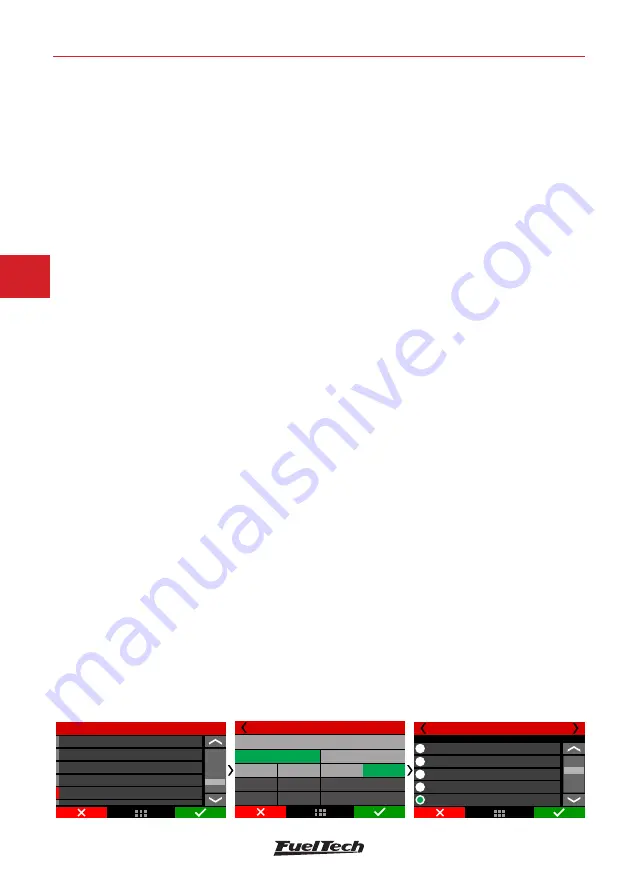
8
EN
WB-O
2
Nano
6. CAN Communication
The WB-O2 has CAN communication, which allows the module to send and
read information from the Power FT ECU’s that are not. Included on the Nano
harness are two 4-way CAN connectors that plug and play with other Nano
units as well as the Power FT ECU’s.
When connected to the CAN port, the WB-O2 Nano can read what the fuel and
the measurement unit (lambda or AFR) that the ECU is set, adjusting itself to
these settings, disabling the analog output and sending the AFR value to ECU
in the range of 5.14 to 149.9 AFR Gas (0,35
λ
to 9,99
λ)
.
When used with the FT250 to FT400 range of ECU’s you will need to use
a 0-5v analog output from the Nano as CAN communication is not possible.
In the CAN network, during the O2 sensor heating period, the value displayed
in the Power FT ECU’s will be equal to 0 (zero) and the back of lambda gauge
will turn yellow.
In case of any error during work, in addition to the warning on WB-O2 Nano
display, the error will be sent via CAN to the Power FT ECU’s and recorded in
"Status Events" log.
To connect the WB-O2 Nano via CAN to Power FT ECU’s simply plug the 4-way
cable to the ECU CAN port.
6.1 Power FT Line Configuration
WB-O2 Nano CAN Communication can be setup through FTManager Software
or through Power FT ECU’s screen.
To setup it through the ECU screen:
Go to “Sensors and Calibration” menu, then “O2 sensor”. Select the position
where this O2 sensor is installed on the engine. Then for CAN network, select
“CAN 2.0”.
O2 Sensor
Ride height
Pitch rate
CAN communication
Clutch pressure
Sensors and Calibration
Cylindrer 2 2/4
White 5: Available
Select O2 sensor Input
CAN 2.0
White 7: Available
White 8: Available
White 6: Available
O2 Sensor 2/4
O2 Sensor General
Left bank
Right Bank
Cylinder 1
Cylinder 5
Cylinder 9
Cylinder 2
Cylinder 6
Cylinder 10
Cylinder 3
Cylinder 7
Cylinder 11
Cylinder 4
Cylinder 8
Cylinder 12