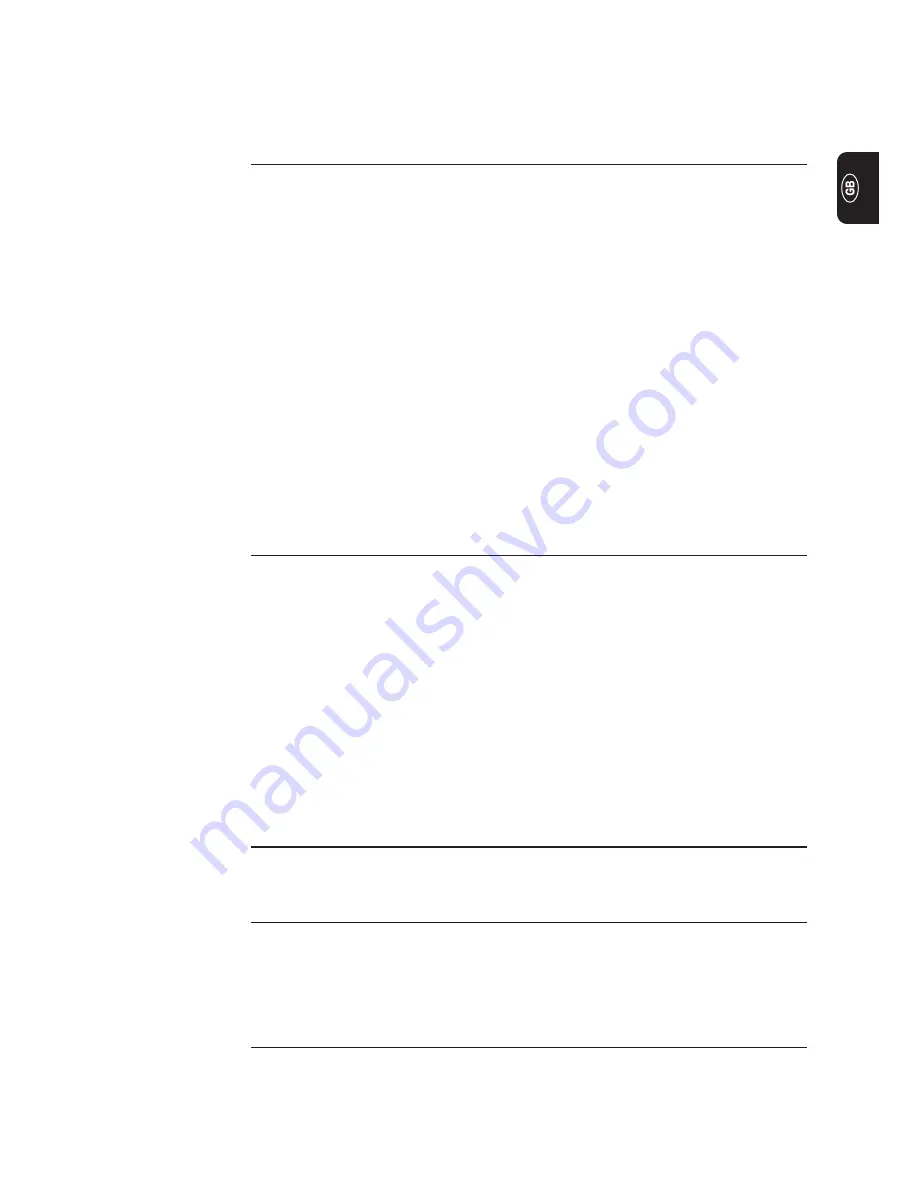
35
Cause:
Phase missing on the power source
Remedy:
Check mains lead, main switch and contactor
Cause:
Secondary commutator faulty
Remedy:
Check commutator
Irregular wirefeed speed, welding wire forms a loop between feed rollers and torch
wire inlet nozzle
Cause:
Wirespool brake applied too lightly/strongly
Remedy:
Adjust wirespool brake
Cause:
The borehole of the contact tube is too narrow
Remedy:
Use correct contact tube
Cause:
Faulty wire feed liner in torch
Remedy:
Check liner for kinks, inner diameter, length, dirt, etc.
Cause:
Feed rollers are unsuitable for the wire being used
Remedy:
Match up feed rollers and welding wire
Cause:
Feed rollers have the wrong contact pressure
Remedy:
Optimize the contact pressure
Cause:
Quality of welding wire is not up to standard
Remedy:
Change welding wire
Cause:
Internal machine fault
Remedy:
Contact After-Sales Service
Wirefeeder motor not running / cannot be adjusted
Ready indicator lights up
Cause:
Faulty fuse F1, F2, F3 or F7
Remedy:
Check fuses
Cause:
Wirefeeder motor faulty
Remedy:
Change wirefeeder motor (After-Sales Service)
Cause:
Wirefeeder adjuster faulty
Remedy:
Change wirefeeder adjuster (After-Sales Service)
Cause:
On separated version: Fault in interconnecting hosepack
Remedy:
Check hosepack connections
Cause:
Internal machine fault
Remedy:
Contact After-Sales Service
Welding wire is welded to the contact tube or weld pool
Cause:
Afterglow time adjuster has not been set to achieve optimum results
Remedy:
Correct afterglow time
Main torch body and hosepack become very hot
Cause:
Design dimensions of the torch are not sufficient for this task
Remedy:
Observe duty cycle and loading limit
Cause:
On water-cooled machines: flow rate too low
Remedy:
Check water level, flow rate and cleanliness
Variosynergic
3400/4000/5000
power source
(continued)