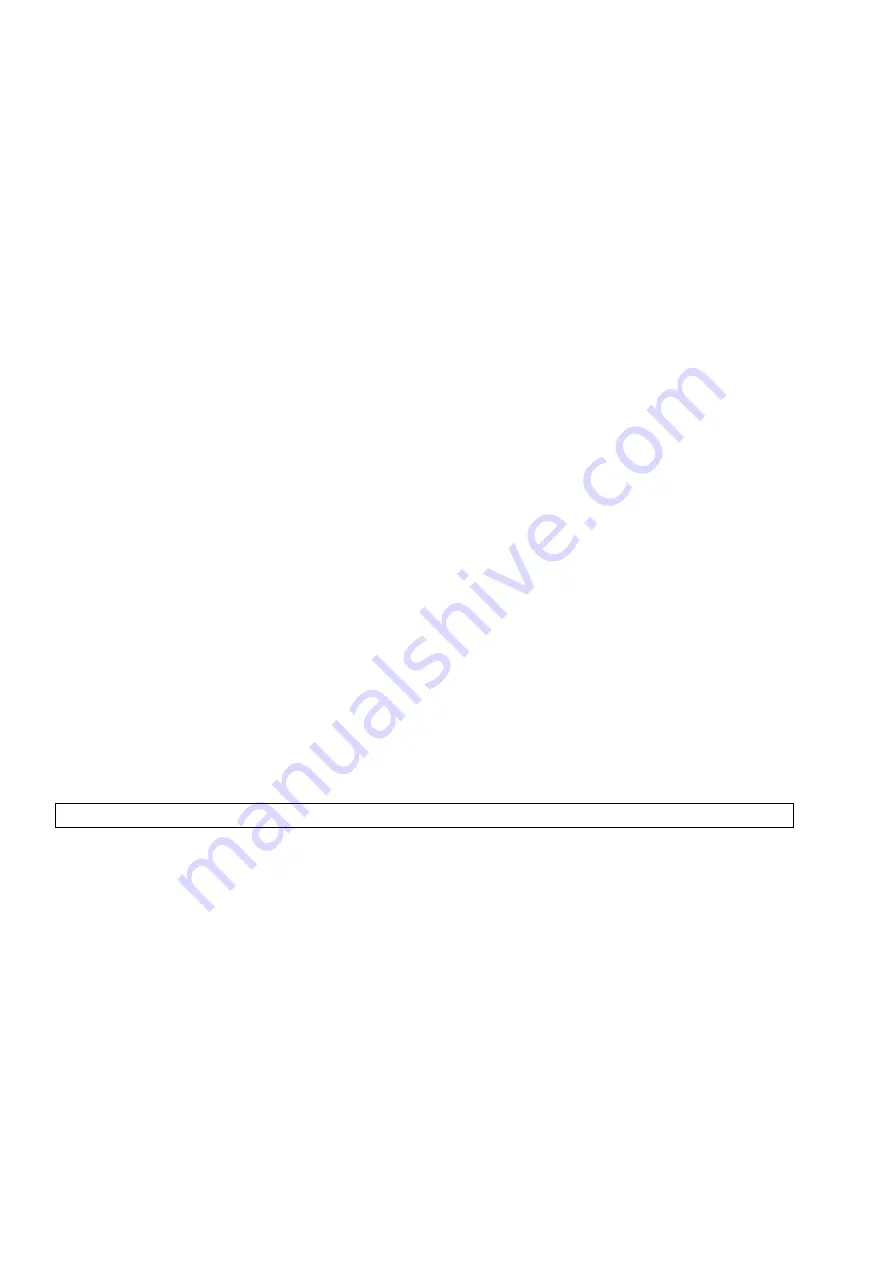
SAFETY
PAGE 12
If Viton seals appear charred or gummy do not touch with unprotected hands: wear neoprene or PVC
gloves.
When the seal has been removed, wash the area with limewater and avoid breathing any fumes. If
contamination of the skin occurs, wash with limewater and seek medical advice.
Always clean oil spills from the compressor module before and after maintenance work
NEVER USE A LIGHT SOURCE WITH AN OPEN FLAME FOR INSPECTION
Pressure gauges, temperature switches and other protection devices should be checked at least every
12 months and thoroughly examined at least every 48 months. They must be renewed or service
exchanged if acceptable tolerances are exceeded or if they are not functioning correctly.
The maximum pressure for safety valves under fault conditions is 1.10 times the set pressure, the set
pressure being a minimum of 1.05 times the maximum operating pressure to ensure seat tightness.
Do not use any flammable liquid to clean valves, filter elements, cooler passages, pipes bores or any
component carrying a flow of air or gas during normal operation. If chlorinated hydrocarbon substances
are used for cleaning, safety precautions must be taken against toxic vapours which may be released.
DO NOT USE CARBON TETRACHLORIDE.
Precautions must be taken against using acids, alkalis and chemical detergents for cleaning machined
parts. These materials cause irritation and are corrosive to the skin, eyes nose and throat.
Avoid splashes and wear suitable protective clothing and safety glasses. Do not breathe mists. Ensure
clean water and soap is readily available.
Protect components and exposed openings by covering with clean cloths or tape during repair or
maintenance work.
Protect all items as necessary against the ingress of moisture if steam cleaning is undertaken.
Precautions must be taken when carrying out any hot working. The adjacent components must be
screened with non-flammable material and if oil is present, the area must be first cleansed thoroughly
by steam cleaning.
1.7.7
PRECAUTIONS IN THE EVENT OF FIRE WITHIN THE COMPRESSOR
Use extreme caution when handling components that have been subjected to fire or very high
temperature. Some components may contain fluoroelastomer materials which decompose under these
conditions to form highly corrosive residues. Skin contact can cause painful and penetrating burns
resulting in permanent skin and tissue damage.
1.8 PURGING INSTRUCTIONS FOR GAS INSTALLATIONS
BEFORE ANY ATTEMPT IS MADE TO RUN THE COMPRESSOR ON PROCESS GAS, THE
OPERATOR MUST BE SATISFIED THAT THE COMPRESSOR AND ITS ASSOCIATED PIPEWORK
IS PURGED FREE OF AIR AND THAT THEY ARE FULLY CONVERSANT WITH THE OPERATING
PROCEDURES OF THE EQUIPMENT.
If in any doubt as to efficiency of the purging, ALWAYS REPEAT THE PROCEDURE.
1.8.1
PURGING
When the gas being compressed is flammable, or its purity is important, it must be a plant requirement
to purge the compressor to remove any air in it before letting the process gas into the system. The
compressor should be purged free of air, in accordance with purging procedures which apply to the
whole plant using the inert gas specified, after the compressor has been commissioned on air and
before the process gas is introduced into the system.
Содержание Reavell H5000 Series
Страница 2: ......
Страница 18: ...SAFETY PAGE 16...
Страница 20: ...AMENDMENTS PAGE 18...
Страница 22: ...COMPRESSOR LOG SHEET PAGE 20 REMARKS DATE REMARKS DATE...
Страница 24: ...GENERAL DESCRIPTION AND OPERATION PAGE 22 4 6 LUBRICATION SCHEMATIC FLOW DIAGRAM...
Страница 26: ...GENERAL DESCRIPTION AND OPERATION PAGE 24...
Страница 36: ...OPERATION AND ROUTINE MAINTENANCE PAGE 34...
Страница 44: ...DISMANTLING AND REASSEMBLY OF VALVES PAGE 42...
Страница 50: ...FAULT GUIDE PAGE 48...
Страница 68: ...PARTS LIST PAGE 66 80 89 EXTERNAL COMPONENTS 83 4 84 1 83 5 83 6 83 3 83 2 83 1 4 2 81 1 3 4 82 4 2 1 3 4...
Страница 72: ...PARTS LIST PAGE 70 93 95 1ST STAGE CONCENTRIC VALVE 9 8 6 5 4 2 1 3...
Страница 74: ...PARTS LIST PAGE 72 96 97 2ND STAGE CONCENTRIC VALVE 2 1 3 4 5 6 5...
Страница 80: ...PARTS LIST PAGE 78...
Страница 92: ...ANCILLARY PARTS PAGE 90...
Страница 94: ...STANDARD WIRING TERMINAL NUMBERS PAGE 92...
Страница 95: ......