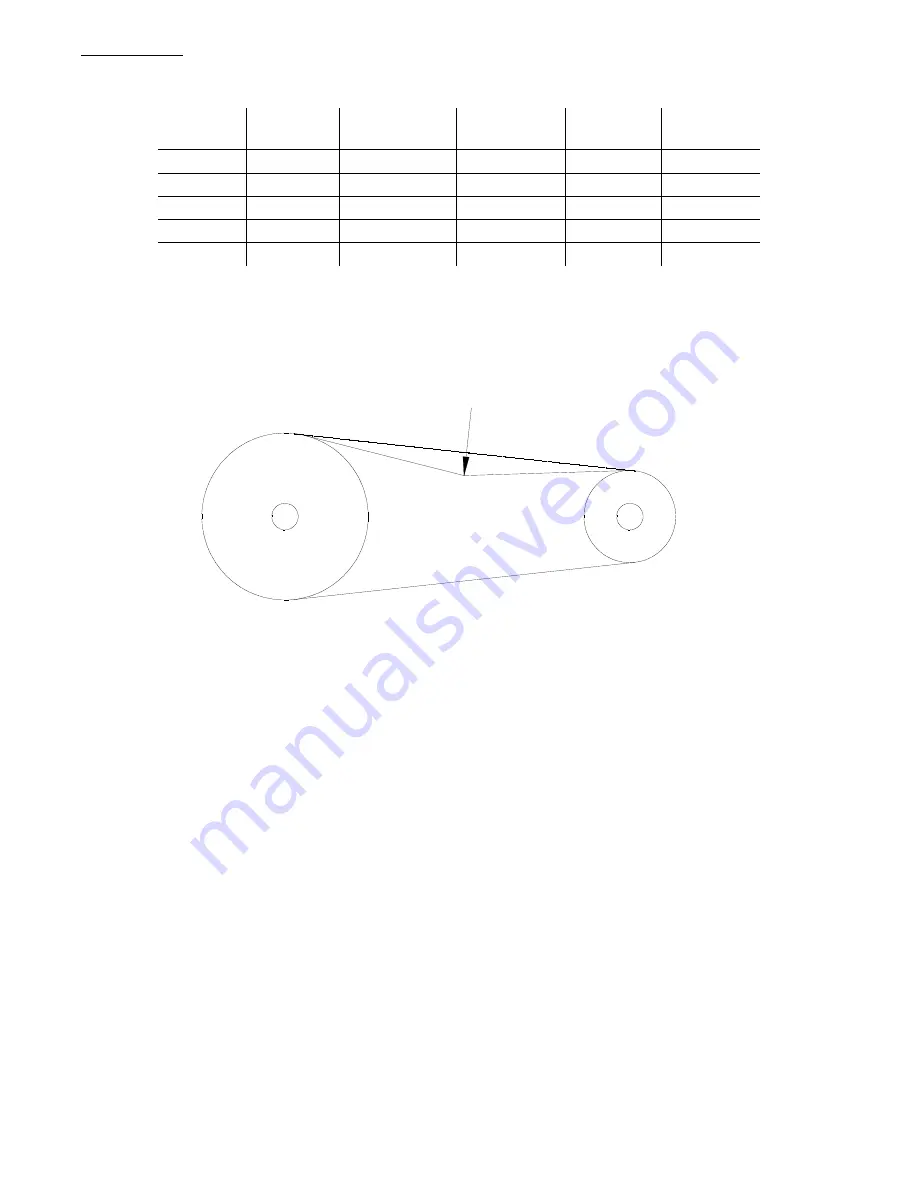
CA / CT SERIES
CAP600
Page
25 of 30
REV D July 2013
Model
HP
Gage
Deflection
Average
Tension
Minimum Maximum
555VT6
5
1/4"
13lb
11lb
14lb
555VT8
5
1/4"
10lb
9lb
12lb
775VT8
7.5
1/4"
10lb
9lb
12lb
1075HT12
10
1/4"
8lb
7lb
10lb
CT Gas
13-14
3/8"
20lb
18lb
23lb
Table (8) CT Belt Tensioning Guide
DIRECTION
OF APPLIED FORCE
Motor
Pulley
Compressor
Pulley
3. Fig (15) Proper belt tensioning
4. At the center of the span, perpendicular to the belt, apply pressure to the outer surface of
the belt tension gauge as shown in figure (13). Apply force to the belt until the rubber ring
on the deflection gauge is located at the original position of the belt. Record the reading on
the belt tension gauge and compare to the chart. Reset the rubber ring on the belt tension
gauge before taking another reading.
5. Adjust the take-up bolt to tighten or loosen the belt tension as required.
6. Finger-tighten ONE motor mounting bolt. Using a straight-edge, check that pulleys are
aligned and adjust motor as necessary.
7. Finger tighten the remaining motor mounting bolts.
8. Using a wrench or air tool, incrementally tighten the mounting bolts in a basic crossing
pattern.
9. Re-mount the belt guard. DO NOT attempt to operate the unit without the belt guard
securely in place.
10. Recheck the tension of the new belts several times in the first month of operation and
adjust if necessary. Thereafter, check belt tension every three months.