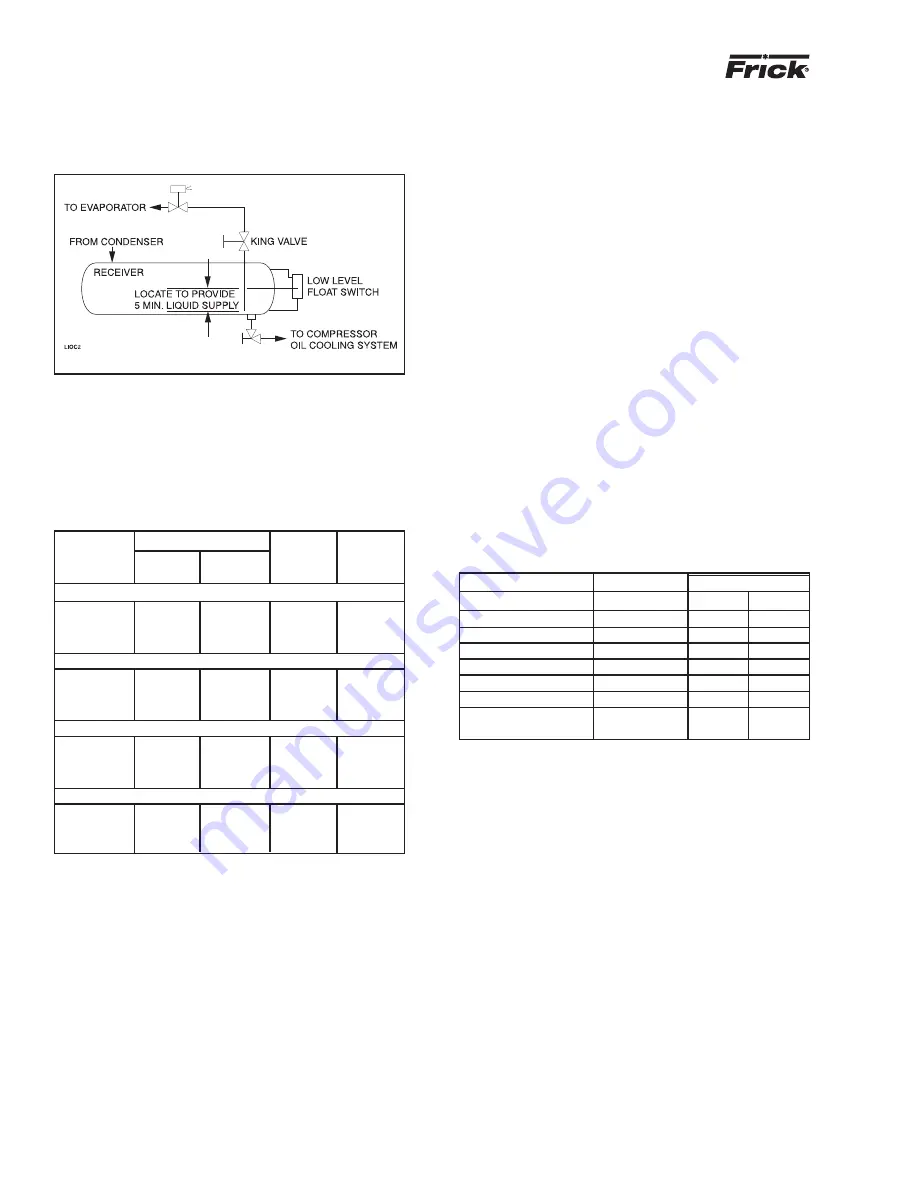
RWB II ROTARY SCREW COMPRESSOR UNITS
INSTALLATION
S70-200 IOM
Page 12
ECONOMIZER - HIGH STAGE (OPTIONAL)
The economizer option provides an increase in system ca-
pacity and efficiency by subcooling liquid from the condenser
through a heat exchanger or flash tank before it goes to the
evaporator. The subcooling is provided by flashing liquid in
the economizer cooler to an intermediate pressure level.The
intermediate pressure is provided by a port located part way
down the compression process on the screw compressor.
As the screw compressor unloads, the economizer port will
drop in pressure level, eventually being fully open to suction.
Because of this, an output from the microprocessor is gen-
erally used to turn off the supply of flashing liquid on a shell
and coil or DX economizer when the capacity falls below
approximately 45%-60% capacity (85%-90% slide valve po-
sition). This is done because the compressor will be more
efficient operating at a higher slide valve position with the
economizer turned off, than it will at a low slide valve position
with the economizer turned on. Please note however that
shell and coil and DX economizers can be used at low com-
pressor capacities in cases where efficiency is not as impor-
tant as assuring that the liquid supply is subcooled. In such
cases, the economizer liquid solenoid can be left open when-
ever the compressor is running.
WATER-COOLED OIL COOLING (Optional)
The plate and shell type water-cooled oil cooler is mounted
on the unit complete with all oil piping. The customer must
supply adequate water connections and install the two-way
water regulating valve if ordered in lieu of a three-way oil
temperature valve. It is recommended (local codes permit-
ting) that the water regulator be installed on the water outlet
connection. Insert the water regulator valve bulb and well in
the chamber provided on the oil outlet connection. Deter-
mine the size of the water-cooled oil cooler supplied with the
unit, then refer to table for the water connection size. The
water supply must be sufficient to meet the required flow.
Frick recommends a closed-loop system for the waterside of
* Based on 100 foot liquid line. For longer runs, increase line
size accordingly.
** For models 60 and 76, contact Frick engineering.
LIQUID LINE SIZES/RECEIVER VOLUME
Liquid line sizes and the additional receiver volume (quanti-
ty of refrigerant required for 5 minutes of liquid injection oil
cooling) are given in the following table:
LIQUID LINE SIZE and RECEIVER VOLUME
LINE SIZE*
POUND
LIQUID
RWB II
SCH 80
OD
PER
VOLUME
MODEL **
PIPE
TUBING
5 MIN.
CU FT
R-717
HIGH STAGE*
100-134
3/4
–
80
2.0
177-270
1
–
140
4.0
316-480
1-1/4
–
250
7.0
R-717
BOOSTER*
100-134
1/2
–
20
0.5
177-270
3/4
–
30
1.0
316-480
1
–
40
1.5
R-22
HIGH STAGE*
100-134
1-1/4
1-1/8
290
4.0
177-270
1-1/2
1-3/8
570
8.0
316-480
2
2-1/2
1,050
14.0
R-22
BOOSTER*
100-134
3/4
7/8
44
0.6
177-270
3/4
7/8
59
0.8
316-480
3/4
7/8
92
1.2
The level-control method utilizes a float level control on the
receiver to close a solenoid valve feeding the evaporator
when the liquid falls below that amount necessary for 5 min-
utes of liquid injection oil cooling. See Figure 10.
Figure 10
the oil cooler. Careful attention to water treatment is essen-
tial to ensure adequate life of the cooler if cooling tower wa-
ter is used. It is imperative that the condition of cooling
water and closed-loop fluids be analyzed regularly and
as necessary and maintained at a pH of 7.4, but not less
than 6.0 for proper heat exchanger life. After initial start-
up of the compressor package, the strainer at the inlet of the
oil cooler should be cleaned several times in the first 24 hours
of operation.
In some applications, the plate and shell oil cooler may be
subjected to severe water conditions, including high tempera-
ture and/or hard water conditions. This causes accelerated
scaling rates which will penalize the performance of the heat
exchanger. A chemical cleaning process will extend the life
of the Plate and Shell heat exchanger. It is important to es-
tablish regular cleaning schedules.
Cleaning: A 3% solution of Phosphoric or Oxalic Acid is rec-
ommended. Other cleaning solutions can be obtained from
your local distributor, but they must be suitable for stainless
steel. The oil cooler may be cleaned in place by back flush-
ing with recommended solution for approximately 30 min-
utes. After back flushing, rinse the heat exchanger with fresh
water to remove any remaining cleaning solution.
NOTE: The water-regulating valve shipped with the unit
will be sized to the specific flow for the unit.
OIL COOLER DATA TABLE
RWB II
TYPICAL
CONNECTION
MODEL
COOLER
INLET
OUTLET
60 - 134 High Stage
116 Plates
3
"
3
"
100 - 270 Booster
66 Plates
2
"
2
"
177/222 High Stage
190 Plates
3
"
3
"
270 High Stage
288 Plates
3
"
4
"
316/399 Booster
56 Plates
3
"
3
"
316/399 High Stage
136 Plates
4
"
5
"
480 Booster
72 Plates
3
"
3
"
480 High Stage
188 Plates
4
"
5
"
Содержание RWB II 480
Страница 42: ...RWB II ROTARY SCREW COMPRESSOR UNITS MAINTENANCE S70 200 IOM Page 42 P I DIAGRAM...
Страница 45: ...RWB II ROTARY SCREW COMPRESSOR UNITS MAINTENANCE S70 200 IOM Page 45 P I DIAGRAM LIQUID INJECTION BOOSTER...
Страница 49: ...RWB II PLUS ROTARY SCREW COMPRESSOR UNITS FORMS S70 200 IOM Page 49 OPERATING LOG SHEET...
Страница 55: ...RWB II ROTARY SCREW COMPRESSOR UNITS NOTES S70 200 IOM Page 55...