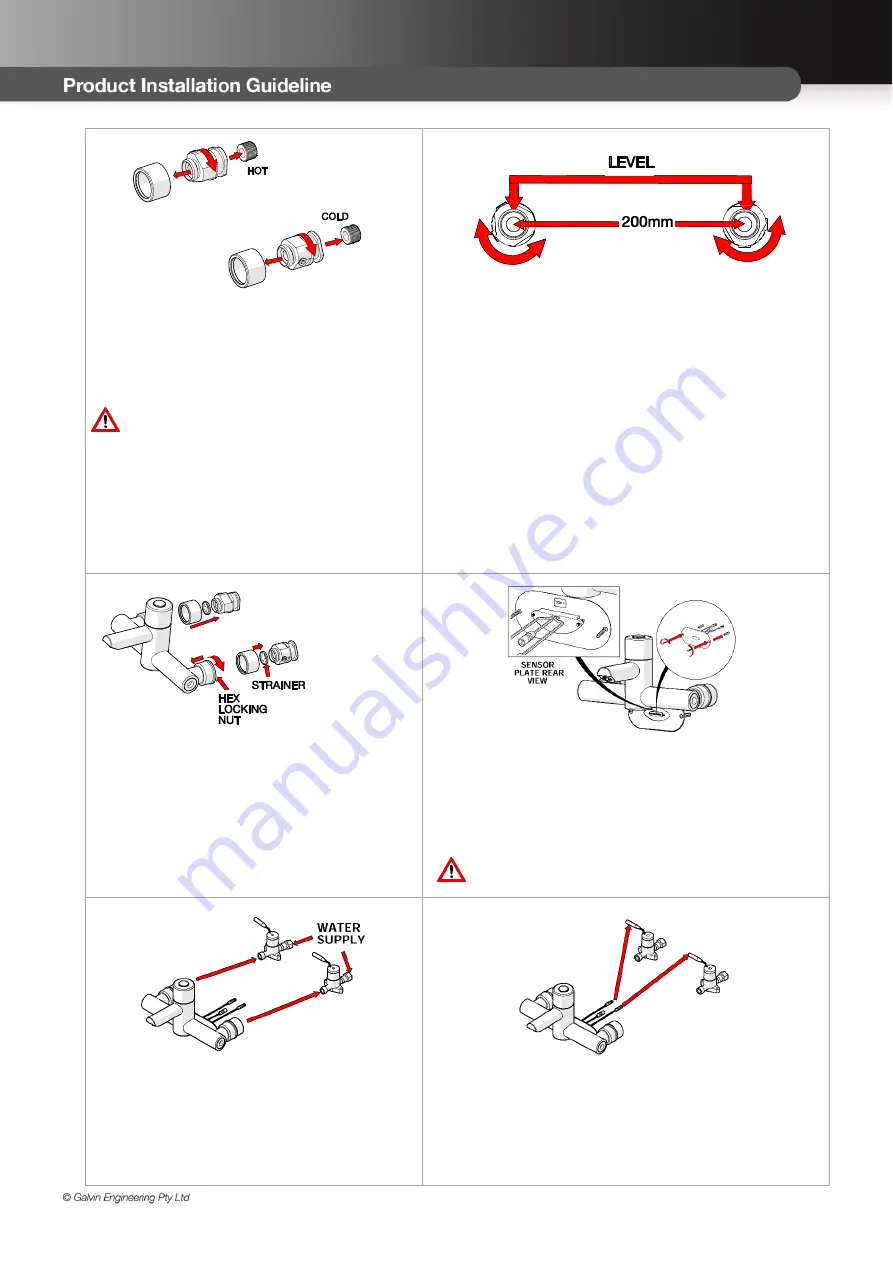
5
Version 1, 21 August 2019, 5 of 21
1. Fit isolator connector
−
Ensure /2” male hot and cold water
supply outlets are positioned as per
mounting details (section 4.0) at the
desired height and location above the
basin/sink.
Note: Hot supply should be on the left
when facing the wall
Remove both isolator connectors from
box.
−
Remove chromed sleeve from the
connectors
−
Apply thread tape to the male threaded
outlets and fit the isolator connectors.
2. Adjust the connectors
−
The isolator connectors are offset to p/-
15mm of rotational adjustment.
−
With the use of a spirit level and tape measure, you
are required to
▪
Position the back of the bases within 3mm of
the finished wall and;
▪
Ensure the bases are level and;
▪
Achieve 200mm centre to centre of the
connectors
Note: The use of thread tape is recommended to
ensure bases stay in the required position and are
water tight.
3. Fit progressive mixer
−
Fit chrome sleeves to fitted isolator
connectors.
Tighten loose nuts on the body to the isolator
connectors already on the wall ensuring the
strainer seal is in between. Do not over
tighten.
4. Secure Sensor
−
Install the proximity sensor to the wall
−
Ensure correct orientation of the sensor, It is
critical (see back of the face plate for orientation
arrow)
Do not remove the black label in front of sensor
faceplate until the tap is to be commissioned.
5. Fit solenoids
−
Connect solenoids to the tap and mains
water line
Ensure water is connected to correct inlet as
marked on tap.
6. Connect solenoids
−
Connect the solenoids to the sensor.
The unit supplied with a 3 x 3.2metre extension leads for
connecting to transformer, solenoid, and sensor.