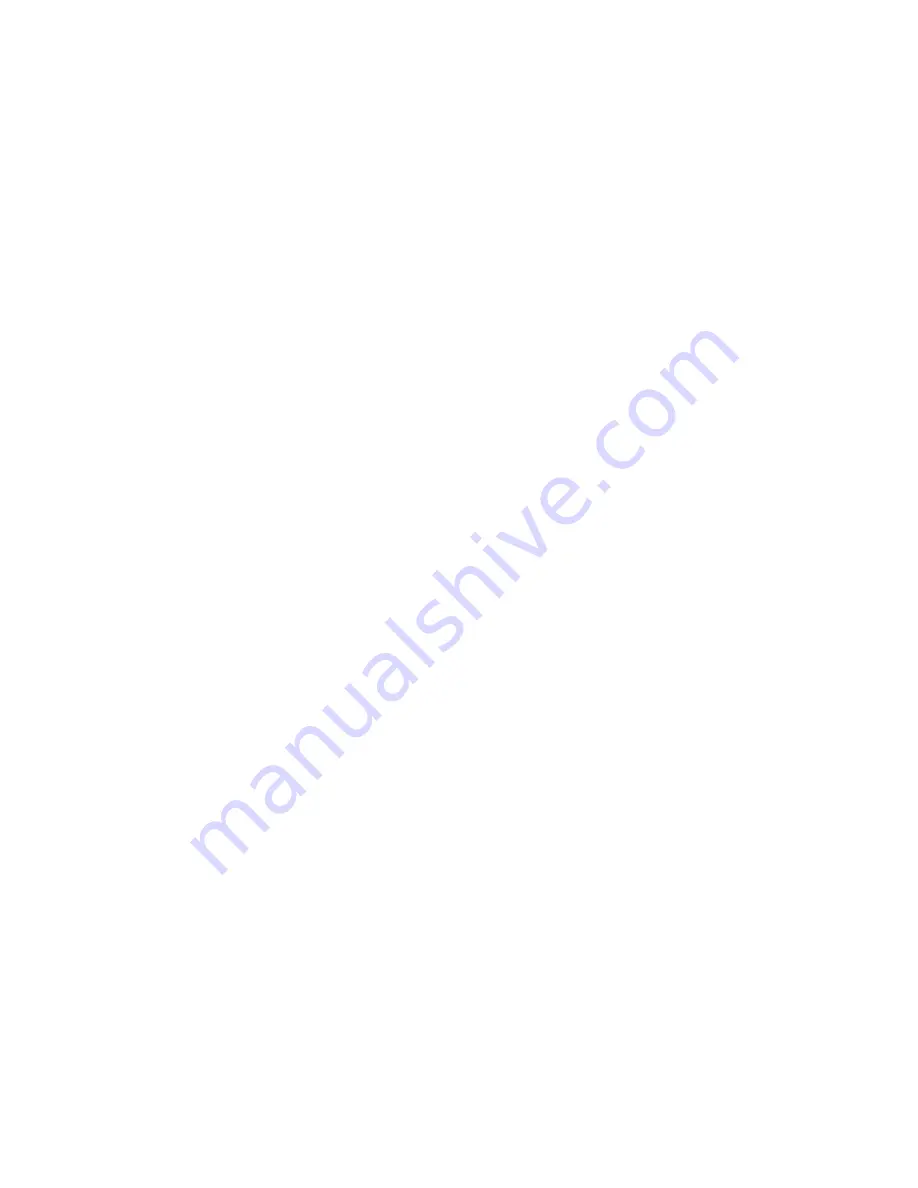
Curtis-Toledo Rotary Compressor
CAP862
Operations and Maintenance Manual
Chapter 4 Page 2
B. Description of system flow chart and component function
1. Air flow path (refer to the flow chart of each type)
1.1. After dust is removed by intake filter, clean air goes through the intake valve into the
compression chamber and is mixed with oil. The mixture is compressed and delivered
though the oil separator, minimum pressure valve, after cooler, and moisture separator.
1.2. Function of parts in the air flow path
(1). Air intake filter
Air intake filter is a suction filter which is a special-purpose air cleaner of the air
compressor. For normal environmental use, clean the dust on the element from inside out
with compressed air every 1,000 hours of operation. The air filter LED lamp “on” implies
that the filter needs to be cleaned or replaced.
(2). Intake Valve
On/Off Load Control
:
for SE20/SE25/SE30/SE40/SE50 models
The solenoid valve is switched by different capacity controls such as: startup, stop, off
load. Each will move the piston of the intake valve. In the mean time, the shuttle valve
keeps minimum pressure to maintain oil circulation.
When system pressure is less than the unload setting value, the solenoid valve is activated,
thus the intake valve is now fully opened. On the other hand, when the value is reached,
the intake valve is closed and the compressor is running off load.
(3). Thermal couple
Lack of oil in circulation will induce high discharge temperature. It will be shown on the
panel through the signal from the thermal couple. General setting value is 230°F (110
℃)
.
Do not operate over this temperature otherwise compressor trip will occur.
(4). Separator (tank)
There is an oil gauge on the bottom side of tank. Maintain the oil level between H-L.
On the bottom there is a drain valve, remember to drain condensate water every time
before startup. In addition, an oil fill hole for oil replacement is on the tank as well.
The larger cross-section area design
of this tank will slow down the compressed air,
this is known as the first stage of air oil separation.
(5). Oil separator
Please refer to the description on oil flow path.
(6). Relief Solenoid Valve
Upon start, stop, or off load running, this valve will release pressure to ensure air end
starts without back pressure or stops under off load running.
(7). Minimum Pressure Valve
Minimum pressure valve is located at the outlet of air discharge from separator tank.
Operating pressure is set to be around 65 PSIG (4.5 kg/cm
2
). The functions of minimum
pressure valve are shown below:
A. To build up oil circulation pressure and operating temperature at start-up.
B. When pressure is over 65 PSIG (4.5 kg/cm
2
), it will reduce flow rate passing and
protect oil separator from damage due to large pressure difference and increase oil
separator efficiency.
C. Prevent back flow under off load running.
Содержание SE Series
Страница 42: ...CAP862 Chapter 8 Page 2 OTES ...