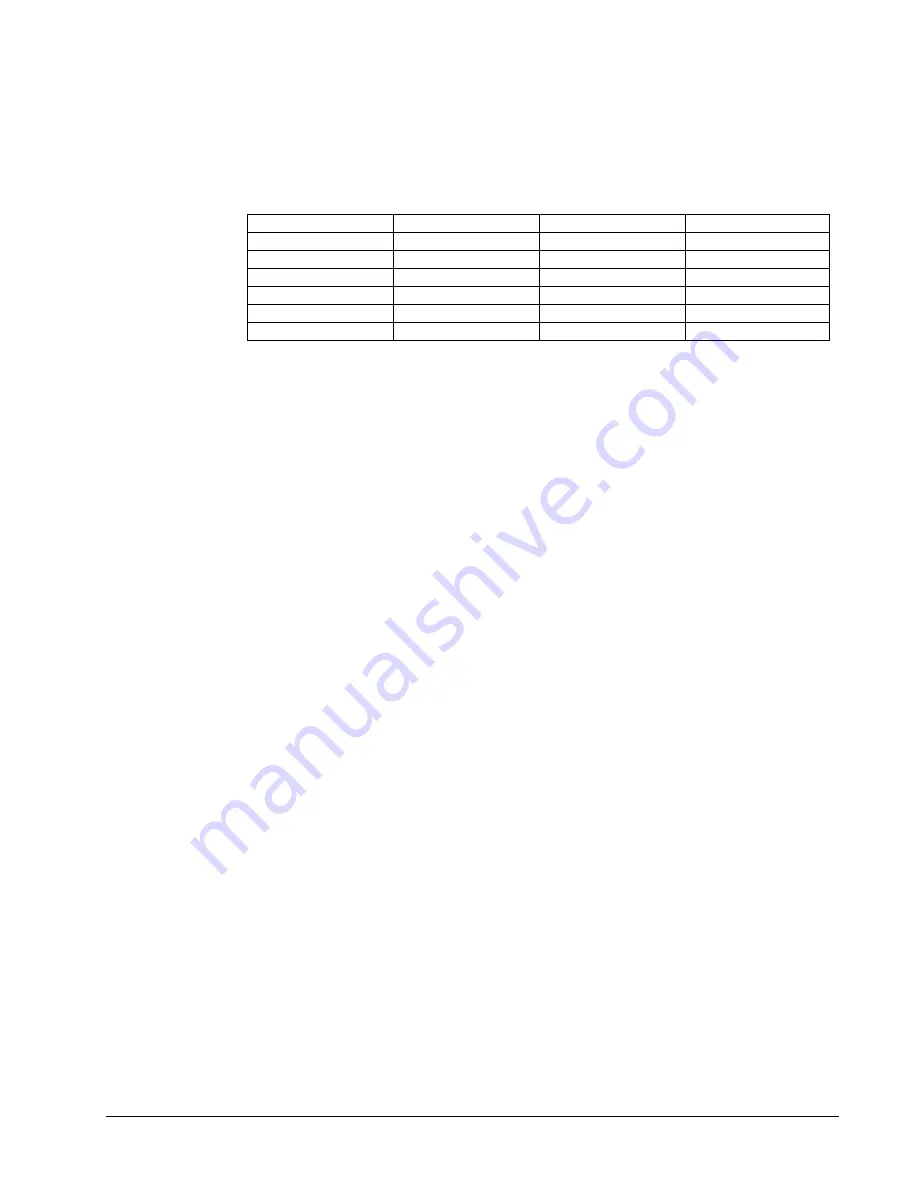
CDS-3310
Chapter
2 Getting Started
i
13
jerky motion in one direction but smooth in the other, and the last (correct) combination
results in smooth movement in both directions. The following table will help you connect all
six combinations:
Aid to connect all six motor power lead combinations
Phase A
Phase B
Phase C
Behavior
Power Lead 1
Power Lead 2
Power Lead 3
Power Lead 1
Power Lead 3
Power Lead 2
Power Lead 2
Power Lead 3
Power Lead 1
Power Lead 2
Power Lead 1
Power Lead 3
Power Lead 3
Power Lead 1
Power Lead 2
Power Lead 3
Power Lead 2
Power Lead 1
Set the PID gains to zero KPX=0; KDX=0; KIX=0. For each combination, set an offset OF2.
If the motor does not move smoothly, go to the next combination. If it does move smoothly,
try the other direction with OF-2. If it is smooth, you have found the correct combination. If
not, go to the next combination.
Step C2.
Test wiring automatically
The controller has been programmed to test whether the Hall commutation order is correct.
To
test the commutation for the X axis, issue the BS command (BSX= n,m). The controller
will attempt to move the motor through one revolution. If the motor is unable to move, the
controller will return “unknown Hall transition”, check wiring, and execute BS again. It may
be necessary to issue more voltage to create motion. The default for the BS command is
BSn=0.25,1000 which will send 0.25 volts to the amplifier for 1 second. BSX=0.5,300 will
issue 0.5 volts from the controller for 300 milliseconds. If the controller is able to move the
motor and the Hall transitions are not correct, the controller will alert the operator and
recommend which motor phases to change. For example, the controller might return “Wire A
to Terminal B, Wire B to Terminal A.” If the controller finds that the commutation order is
correct, but the motor would run away due to positive feedback, the controller will prompt the
user to “Wire Phase B to C and C to B. Exchange Hall Sensors A and B…”. After making
any necessary changes to the motor phase wiring, confirm correct operation by reissuing the
BS command. Once the axis is wired correctly, the controller is ready to perform closed-loop
motion.
Step 8. Close the Loop
Step A.
Test feedback polarity
To test the polarity of the feedback, set small gains KPX=6; KDX=64 and command a move
with the instruction:
PRX=1000 <CR>
Position relative 1000 counts
BGX <CR>
Begin motion on A axis
When the polarity of the feedback is wrong, the motor will run away and the controller will
disable the motor when the position error exceeds 2000 counts. If the motor runs away, the
polarity of the loop must be inverted.
Step B.
Invert feedback polarity (if necessary)
When the polarity of the feedback is incorrect, the user must invert the loop polarity. The
polarity reversal may be done with the encoder. If you are using a single-ended encoder,
interchange the signal CHA and CHB. If, on the other hand, you are using a differential
encoder, interchange only CHA+ and CHA-. The loop polarity and encoder polarity can also
be affected through software with the MT, and CE commands (see the Command Reference).
Содержание CDS-3310
Страница 26: ...18 i Chapter 2 Getting Started CDS 3310 THIS PAGE LEFT PLANK INTENTIONALLY...
Страница 32: ...24 i Chapter 3 Connecting I O CDS 3310 THIS PAGE LEFT PLANK INTENTIONALLY...
Страница 124: ...CDS 3310 Chapter 8 Hardware Software Protection i 63 THIS PAGE LEFT PLANK INTENTIONALLY...
Страница 138: ...CDS 3310 Chapter 10 Theory of Operation i 77 THIS PAGE LEFT BLANK INTENTIONALLY...