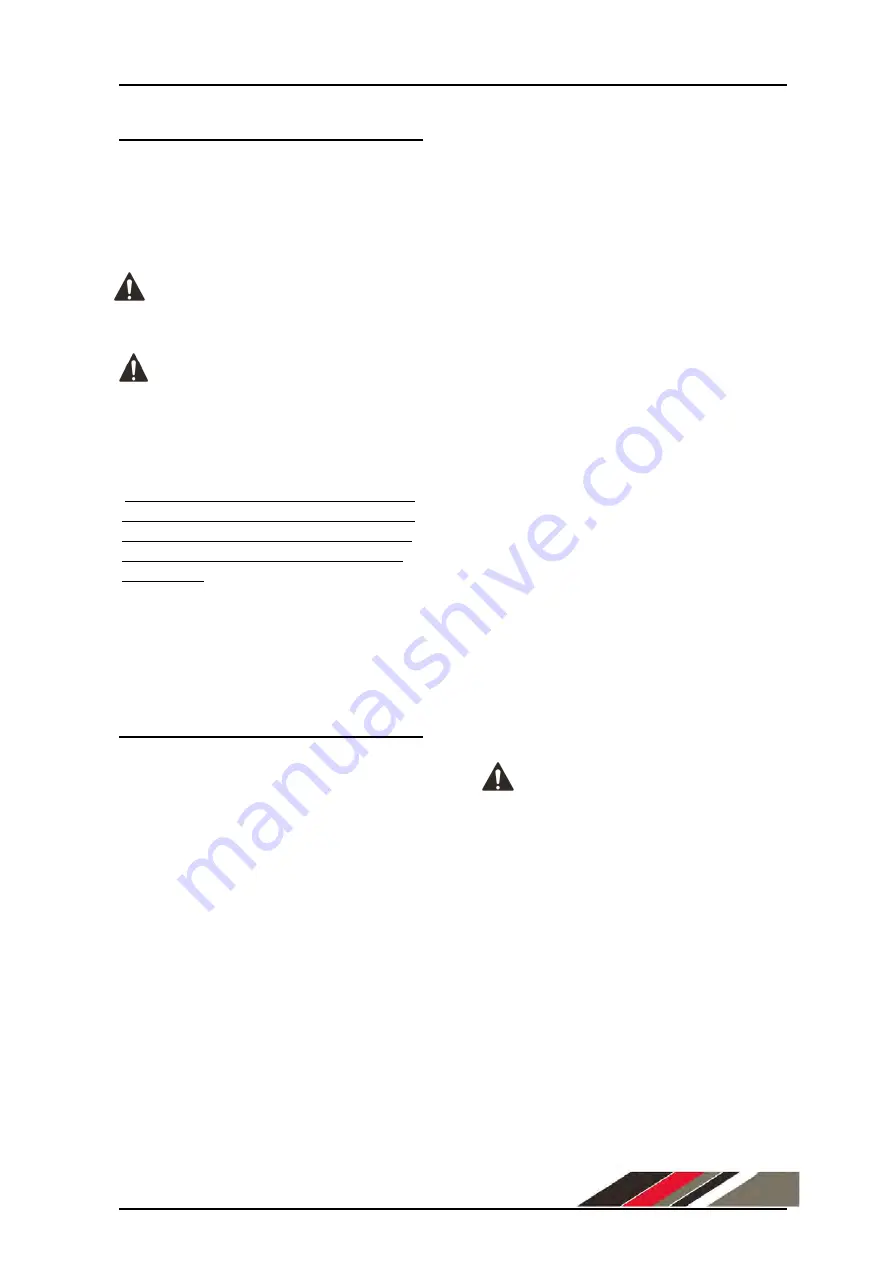
Unloading and Assembly
10
Unloading From Transport
Because of the compact nature of the
NT8000, most machines will be delivered as-
sembled ready to be towed off the truck. If
not assembled or unable to be towed off
machines must be lifted by approved over-
head lifting gear and licensed operators.
Warning: Only qualified personnel are
to be involved with the lifting of machine.
Bystanders must remain clear at all times.
Danger: Ensure that all lifting equip-
ment is in good condition and has the ca-
pacity to lift the load. Do not lift unless the
weight is known or a reasonable assumption
of weight is determined.
Note: Gason dispatch department measure
and record the load & other lift information
on a Crane Lift form*. A copy of this form is
given to the truck driver for use at the un-
loading end.
If lifting points are around the RHS frame
use soft slings. Avoid excessive paint dam-
age, if chains must be used, ensure paint-
work is protected.
Assembly
If the NT8000 is transported partially disas-
sembled, items that may require assembly
are as follows:
Fitment of wheels and tensioning to cor-
rect torque. Wheels may have been re-
moved depending on transport height
required.
Fitment of pull.
Fitment of tines / press wheels to the
marked position.
Shank Fitment.
Reconnection of hydraulic hoses, secur-
ing hoses in clamps and priming hydrau-
lic circuits.
Fitment of implement depth indicator.
Ground tool Fitment.
Touchup of paint work if required.
Wheel Fitment - If wheels have been re-
moved for transport, loosely mount wheels
on hubs. Be Gentle. Avoid damage to
threads. Tighten all nuts firmly then proceed
to torque each wheel nut to 350N.m. Alter-
nating sides across stud pattern when tight-
ening up nuts.
Fitting Pull – the pull may be removed for
transport. Using a crane, position & fit the
drawbar to the front of the centre frame us-
ing the bolts provided i.e. M20 Grade 8.8
bolts and Class 8 Nyloc nuts. Torque bolts to
335 N.m. Lower the jack to support the
front of the drawbar and fit safety tow
chain.
Tine Fitment - Tine location decals (arrows)
should be fitted to the toolbar to indicate
the tine locations for tines/row units not fit-
ted or not fitted in the correct location.
Upon fitment, ensure the correct hardware
is used i.e. M20 Grade 8.8 bolts and Class 8
Nyloc nuts. Secure the four fasteners in
stages to pull up the tine evenly and
squarely onto the toolbar.
Caution: Assembly torque settings
are critical to ensure tine assemblies remain
secure to the toolbar at all times. Torque to
335 N.m. Confirm this setting with a good
quality torque wrench.
Shank Fitment - Fully raise implement, fit
the tine shanks to the upper tine assem-
blies. Ensure positioning pins are in the
same hole in both the shank and the pivot
bracket to the tine tower. Ensure the rear
M20 set screws are tightened up hard
against the shank and the locking nut is then
tightened.
Содержание NT8000
Страница 30: ...26 ...
Страница 31: ...27 Spare Parts SNT8000 HNT8000 Models ...
Страница 32: ...Spare Parts 28 ScariTILL Spring Tine Assembly ...
Страница 34: ...Spare Parts 30 HydraTILL Hydraulic Tine Assembly ...
Страница 38: ...Spare Parts 34 NT8000 Assembly ...
Страница 40: ...Spare Parts 36 Centre Frame Assembly ...
Страница 42: ...Spare Parts 38 Left Wing Assembly ...
Страница 44: ...Spare Parts 40 Right Wing Assembly ...
Страница 52: ...Spare Parts 48 Hydraulic System Wing Fold ...
Страница 54: ...Spare Parts 50 Hydraulic System Depth Control ...
Страница 58: ...Spare Parts 54 HydraTILL Plumb Kit 250mm Spacing ...
Страница 60: ...LAYOUTS 56 Layout 178mm Spacing 45 Tines ...
Страница 61: ...LAYOUTS 57 Layout 250mm Spacing 32 Tines Optional Presswheels Shown ...
Страница 62: ...LAYOUTS 58 Layout 308mm Spacing 26 Tines Optional Presswheels Shown ...
Страница 63: ...59 ...