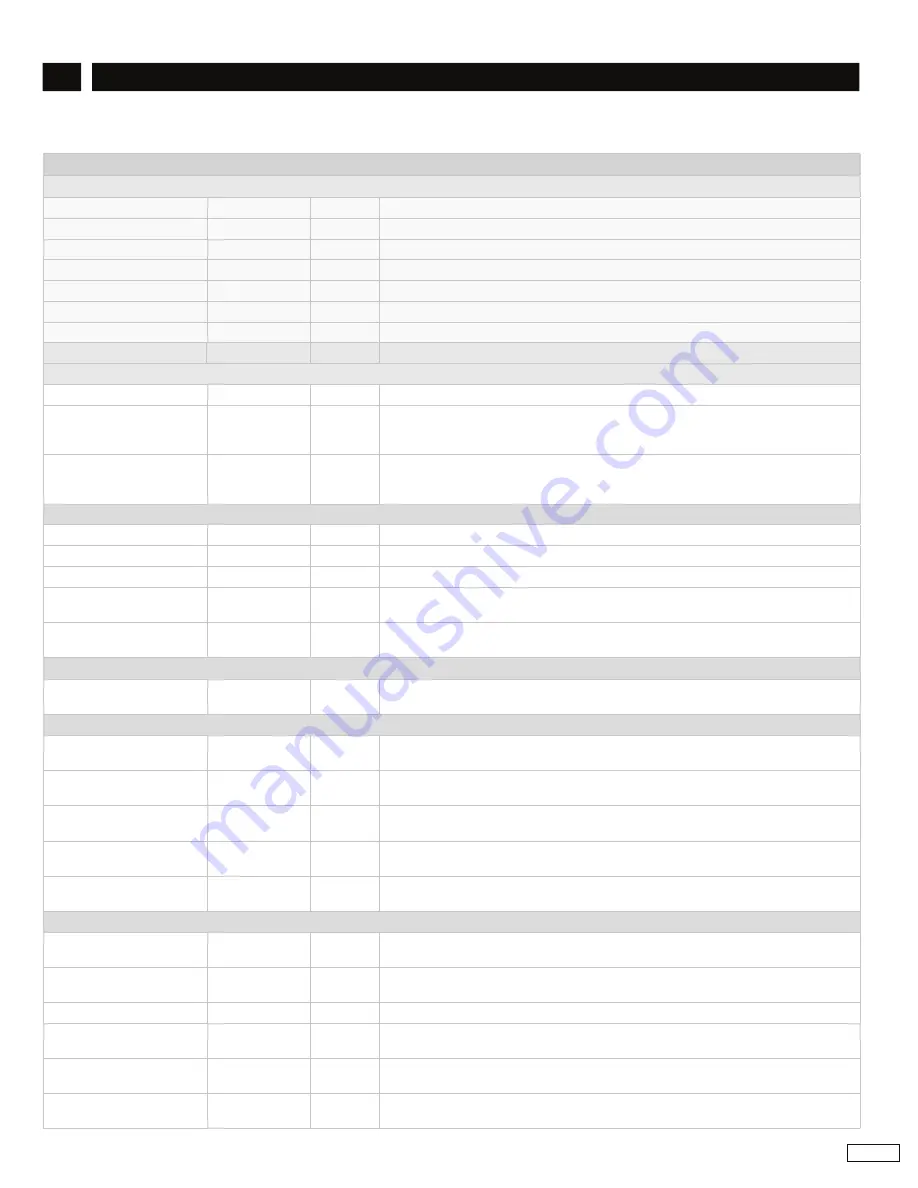
16
Governors America Corp. © 2021 Copyright All Rights Reserved
Enhanced Electronic Governor EEG7000 with GAConfig Tool 8-2021-D6
PIB1009
QUick confiGUration - engine tuning
System Status - engine and actuator - Displays current status similar to Dashboard
Magnetic Pickup Frequency Display only
Hz
Current engine speed
Actual Engine Speed
Display only
rpm
Current engine speed
Desired Engine Speed
Display only
rpm
Set governing speed
Operator Requested Speed
Display only
rpm
Requested governing speed
Selected Speed Mode
Display only
Speed 1, 2, 3, Variable
Actuator Duty Cycle
Display only
%
Actuator duty cycle
Actuator Current
Display only
A
Current draw of actuator
Parameter
min - max
DefaUlt noteS
System Setup
Flywheel Teeth
60 - 250
120
Number of teeth on the flywheel.
The system can govern up to 12000 Hz.
Overspeed
150 - 6000*
1800
Set rpm to cause automatic actuator shut down. Set value low enough to prevent
mechanical damage but high enough to allow realistic load rejection speeds without
stopping engine. Begin by setting at no more than 25 % above rated speed.
Fuel Limit
0 - 100 %
100
Maximum fuel (actuator duty cycle) allowed during governing. Prevents over fueling
after engine has started. During normal starting cycles and short load step the function
will not engage since there is a 1 second delay.
Start-Up / ramp control
Actuator Start Fuel
0 - 100 %
100
Actuator start point during cranking.
Actuator Ramp Rate
1 - 100 %/s
10
Fuel (actuator duty cycle) ramp rate during cranking.
Starter Cutoff
100 - 1000 rpm
400
Crank termination speed in rpm.
Acceleration
25 - 2000 rpm/s
300
Controls rate of acceleration in engine speed. A lower value rpm/s allows for a gradual
increase in engine speed while a larger value of rpm/s provides faster acceleration
Deceleration
25 - 2000 rpm/s
300
Controls rate of deceleration in engine speed. Lower rpm/s allows gradual decrease in
response to engine speed while higher rpm/s create more rapid deceleration.
fixed Speed
Speed 1
Speed 2, 3
0 - 6000*
150 - 6000*
1500
1500
Set engine speeds.
variable Speed
Variable Speed Input Mode
4 - 20 mA or
0 - 5 V DC
0 - 5 V DC Sets variable speed input signal to 0 - 5 V DC or 4 - 20 mA
Speed Minimum
Speed Maximum
150 - 6000*
150 - 6000*
1500
1500
Minimum and maximum speed settings.
Variable Speed Start Gain
Variable Speed End Gain
1 - 100
0 - 100
50
50
Gain used when at the minimum speed while in variable speed.
Gain used when at the maximum speed while in variable speed.
Input Minimum
0 - 75 %
0
Sets variable input start position based on current value. Range: 0 to 75 % and must be
25 % apart from end position. Use the Calibrate button to set automatically.
Input Maximum
25 - 100 %
100
Sets variable end position based on the current value. Range: 0 to 75 % and must be
25 % apart from end position. Use the Calibrate button to set automatically.
tuning
Gain 1, 2, 3 (P)
1 - 100
50
Gain determines how fast the controller responds to transient load changes or when a
load disturbance occurs. Applicable to related Speed 1, 2, or 3.
Stability (I)
0 - 100
50
Stability changes steady state response of the engine. Increasing stability brings the
system to steady state faster and decreasing causes a gradual transition.
Deadtime (D)
Low - High
High
Deadtime
Lead Circuit
Select -
Deselect
Select
Lead Circuit increases the range of Gain adjustment increasing the responsiveness of
the governor. Select Lead Circuit if slow or moderate hunting and higher Gain.
Light Force Governing
Select -
Deselect
Deselect
Light Force Governor improves performance when controlling small or low current actu-
ators (GAC T1 ATB, ALR/ALN, 100/103/104 series and normally closed actuators).
Speed Anticipation
Select -
Deselect
Deselect
Speed anticipation reduces rpm recovery time during high load transients and requires
both no load (NLCU) and full load current (FLCU) values are entered.
GAC
onfig
TOOl - SETTING All PARAmETERS
The
gives you access to all the parameters from one menu location. Parameters are grouped by function
and relate directly to the GAConfig Tool groups on other tabs. The menu does not display you all the error messages the core menus
do. Parameter values may be updated by the software if they interfere with other parameters.
14