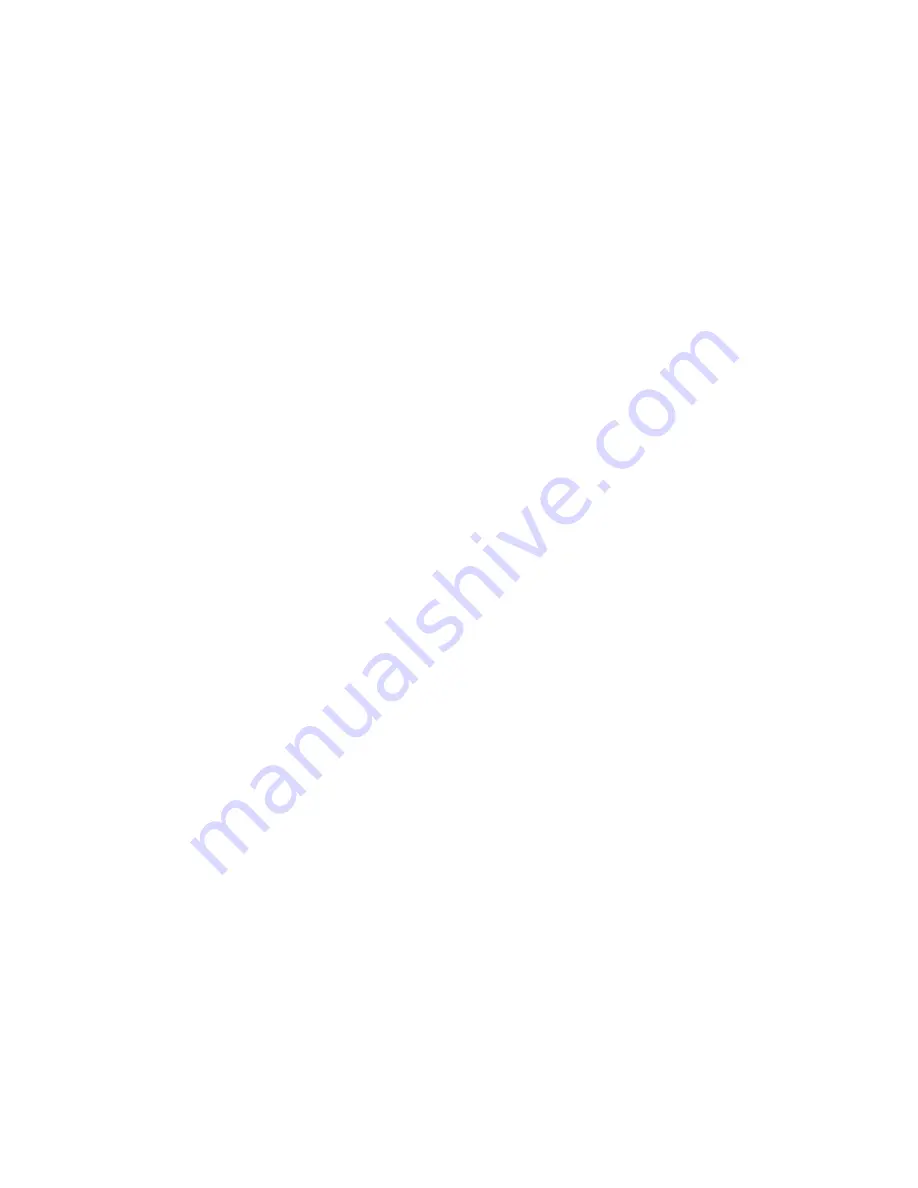
IOM GMI 2M & 2ML Nov 2010.doc
9
VI:
Gas Pressure Switches:
One Honeywell manual reset low gas pressure switch is
installed on the gas train in between the gas pressure regulator and the first safety
shut off valve (please see the schematic diagram “Typical UL Schematic Gas
Piping” on page 9 of the Riello catalogue). If the line pressure drops below 8” wc,
the switch will open and the unit will immediately shut down. One Dungs high gas
pressure switch is also installed on the side of the Riello burner (for exact location
please see item #4 on the drawing presented on page 4 of the Riello catalogue). If
the gas manifold pressure increases above 3.65” wc, the switch will open and the
unit will immediately shut down.
1.4
Gas Lines
1.4.1 Pilot Gas Line
Referring to the “Typical UL Schematic Gas Piping” diagram on page 9 of the Riello catalogue,
gas from the main supply line flows at the maximum pressure of 14” wc through the manual valve
into the pilot line. From the pressure regulator it will then flow through the
two safety shut off
valves into the burner. The pressure regulator is adjusted such that gas flows within 2” – 5” wc
pressure into the first safety shut off valve. If pilot flame is not established within 5 seconds of the
ignition trial time, the flame safeguard will shut off the pilot safety gas valves.
The pilot flame will ignite the air/gas mixture flowing through the burner within 5 seconds of the
mixture flowing into the burner.
1.4.2 Main Gas Line
Referring to the same drawing, gas from the main supply line flows at a maximum pressure of 14”
wc through the manual gas valve into the main gas line. From the pressure regulator it will then
flow through the two safety shut off valves, into the second manual shut off valve. Finally gas
flows through the gas adjustment butterfly valve into the burner where it is ignited by the pilot
flame. The pressure regulator is adjusted such that the manifold gas pressure remains within 0.2 –
3.0” wc. This pressure is tested at the manifold gas pressure test point located on the side of the
Riello burner (for exact location of the test point please see item #8 on the drawing presented on
page 4 of Riello catalogue). Signals from the temperature controller are sent to the servomotor,
which controls the opening of the butterfly valve and the air damper. Subsequently, the valve and
damper are proportionately closed or opened in order to decrease or increase the air/gas mixture
flow into the burner. Hence, maintaining the outlet water at constant temperature, during changes
in the load/demand (i.e. throttle or load tracking function).
Содержание GMI 2M
Страница 6: ...IOM GMI 2M 2ML Nov 2010 doc 6 SECTION 1 INTRODUCTION...
Страница 13: ...IOM GMI 2M 2ML Nov 2010 doc 13 SECTION 2 INSTALLATION...
Страница 22: ...IOM GMI 2M 2ML Nov 2010 doc 22 SECTION 3 OPERATION...
Страница 30: ...IOM GMI 2M 2ML Nov 2010 doc 30 SECTION 4 MAINTENANCE...
Страница 34: ...IOM GMI 2M 2ML Nov 2010 doc 34...
Страница 35: ...IOM GMI 2M 2ML Nov 2010 doc 35 START UP REPORT...