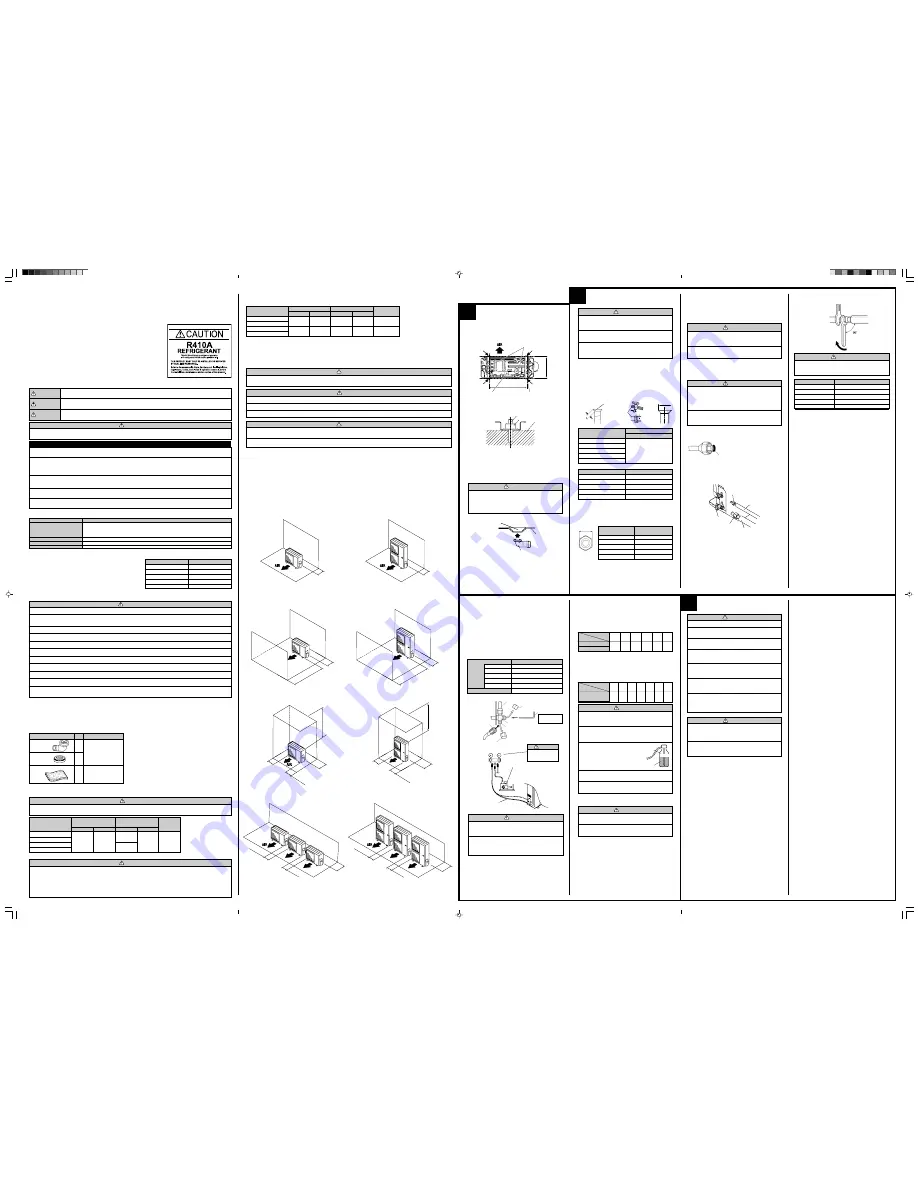
*
If the space is larger than that is stated, the condition
will be the same as that there are no obstacles.
CONNECTION PIPE REQUIREMENT
CAUTION
Install heat insulation around both the gas and liquid pipes. Failure to do so may cause water leaks.
Use heat insulation with heat resistance above 120 °C. (Reverse cycle model only)
In addition, if the humidity level at the installation location of the refrigerant piping is expected to exceed 70%, install heat
insulation around the refrigerant piping. If the expected humidity level is 70-80%, use heat insulation that is 15 mm or thicker
and if the expected humidity exceeds 80%, use heat insulation that is 20 mm or thicker.
If heat insulation is used that is not as thick as specified, condensation may form on the surface of the insulation.
In addition, use heat insulation with heat conductivity of 0.045 W/(m·K) or less (at 20 °C).
•••••
Use pipe with water-resistant heat insulation.
CAUTION
The maximum lengths of this product are shown in the following table. If the units are further apart than this, correct
operation can not be guaranteed.
ELECTRICAL REQUIREMENT
•••••
Electric wire size and breaker capacity:
SELECTING THE MOUNTING POSITION
Decide the mounting position with the customer as follows:
WARNING
Select installation locations that can properly support the weight of the indoor and outdoor units. Install the units securely so
that they do not topple or fall.
CAUTION
1
Do not install where there is the danger of combustible gas leakage.
2
Do not install the unit near heat source of heat, steam, or flammable gas.
3
If children under 10 years old may approach the unit, take preventive measures so that they cannot reach the unit.
•••••
Always use H07RN-F or equivalent to the connection cord.
•••••
Install all electrical works in accordance to the standard.
•••••
Install the disconnect device with a contact gap of at least 3 mm in all poles nearby the units. (Both indoor unit and outdoor unit)
•••••
Install the circuit breaker nearby the units.
WARNING
1
Install the unit where it will not be tilted by more than 3˚. However, do not install the unit with it tilted towards the side
containing the compressor.
2
When installing the outdoor unit where it may exposed to strong wind, fasten it securely.
(1) Install the outdoor unit in a location which can withstand the weight of the unit and vibration, and which can install horizontally.
(2) Provide the indicated space to ensure good airflow.
(3) If possible, do not install the unit where it will be exposed to direct sunlight.
(If necessary, install a blind that does not interfere with the airflow.)
(4) Do not install the unit near a source of heat, steam, or flammable gas.
(5) During heating operation, drain water flows from the outdoor unit.
Therefore, install the outdoor unit in a place where the drain water flow will not be obstructed. (Reverse cycle model only)
(6) Do not install the unit where strong wind blows or where it is very dusty.
(7) Do not install the unit where people pass.
(8) Install the outdoor unit in a place where it will be free from being dirty or getting wet by rain as much as possible.
(9) Install the unit where connection to the indoor unit is easy.
INSTALLATION PROCEDURE
1
OUTDOOR UNIT
INSTALLATION
1. OUTDOOR UNIT PROCESSING
(1) Outdoor unit to be fasten with bolts at the four places indicated by the
arrows without fail.
(2) Fix securely with bolts on a solid block. (Use 4 sets of commercially
available M10 bolt, nut and washer.)
(3) Since the drain water flows out of the outdoor unit during heating
operation, install the drain pipe and connect it to a commercial 16 mm
hose. (Reverse cycle model only)
(4) When installing the drain pipe, plug all the holes other than the drain
pipe mounting hole in the bottom of the outdoor unit with putty so
there is no water leakage. (Reverse cycle model only)
Drain pipe mounting hole
Base
Drain pipe
Bottom side
Drain cap
mounting place
Drain pipe
mounting place
650 mm
4-ø 12 hole
370 mm
Bolt
Nut
Block
CAUTION
When the outdoor temperature is 0 °C or less, do not use
the accessory drain pipe and drain cap. If the drain pipe
and drain cap are used, the drain water in the pipe may
freeze in extremely cold weather. (Reverse cycle model
only)
(Continued to the next page)
2
CONNECTING THE PIPE
2. BENDING PIPES
CAUTION
1
To prevent breaking of the pipe, avoid sharp bends.
Bend the pipe with a radius of curvature of 150 mm or
over.
2
If the pipe is bent repeatedly at the same place, it will
break.
CAUTION
1
Do not use mineral oil on flared part. Prevent mineral
oil from getting into the system as this would reduce
the lifetime of the units.
2
While welding the pipes, be sure to blow dry nitrogen
gas through them.
3
The maximum lengths of this product are shown in the
table. If the units are further apart than this, correct
operation can not be guaranteed.
1. FLARING
(1) Cut the connection pipe to the necessary length with a pipe cutter.
(2) Hold the pipe downward so that cuttings will not enter the pipe and
remove the burrs.
(3) Insert the flare nut (always use the flare nut attached to the indoor
and outdoor units respectively) onto the pipe and perform the flare
processing with a flare tool.
Use the special R410A flare tool, or the conventional flare tool.
When using conventional flare tools to flare R410A pipes, the dimension
A should be approximately 0.5 mm more than indicated in the table (for
flaring with R410A flare tools) to achieve the specified flaring. Use a thick-
ness gauge to measure the dimension A.
Pipe outside
diameter
Width across flats
of Flare nut
Width across flats
Check if [L] is flared uniformly
and is not cracked or scratched.
B
Die
A
Pipe
3. CONNECTION PIPES
Outdoor unit
(1) Detach the caps and plugs from the pipes.
CAUTION
1
Be sure to apply the pipe against the port on the in-
door unit and the outdoor unit correctly. If the centering
is improper, the flare nut cannot be tightened smoothly.
If the flare nut is forced to turn, the threads will be
damaged.
2
Do not remove the flare nut from the indoor unit pipe
until immediately before connecting the connection
pipe.
(2) Centering the pipe against port on the outdoor unit, turn the flare nut
with your hand.
To prevent gas leakage, coat the flare
surface with alkylbenzene oil (HAB).
Do not use mineral oil.
(3) Tighten the flare nut of the connection pipe at the outdoor unit valve
connector.
(4) When the flare nut is tightened properly by your hand, use a torque
wrench to finally tighten it.
Torque wrench
Holding spanner
Body side
CAUTION
Hold the torque wrench at its grip, keeping it in the right
angle with the pipe, in order to tighten the flare nut
correctly.
Flare nut
Tightening torque
6.35 mm (1/4 in.) dia.
9.52 mm (3/8 in.) dia.
12.70 mm (1/2 in.) dia.
15.88 mm (5/8 in.) dia.
19.05 mm (3/4 in.) dia.
6.35 mm (1/4 in.)
9.52 mm (3/8 in.)
12.70 mm (1/2 in.)
15.88 mm (5/8 in.)
19.05 mm (3/4 in.)
0 to 0.5
Pipe outside diameter
Dimension A
(mm)
Flare tool for R410A, clutch type
Pipe outside diameter
Dimension B
(mm)
0
-0.4
6.35 mm (1/4 in.)
9.52 mm (3/8 in.)
12.70 mm (1/2 in.)
15.88 mm (5/8 in.)
19.05 mm (3/4 in.)
17 mm
22 mm
26 mm
29 mm
36 mm
The pipes are shaped by your hands. Be careful not to collapse them.
Do not bend the pipes in an angle more than 90
°
.
When pipes are repeatedly bend or stretched, the material will harden,
making it difficult to bend or stretch them any more. Do not bend or
stretch the pipes more than three times.
14 to 18 N·m (140 to 180 kgf·cm)
33 to 42 N·m (330 to 420 kgf·cm)
50 to 62 N·m (500 to 620 kgf·cm)
63 to 77 N·m (630 to 770 kgf·cm)
100 to 110 N·m (1000 to 1100 kgf·cm)
3-way valve
(Liquid)
Flare nut
Connection pipe
(Liquid)
3-way valve
(Gas)
Flare nut
Connection pipe
(Gas)
Name and Shape
Q’ty
Application
For outdoor unit drain
piping work (May not be
supplied, depending on
the model.)
For filling in a gap at the
entrance of connection
cords
1
2
1
Drain pipe
Drain cap
Insulation (seal)
STANDARD PARTS
The following installation parts are furnished.
Use them as required.
• 30,000 BTU/h class
• 36,000 BTU/h class
• 45,000 BTU/h class
• 54,000 BTU/h class
6.35 mm (1/4 in.)
9.52 mm (3/8 in.)
12.70 mm (1/2 in.)
15.88 mm (5/8 in.)
19.05 mm (3/4 in.)
9.1
13.2
16.6
19.7
24.0
Model Type
Power supply cord (mm
2
)
Connection cord (mm
2
)
Breaker capacity (A)
MAX.
MIN.
MAX.
MIN.
30,000 BTU/h class
4.0
3.5
2.5
1.5
30
36,000 BTU/h class
45,000 BTU/h class
6.0
5.3
3.5
2.5
30
54,000 BTU/h class
MAX.
50 m
70 m
Pipe length
MIN.
5 m
30 m
Maximum height
(between indoor
and outdoor)
Model Type
Liquid
Gas
30,000 BTU/h class
36,000 BTU/h class
9.52 mm (3/8 in.) 15.88 mm (5/8 in.)
45,000 BTU/h class
54,000 BTU/h class
Diameter
SPLIT TYPE AIR CONDITIONER
INSTALLATION INSTRUCTION
SHEET
(PART NO. 9374995011)
WARNING
1
For the air conditioner to operate satisfactorily, install it as outlined in this installation instruction sheet.
2
Connect the indoor unit and outdoor unit with the room air conditioner piping and cords available standards parts. This
installation instruction sheet describes the correct connections using the installation set available from our standard parts.
3
Installation work must be performed in accordance with national wiring standards by authorized personnel only.
4
Also, do not use an extension cord.
5
Do not turn on the power until all installation work is complete.
6
Do not purge the air with refrigerants but use a vacuum pump to vacuum the installation.
7
There is not extra refrigerant in the outdoor unit for air purging.
8
Use a vacuum pump for R410A exclusively.
9
Using the same vacuum pump for different refrigerants may damage the vacuum pump or the unit.
0
Use a clean gauge manifold and charging hose for R410A exclusively.
A
If refrigerant leaks while work is being carried out, ventilate the area. If the refrigerant comes in contact with a flame, it
produces a toxic gas.
•••••
Be careful not to scratch the air conditioner when handling it.
•••••
After installation, explain correct operation to the customer, using the operating manual.
•••••
Let the customer keep this installation instruction sheet because it is used when the air conditioner is serviced or moved.
When there are obstacles at the back side.
4. VACUUM
(1) Remove the cap, and connect the gauge manifold and the vacuum
pump to the charging valve by the service hoses.
(2) Vacuum the indoor unit and the connecting pipes until the pressure
gauge indicates –0.1 MPa (–76 cmHg).
(3) When –0.1 MPa (–76 cmHg) is reached, operate the vacuum pump
for at least 60 minutes.
(4) Disconnect the service hoses and fit the cap to the charging valve to
the specified torque.
(5) Remove the blank caps, and fully open the spindles of the 2-way
and 3-way valves with a hexagon wrench [Torque: 6~7 N·m (60 to
70 kgf·cm)].
(6) Tighten the blank caps of the 2-way valve and 3-way valve to the
specified torque.
5. ADDITIONAL CHARGE
• 30,000 BTU/h class
• 36,000 BTU/h class
Refrigerant suitable for a piping length of 15 m is charged in the outdoor
unit at the factory.
When the piping is longer than 15 m, additional charging is necessary.
For the additional amount, see the table below.
20 to 25 N·m (200 to 250 kgf·cm)
20 to 25 N·m (200 to 250 kgf·cm)
25 to 30 N·m (250 to 300 kgf·cm)
30 to 35 N·m (300 to 350 kgf·cm)
35 to 40 N·m (350 to 400 kgf·cm)
10 to 12 N·m (100 to 120 kgf·cm)
Tightening torque
Lo
Hi
Gauge manifold
Service hose
Vacuum pump
Connecting pipe
Blank cap
Hexagon wrench
3-way valve
Charging port
Cap
Service hose
with valve core
Outdoor unit
Use a 4 mm
hexagon wrench.
Blank
cap
6.35 mm (1/4 in.)
9.52 mm (3/8 in.)
12.70 mm (1/2 in.)
15.88 mm (5/8 in.)
19.05 mm (3/4 in.)
Charging port cap
CAUTION
1
Do not purge the air with refrigerants, but use a vacuum
pump to vacuum the installation! There is no extra re-
frigerant in the outdoor unit for air purging!
2
Use a vacuum pump and gauge manifold and charg-
ing hose for R410A exclusively. Using the same vacuum
for different refrigerants may damage the vacuum pump
or the unit.
6. GAS LEAKAGE INSPECTION
CAUTION
1
When moving and installing the air conditioner, do not
mix gas other than the specified refrigerant R410A
inside the refrigerant cycle.
2
When charging the refrigerant R410A, always use
an electronic balance for refrigerant charging (to
measure the refrigerant by weight).
3
When charging the refrigerant,
take into account the slight change
in the composition of the gas and
liquid phases, and always charge
from the liquid phase side whose
composition is stable.
4
Add refrigerant from the charging valve after the
completion of the work.
5
If the units are further apart than the maximum pipe
length, correct operation can not be guaranteed.
Gas
Liquid
R410A
CAUTION
1
After connecting the piping, check the all joints for gas
leakage with gas leak detector.
2
When inspecting gas leakage, always use the vacuum
pump for pressure. Do not use nitrogen gas.
3
POWER
WARNING
1
The rated voltage of this product is 230 V a.c. 50 Hz.
2
Before turning on, verify that the voltage is within the
198 V to 264 V range.
3
Always use a special branch circuit and install a spe-
cial receptacle to supply power to the air conditioner.
4
Use a special branch circuit breaker and receptacle
matched to the capacity of the air conditioner.
(Install in accordance with standard.)
5
Perform wiring work in accordance with standards
so that the air conditioner can be operated safely and
positively.
6
Install a leakage special branch circuit breaker in
accordance with the related laws and regulations
and electric company standards.
7
The circuit breaker is installed in the permanent wir-
ing. Always use a circuit that can trip all the poles of
the wiring and has an isolation distance of at least
3 mm between the contacts of each pole.
CAUTION
1
The power source capacity must be the sum of the air
conditioner current and the current of other electrical
appliances. When the current contracted capacity is
insufficient, change the contracted capacity.
2
When the voltage is low and the air conditioner is
difficult to start, contact the power company the
voltage raised.
CAUTION
Use a clean gauge mani-
fold and charging hose
for R410A exclusively.
t
For authorized service personnel only.
This installation instruction sheet describes how to install the outdoor unit only. To install the indoor unit, refer to the installation instruction sheet included with
the indoor unit.
250 mm
or more
250 mm
or more
300 mm
or more
100 mm
or more
When there are obstacles at the back and front sides.
When there are obstacles at the back, side(s), and top.
When there are obstacles at the back side with the installation of
more than one unit.
Pipe length
Model type
30,000 BTU/h class
None
200 g
600 g 1000 g 1400 g 40 g/m
36,000 BTU/h class
15 m
20 m
30 m
40 m
g/m
50 m
• 45,000 BTU/h class
• 54,000 BTU/h class
Refrigerant suitable for a piping length of 20 m is charged in the outdoor
unit at the factory.
When the piping is longer than 20 m, additional charging is necessary.
For the additional amount, see the table below.
This air conditioner uses new refrigerant HFC (R410A).
The basic installation work procedures are the same as conventional refrigerant models.
However, pay careful attention to the following points:
1
Since the working pressure is 1.6 times higher than that of conventional refrigerant models, some of the piping and
installation and service tools are special. (See the table below.)
Especially, when replacing a conventional refrigerant model with a new refrigerant R410A model, always replace the
conventional piping and flare nuts with the R410A piping and flare nuts.
2
Models that use refrigerant R410A have a different charging port thread diameter to prevent erroneous charging with
conventional refrigerant and for safety. Therefore, check beforehand. [The charging port thread diameter for R410A is
1/2 UNF 20 threads per inch.]
3
Be more careful that foreign matter (oil, water, etc.) does not enter the piping than with refrigerant models. Also, when
storing the piping, securely seal the openings by pinching, taping, etc.
4
When charging the refrigerant, take into account the slight change in the composition of the gas and liquid phases, and
always charge from the liquid phase side whose composition is stable.
Special tools for R410A
Contents of change
Pressure is high and cannot be measured with a conventional gauge. To prevent erroneous mixing of other
refrigerants, the diameter of each port has been changed.
It is recommended the gauge with seals –0.1 to 5.3 MPa (–76 cmHg to 53 kgf/cm
2
) for high pressure. –0.1 to
3.8 MPa (–76 cmHg to 38 kgf/cm
2
) for low pressure.
To increase pressure resistance, the hose material and base size were changed.
A conventional vacuum pump can be used by installing a vacuum pump adapter.
Special gas leakage detector for HFC refrigerant R410A.
Tool name
Gauge manifold
Charge hose
Vacuum pump
Gas leakage detector
This air conditioner uses new refrigerant HFC (R410A).
DANGER
This mark indicates procedures which, if improperly performed, are most likely to result in the death of or
serious injury to the user or service personnel.
WARNING
This mark indicates procedures which, if improperly performed, might lead to the death or serious injury of
the user.
CAUTION
This mark indicates procedures which, if improperly performed, might possibly result in personal harm to
the user, or damage to property.
250 mm
or more
250 mm
or more
300 mm
or more
AIR
100-300 mm*
250 mm or more
(Service space)
300 mm
or more
600-1000 mm*
AIR
100 mm
or more
600 mm
or more
250 mm or more
(Service space)
100-300 mm*
300 mm
or more
600-1000 mm*
AIR
100 mm
or more
600 mm
or more
100 mm
or more
Pipe length
Model type
45,000 BTU/h class
54,000 BTU/h class
20 m 30 m 40 m 50 m
g/m
60 m 70 m
None
400 g 800 g 1200 g 1600 g 2000 g 40 g/m
Copper pipes
It is necessary to use seamless copper pipes and it is desirable that the amount of
residual oil is less than 40 mg/10 m. Do not use copper pipes having a collapsed,
deformed or discolored portion (especially on the interior surface). Otherwise, the
expansion valve or capillary tube may become blocked with contaminants.
As an air conditioner using R410A incurs pressure higher than when using con-
ventional refrigerant, it is necessary to choose adequate materials.
Thicknesses of copper pipes used with R410A are as shown in the table. Never
use copper pipes thinner than that in the table even when it is available on the
market.
6.35 mm (1/4 in.)
9.52 mm (3/8 in.)
12.70 mm (1/2 in.)
15.88 mm (5/8 in.)
19.05 mm (3/4 in.)
0.80 mm
0.80 mm
0.80 mm
1.00 mm
1.20 mm
Pipe outside diameter
Thickness
Thicknesses of Annealed Copper Pipes (R410A)
DANGER
Never touch electrical components immediately after the power supply has been turned off. Electrical shock may occur. After
turning off the power, always wait 5 minutes or more before touching electrical components.
DANGER
Never touch electrical components immediately after the power supply has been turned off. Electrical shock may occur. After
turning off the power, always wait 5 minutes or more before touching electrical components.
9374995011_IM_front.p65
4/19/05, 9:19 AM
1
Содержание AO*24LMAKL
Страница 5: ...1 SPECIFICATIONS R410A CASSETTE type INVERTER ...
Страница 11: ...2 DIMENSIONS R410A CASSETTE type INVERTER ...
Страница 15: ...3 REFRIGERANT SYSTEM DIAGRAM R410A CASSETTE type INVERTER ...
Страница 19: ...4 CIRCUIT DIAGRAM R410A CASSETTE type INVERTER ...
Страница 25: ...5 DESCRIPTION OF EACH CONTROL OPERATION R410A CASSETTE type INVERTER ...
Страница 47: ...6 REFRIGERANT CAUTION R410A R410A CASSETTE type INVERTER ...
Страница 56: ...7 TROUBLE SHOOTING R410A CASSETTE type INVERTER ...
Страница 91: ...8 APPENDING DATA R410A CASSETTE type INVERTER ...
Страница 110: ...9 INSTALLATION MANUAL R410A CASSETTE type INVERTER ...
Страница 117: ...10 REPLACEMENT PARTS R410A CASSETTE type INVERTER ...
Страница 119: ...Thermistor Heat exchanger temp 2 way valve Liquid 3 way valve Gas 10 02 Thermo Holder Thermistor Outdoor Temp ...
Страница 143: ...2 TOP PANEL removal Remove the 7 mounting screws Remove the TOP PANEL upward FRONT VIEW REAR VIEW 10 26 ...
Страница 158: ...10 41 8 DRAIN PAN removal Remove the DRAIN PAN ASSY DRAIN PAN ASSY ...
Страница 161: ...10 44 11 DRAIN PUMP removal Remove the 2 mounting screws Remove the DRAIN PUMP UNIT DRAIN PUMP UNIT DRAIN HOSE ...
Страница 162: ...1116 Suenaga Takatsu ku Kawasaki 213 8502 Japan Apr 2006 Printed in Japan ...