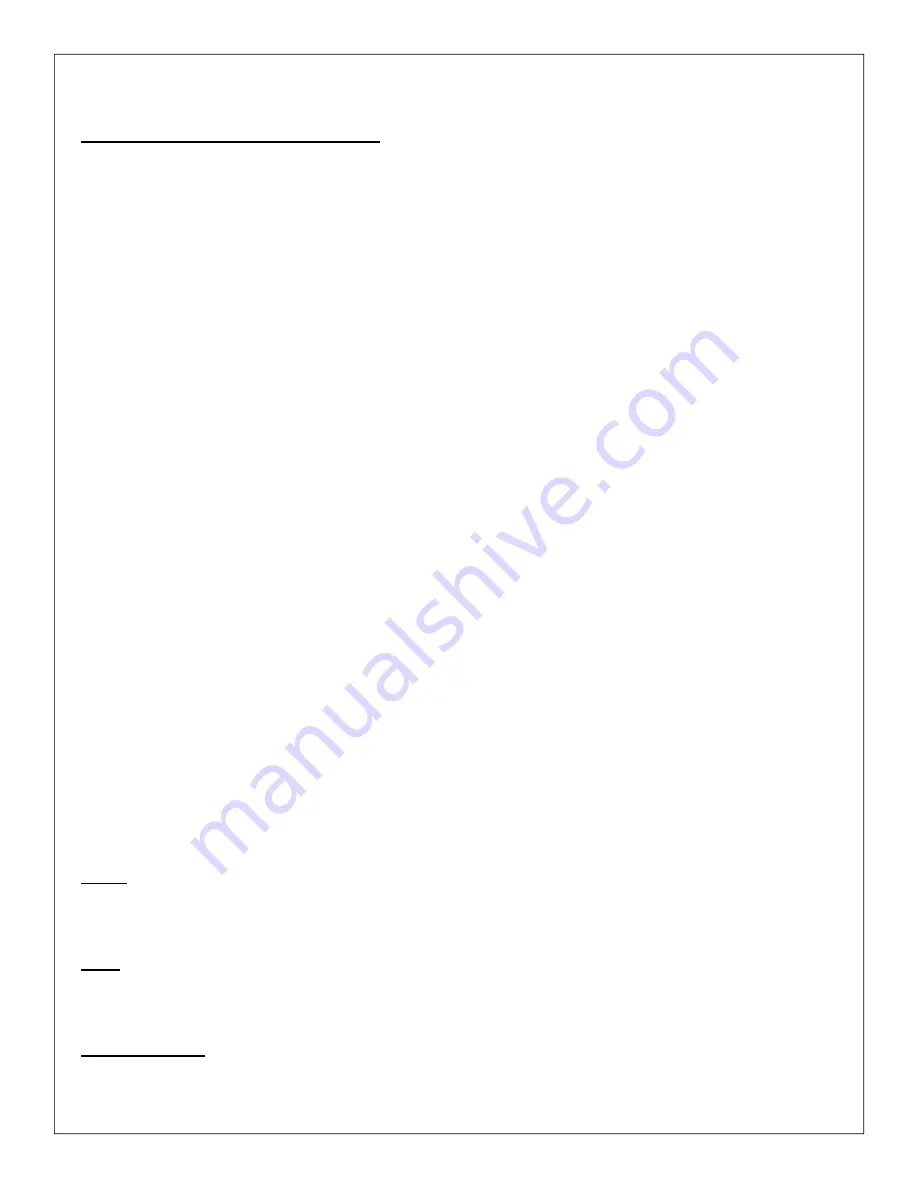
Page 6
Installation
Track Power to Battery Power Conversion
All track powered locomotives are very simple, electrically. Track power is picked up from the rails via pickups and
usually connected directly to the motor. Sometimes there are switches in the circuit to reverse polarity or turn off
track power. These connections need to be modified in order to properly connect the battery powered driver
board.
Converting to battery power consists of these basic steps.
1. Determine battery voltage requirements.
Before you disturb any wiring, run your locomotive at the fastest speed you like to run on your layout and
measure the track voltage. Add at least 2 volts to this measurement to account for low batteries and driver
losses. If using NiCad or NiMh batteries, round this value up to the nearest 1.2v increment, and you have the
number of cells you need. For lithium cells, round up to the nearest 3.7v increment.
For example: Track voltage measures 11.6V at speed. (11.6 + 2)/ 1.2 = 11.3. You will need at least 12 NiMh
cells. 12 X 1.2V = 14.4V. (14.4V is a popular value for steam locomotives. Many critters can run on 12V. Die-
sels usually require 18V or more).
2. Disconnect the track power pickups.
By isolating your locomotive from track power, you can run more than one locomotive on the same track at
the same time, either battery powered or track powered. If you don’t do this, your battery will be directly con-
nected to your track power supply, resulting in damage. Note that in doing this, you have also removed power
from all lighting circuits, smoke units, and any other accessories that were running from track power. For bat-
tery power, smoke units are usually not used due to the high current requirements that will quickly drain the
battery pack. Understanding existing wiring and/or circuit boards without documentation can be difficult. You
may choose to just remove it all and wire directly to the things you can see and understand.
3. Find a direct connection to the motor.
The output of the controller needs to be connected directly to the motor. All other control boards and switches
should be removed from the circuit. Depending on the design of the locomotive, this may be an extremely
simple process, or it may be difficult. Some motor blocks make it very simple. You will find two pairs of wires.
One set goes to the track pickups, and the other goes to the motor. You can verify which pair goes to the
track pickups using a continuity checker or ohmmeter. Track pickups will have continuity from one pin to one
set of wheels. The motor will read a small resistance value across the two wires (e.g. 18 ohms). Simply dis-
connect the track pickup pair and connect the motor pair to the controller.
4. Install the discrete components and wire them together
(battery pack, power on/off switch, fuses, charging jack, controller, Receiver, and lights)
Installing the new components is a packaging exercise. Where will it all fit? Space for the battery pack and
control board and receiver is usually the biggest consideration. For smaller locos you may need to install
some of all of the system in a trailing car. The G-Scale Graphics “Battery Power Conversion Module” makes
installation easier in many cases by putting the on/off switch, fuse, and charging jack all one small circuit
board with screw terminals to eliminate soldering.
Wiring
Always use stranded wire and tin the ends with solder prior to making any connections. Wiring for the power input
and motor output circuitry on terminals 18 thru 21 needs to be heavier gauge wire (20 or 22 Ga.) Any wiring con-
nections or splices not directly connected to a component must be covered. Use heat shrink tubing or wire nuts.
Skills
All connections to the RailBoss Control can be made via screw terminals. However, basic wiring and soldering
skills may be required to make proper connections to the power on/off switch and charging jack. Some drilling and
minor fabrication or modifications to the unit under conversion may also be required.
Tools & Materials
A low wattage soldering iron, side cutters, needle-nose pliers, wire strippers, a 1/16” or 5/64” slotted screwdriver,
resin core solder, 22 Ga. Wire, and heat shrink tubing are recommended to properly complete the wiring. A suit-
able drill and double-sided foam tape may be useful for mounting components.