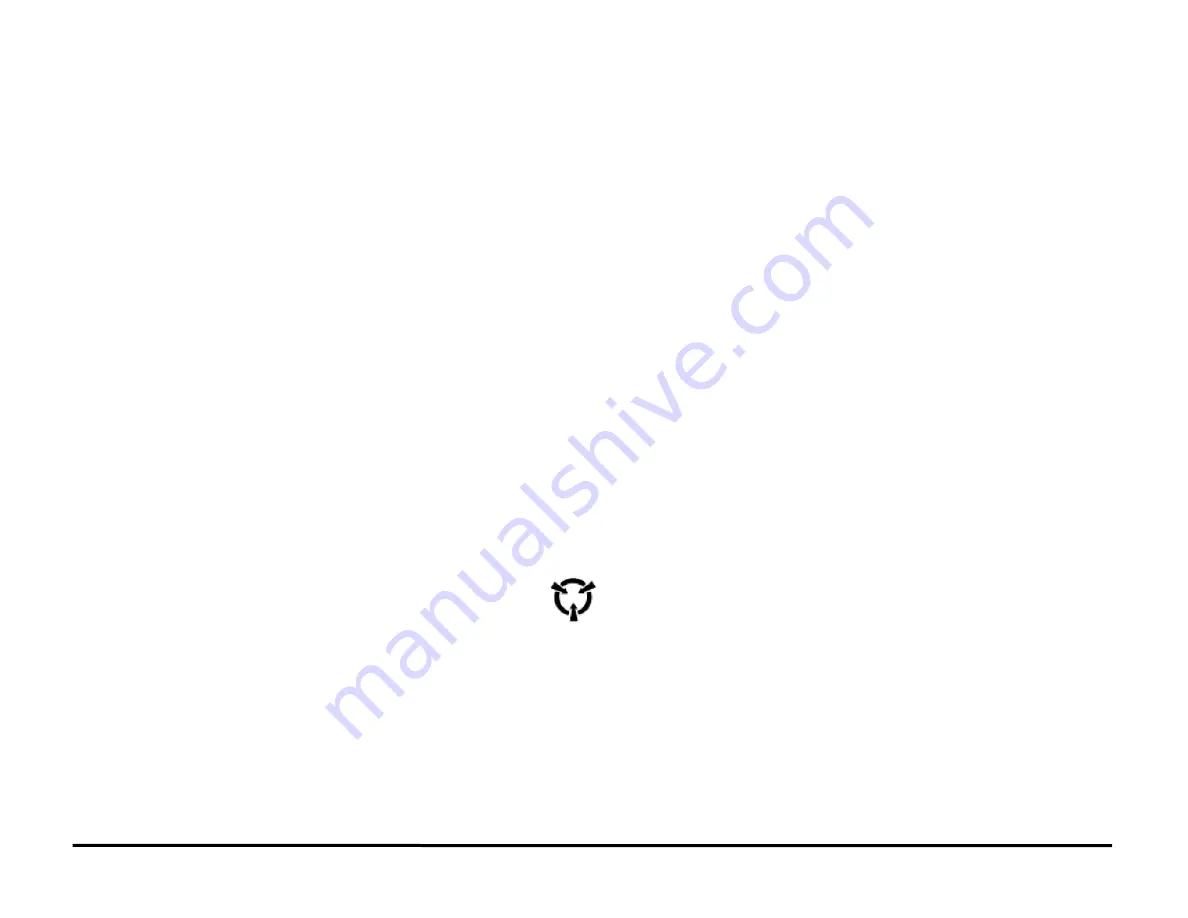
GBC AdvancedPunch Pro
11/07/2018
Service Manual
Part Number: 7718590
Revision Number: A1
Issue Date: November 2018
GBC AdvancedPunch Pro
Service Manual
CAUTION
Certain components in the GBC AdvancedPunch Pro are susceptible to
damage from electrostatic discharge. Observe all ESD procedures to
avoid component damage.
Содержание AdvancedPunch Pro
Страница 26: ...Service Call Procedures 08 20 2015 GBC AdvancedPunch Pro 1 8 Notes ...
Страница 28: ...GBC AdvancedPunch Pro 11 07 2018 RAPS 2 2 ...
Страница 78: ...Punch Quality 11 07 2018 GBC AdvancedPunch Pro 3 2 This page intentionally left blank ...
Страница 230: ...Repairs Adjustments 08 20 2015 GBC AdvancedPunch Pro 4 142 Notes ...
Страница 263: ...GBC AdvancedPunch Pro 09 11 2018 Parts List 5 33 PL 6 4 Wiring Drawing OEM Configurations ...
Страница 264: ...Parts List 09 11 2018 GBC AdvancedPunch Pro 5 34 PL 6 5 Wiring Drawing DFA Configurations ...
Страница 275: ...GBC AdvancedPunch Pro 09 11 2018 General Procedures and Information 6 5 User Interface Screen Map ...
Страница 297: ...GBC AdvancedPunch Pro 09 11 2018 General Procedures and Information 6 27 Service Interface Screen Map ...
Страница 359: ...GBC AdvancedPunch Pro 09 11 2018 General Procedures and Information 6 89 This page intentionally left blank ...
Страница 360: ...General Procedures and Information 09 11 2018 GBC AdvancedPunch Pro 6 90 Notes ...
Страница 362: ...Wiring Data 08 20 2015 GBC AdvancedPunch Pro 7 2 This page intentionally left blank ...
Страница 363: ...GBC AdvancedPunch Pro 08 20 2015 Wiring Data 7 3 System Wiring ...
Страница 364: ...Wiring Data 08 20 2015 GBC AdvancedPunch Pro 7 4 System Wiring DFA Configurations ...
Страница 365: ...GBC AdvancedPunch Pro 08 20 2015 Wiring Data 7 5 Plug Jack Connectors ...
Страница 366: ...Wiring Data 08 20 2015 GBC AdvancedPunch Pro 7 6 Plug Jack Connectors DFA Configurations ...
Страница 367: ...GBC AdvancedPunch Pro 08 20 2015 Wiring Data 7 7 Notes ...
Страница 368: ...GBC AdvancedPunch Pro 08 20 2015 Installation Instructions 8 1 8 Installation Instructions ...
Страница 369: ...Installation Instructions 08 20 2015 GBC AdvancedPunch Pro 8 2 ...
Страница 370: ...GBC AdvancedPunch Pro 08 20 2015 Installation Instructions 8 3 ...
Страница 371: ...Installation Instructions 08 20 2015 GBC AdvancedPunch Pro 8 4 ...
Страница 372: ...GBC AdvancedPunch Pro 08 20 2015 Installation Instructions 8 5 ...
Страница 373: ...Installation Instructions 08 20 2015 GBC AdvancedPunch Pro 8 6 ...
Страница 374: ...GBC AdvancedPunch Pro 08 20 2015 Installation Instructions 8 7 ...
Страница 375: ...Installation Instructions 08 20 2015 GBC AdvancedPunch Pro 8 8 ...
Страница 376: ...GBC AdvancedPunch Pro 08 20 2015 Installation Instructions 8 9 ...
Страница 377: ...Installation Instructions 08 20 2015 GBC AdvancedPunch Pro 8 10 ...
Страница 378: ...GBC AdvancedPunch Pro 08 20 2015 Installation Instructions 8 11 ...
Страница 379: ...Installation Instructions 08 20 2015 GBC AdvancedPunch Pro 8 12 ...
Страница 380: ...GBC AdvancedPunch Pro 08 20 2015 Installation Instructions 8 13 ...
Страница 381: ...Installation Instructions 08 20 2015 GBC AdvancedPunch Pro 8 14 ...
Страница 383: ...Installation Instructions DFA 08 20 2015 GBC AdvancedPunch Pro 8 2 This page intentionally left blank ...