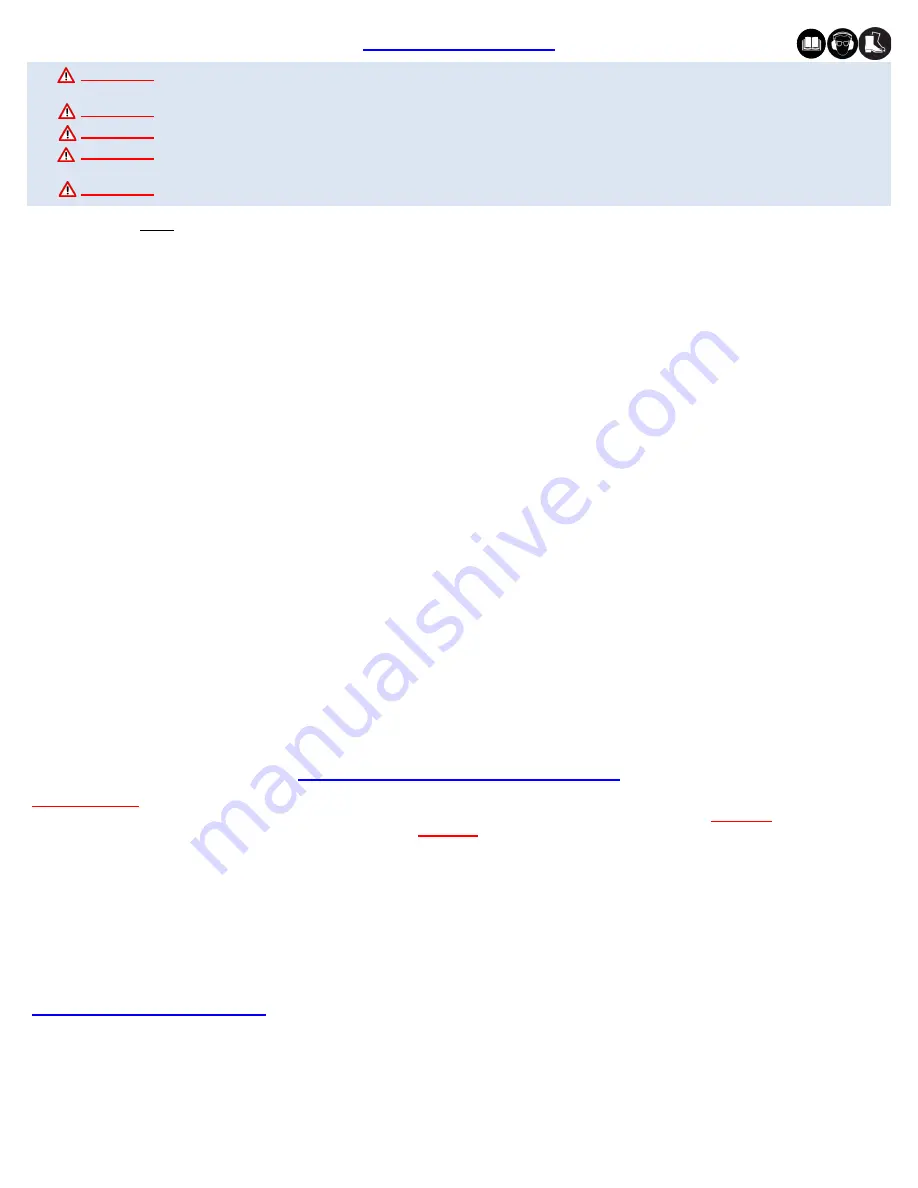
10
REV. 6/22
GB786/204 INSTALLATION TOOL
TORQUE SPECIFICATIONS
Button Head Cap Screws (402482) = 35
-
40 inch lbs. (3.95
-
4.52 Nm)
(Do NOT over
-
tighten).
Socket Head Cap Screws (400062 & 400063) = 40 inch lbs. (4.52 Nm).
Packing Plug (870166) = 45 foot lbs. (61 Nm).
Flat Head Cap Screws (S700) = 40 inch lbs. (4.52 Nm).
Slotted Nut (S302) = 50
-
59 inch lbs. (5.65
-
6.67 Nm)
DAILY MAINTENANCE
WARNING
:
Tool must be maintained in a safe working condition at all times and examined on a daily basis for damage or
wear. Any repair must be done by qualified personnel trained on Gage Bilt procedures.
WARNING
:
Excessive contact with hydraulic oil and lubricants must be avoided.
WARNING:
Maintenance personnel
MUST
read and understand all warnings and cautions.
WARNING
:
Disconnect tool from its power source before performing maintenance, cleaning or when replacing worn or
damaged components. Severe personal injury may occur if power source is not disconnected.
WARNING:
Read material Safety Data Sheet documents for all applicable materials
Note:
•
Dispose of hydraulic oil in accordance with manufacture safety datasheet.
•
All tool materials are recyclable except rubber o
’
rings, seals and wipers.
The performance of any tool depends upon good maintenance practices. Following these minimal requirements daily will extend the
life of your tool.
*Only use a clean dry air supply set at 90
-
100 p.s.i. (6.2
-
6.9 bar) Max. equipped with a filter
-
regulator to prevent wear.
*Check tool and nose assembly for damage. (Replace/Repair if necessary). See Overhaul (pg. 14
-
15) for tool repair.
*Inspect all hoses and couplings for wear, damage and leaks. Replace/Repair if necessary. (
See hydraulic thread preparation below)
.
*Verify that hydraulic hose fittings and couplings, air and electrical connections are secure. Tighten, Replace or Repair if necessary
(
See hydraulic thread preparation below)
.
*Cycle the tool several times to assure there are no leaks during use.
*
Only use a hydraulic power source equipped with relief valves and pressures set within specific limits (See required max pressure
for pull and return).
* Keep hydraulic system free of dirt. Avoid letting couplers contact a dirty floor.
* Do not use as a hammer to force fasteners into holes or otherwise abuse tool.
* Proper care by operators is necessary in maintaining full productivity and reducing downtime.
*Keep nose assemblies, especially jaws, clean and free of chips and debris. Lube jaws and collet surfaces that jaws ride on with
light machine oil on a daily basis.
*All Screwed End Caps, Base Covers, Air Fittings, Air Actuators, Screws and Nose Assemblies are to be examined at the end of
each working shift to check that they are secure.
SEE TROUBLESHOOTING (PG. 13) AND OVERHAUL (PG. 14
-
15) FOR FURTHER GUIDANCE.
HYDRAULIC THREAD PREPARATION
IMPORTANT:
Be sure to use thread sealant on all hydraulic fittings, Loctite® 545 or equivalent or a non
-
hardening Teflon® thread
compound such as Slic
-
tite®. Tighten until fitting feels snug and then continue to tighten 1/2 to 1 full turn.
CAUTION:
Over tightening
can easily distort the threads. DO NOT USE TEFLON® TAPE.
CAUTION:
Teflon® tape is an excellent thread sealer, however, if it is not
properly applied, pieces of Teflon® may enter the hydraulic system and cause malfunction or damage.