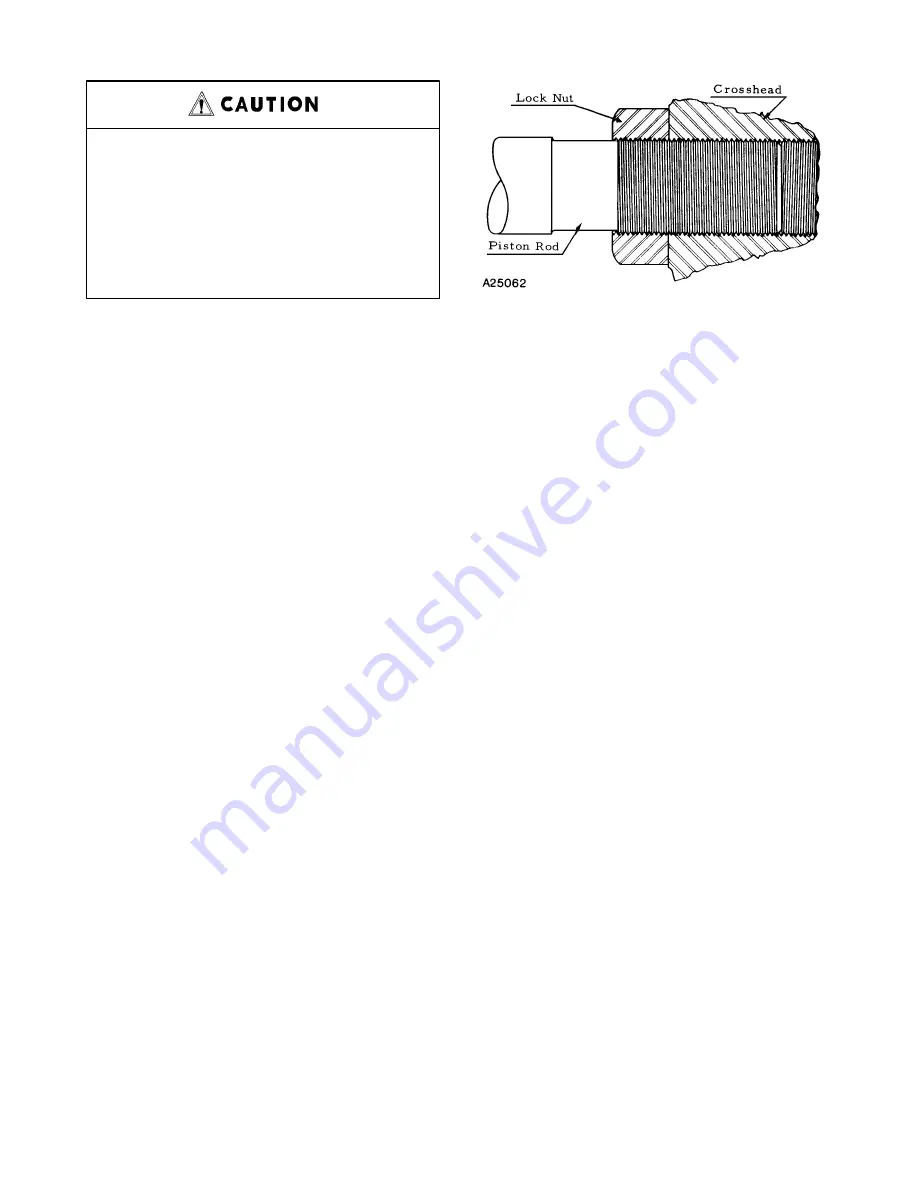
3–600 Page 10
Never tighten liner jack screws while
pump is running. If the screws are
drawn up too tight, enough pressure
can be put on the packing to crush the
liner. This ruins the liner, is apt to ruin
the piston and can cause piston rod
breakage.
Whenever the cylinder head is removed for any reason,
the liner jack screws must be backed out. Jack screws
should be greased to increase life of screws and cylin-
der heads and also to prevent rust formation.
When the cylinder head is replaced, the head to cylin-
der stud nuts should be tightened completely. AFTER
the head nuts are tight, the liner jack screws should be
adjusted against the liners and the locknuts tightened.
Be sure packing is installed under set screw nuts to pre-
vent leakage
Some pumps are equipped with a clamp located
against the end of the liner and serves as a face for the
set screws to bear against. For the proper tightening
torques refer to torque table, page 18.
FLUID END PARTS – Standard procedure for shipping
pumps from the Factory is with valves, pistons, liners,
piston rods and packing installed. These fluid end ex-
pendable parts are shipped unassembled only when
requested by the customer.
FLUID CYLINDER LINERS – Liners should be
installed in accordance with instructions given under
heading ”Fluid Cylinder Liner Packing”, page 9. Clean
liners thoroughly and grease the outside diameter be-
fore installing. Liner jack screws should be tightened as
uniformly as possible.
PISTON RODS – Pistons should be assembled on the
rod taper WITH THE THIN NUT NEXT TO THE PIS-
TON HUB AND THE THICK NUT ON THE OUTSIDE.
This is important as the outer nut carries the load. Slush
service rods use one elastic collar–type locknut per
rod. Rods should be threaded into the crosshead as
shown in FIGURE 6, leaving approximately one thread
of the locknut over the relieved portion of the rod as a
protection to the threads.
FLUID VALVES – Valves are easily installed in their in-
dividual valve pots. Care should be exercised to tighten
the valve cover nuts as uniformly as possible, tighten-
ing each nut a little at a time until all are tight. Valve
FIGURE 6 – PISTON ROD
seats and the bore in the deck must be perfectly clean
and free from oil or grease.
Valve seats can be removed with a puller which can be
purchased from Gardner Denver Machinery Inc.
STARTING A NEW PUMP – Pumps are shipped from
the factory without oil in the crankcase. The hood
should be removed and the power end examined and
cleaned if necessary. The pump may have been in stor-
age or in the yard for some time and as a consequence
dirt may have entered the crankcase. Parts may have
been robbed from the pump during storage and not re-
placed. All nuts and screws should be tightened.
The jackshaft bearings have been supplied with grease
at the factory and no grease should be added at this
time, unless bearings have been disturbed.
Be sure all valves in the discharge line are open. No
valve should be installed between the pump and pres-
sure relief valve in discharge line.
To prevent excessive wear on the fluid pistons and
packing when starting, remove a suction valve cover
plate on each side of the fluid end and prime the pump.
Pump should be started slowly, if possible, and should
be operated for several hours with practically no dis-
charge pressure. Check oil level as it may be neces-
sary to add a small quantity of oil to compensate for that
adhering to the walls of the crankcase and the moving
parts. The pump may then gradually be brought up to
full speed and full working pressure. Watch for undue
heating or abnormal noise in the working parts. Check
all joints in the suction line to be sure there are no air
leaks.
Make certain pump is rotating in the correct direction.
Refer to FIGURE 7, page 11.
Содержание FXF - 5"
Страница 17: ...3 600 Page 11 FIGURE 7 ROTATION OF ECCENTRIC PREFERRED ROTATION OF ECCENTRIC...
Страница 27: ......