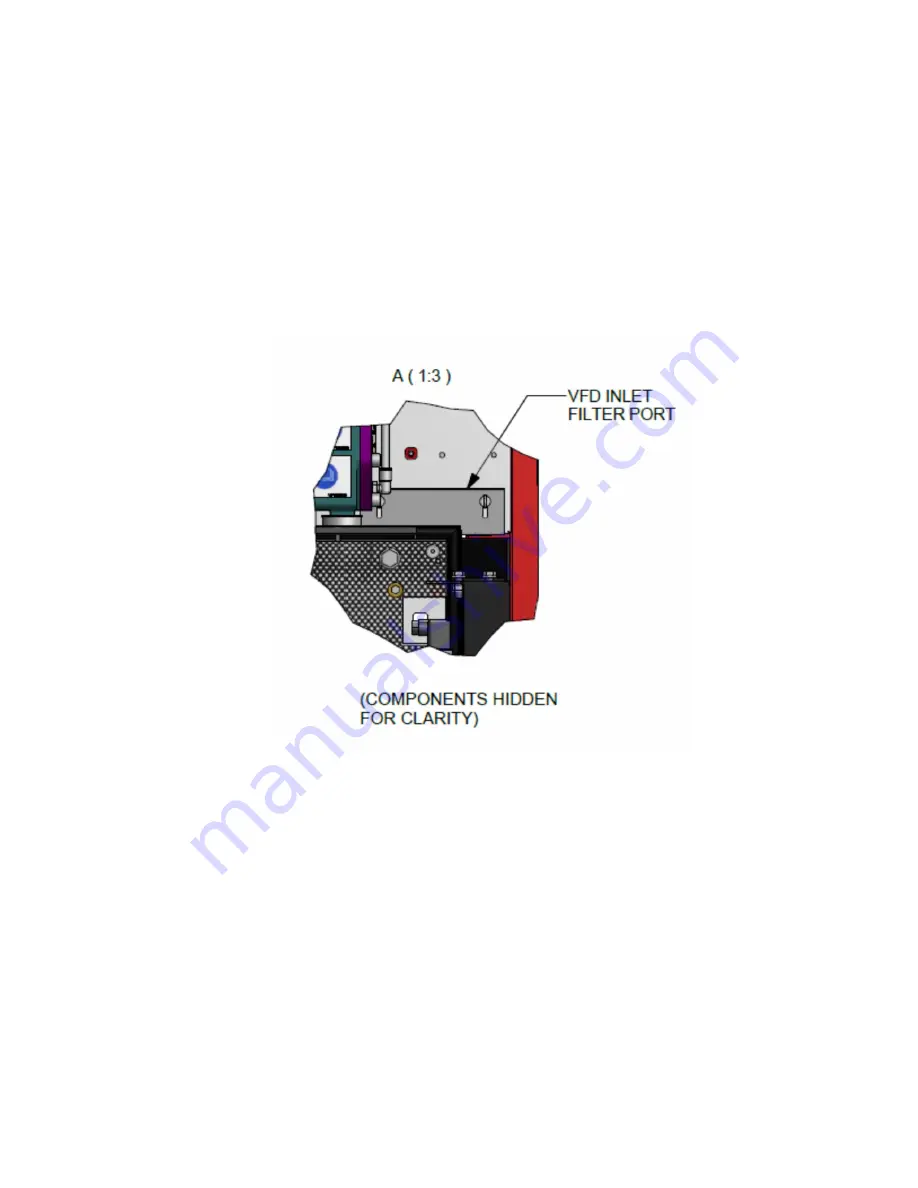
13-25-607 Page 49
VFD VENTILATION FILTER INSPECTION / REPLACEMENT
1. Locate the VFD filter access cover on the bottom, right hand side of the electrical enclosure, as
viewed from the rear with the bi-fold panels open.
2. Loosen the two (2) slotted screws holding the cover in place. Slide the cover upwards to uncover
the air filter edge.
3. Grab the outer edge of the air filter assembly and remove by pulling outwards.
4. If fouling is evident, cleanse the filter media gently with water - do not remove from the aluminum
frame.
5. Replace the filter media in its slot and replace the cover in the reverse order.
Figure 7- 3
Содержание APEX15-18A
Страница 2: ......
Страница 11: ...13 25 607 Page 9 Figure 1 2 COMPRESSOR ILLUSTRATION EXTERNAL DETAILS 300UCC804 C Ref Drawing Page 1 of 1...
Страница 12: ...13 25 607 Page 10 Figure 1 3 COMPRESSOR ILLUSTRATION INTERNAL DETAILS 300UCC797 B Ref Drawing Page 2 of 2...
Страница 13: ...13 25 607 Page 11 Figure 1 4 COMPRESSOR ILLUSTRATION TOTAL SYSTEM 307UCC804 B Ref Drawing Page 1 of 1...
Страница 27: ...13 25 607 Page 25 Figure 4 2 WIRING DIAGRAM VS 200 460 VOLT 306UCC546 A Ref Drawing Page 1 of 4...
Страница 28: ...13 25 607 Page 26 Figure 4 3 WIRING DIAGRAM VS 200 460 VOLT 306UCC546 A Ref Drawing Page 2 of 4...
Страница 29: ...13 25 607 Page 27 Figure 4 4 WIRING DIAGRAM VS 200 460 VOLT 306UCC546 A Ref Drawing Page 3 of 4...
Страница 30: ...13 25 607 Page 28 Figure 4 5 WIRING DIAGRAM VS 200 460 VOLT 306UCC546 A Ref Drawing Page 4 of 4...
Страница 31: ...13 25 607 Page 29 Figure 4 6 WIRING DIAGRAM VS 575 VOLT 307UCC546 A Ref Drawing Page 1 of 4...
Страница 32: ...13 25 607 Page 30 Figure 4 7 WIRING DIAGRAM VS 575 VOLT 307UCC546 A Ref Drawing Page 2 of 4...
Страница 33: ...13 25 607 Page 31 Figure 4 8 WIRING DIAGRAM VS 575 VOLT 307UCC546 A Ref Drawing Page 3 of 4...
Страница 34: ...13 25 607 Page 32 Figure 4 9 WIRING DIAGRAM VS 575 VOLT 307UCC546 A Ref Drawing Page 4 of 4...
Страница 37: ...13 25 607 Page 35 Figure 4 10 PIPING AND INSTRUMENTATION ILLUSTRATION 301UCC797 F Ref Drawing...
Страница 60: ...13 25 607 Page 58 Figure 9 6 Compressor Module Hardware 308UCC810 C Ref Drawing Page 1 of 1...
Страница 69: ......